How AGVs and cobots can be combined
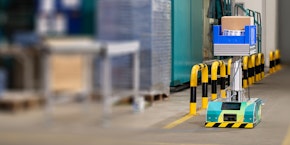
Introduction to automated guided vehicles and cobots
Automated guided vehicles (AGVs) are equipped with drive and load handling devices and are used to automate material transport and handling in processes such as production or order picking. Internal transport in warehouses or factories consists of several AGVs pulling or carrying goods. Automated guided vehicles (AGVs) comprise the following components: one or more AGVs, guidance control, location and position detection systems, data transmission, infrastructure and peripheral equipment. Automated guided vehicles navigate using various technologies such as colour-coded adhesive tapes or inductive guidelines, QR codes, lasers, cameras or GPS. In the European Economic Area, Automated Guided Vehicles and AGVs are subject to the Machinery Directive. A collaborative robot (cobot) is an industrial robot that can operate safely alongside humans in a shared workspace. Unlike autonomous robots, which are programmed for a single task and operate independently, cobots can use advances in mobile technology, artificial intelligence (AI), machine vision, cognitive computing and touch technology to perceive their environment and perform various tasks safely in the vicinity of human workers. Cobots often perform tasks in manufacturing, such as assembly, packaging automation, material handling, machine operation and product quality control. Due to the shortage of skilled labour and rising labour costs, the market for cobots is growing steadily.
Advantages of combining AGVs and cobots
Automated guided vehicles and cobots can be flexibly connected in a production, assembly or storage area, or a cobot can be mounted directly onto an automated guided vehicle.
The combination of automated guided vehicles and collaborative robots offers numerous advantages and can significantly increase efficiency in logistics. One of the main advantages is automated material transport and handling. Autonomous transport systems move materials to workstations where cobots process or assemble them. This reduces the need for human intervention and speeds up the production process. Cobots are also extremely flexible and can be easily reprogrammed for different tasks. The combination of AGVs and cobots creates a highly flexible system that can quickly adapt to changing production requirements. The benefit of cobots is that they can work with people without safety barriers, whereas conventional robot arms cannot. In terms of cost, these two solutions are not really far apart. The disadvantages of cobots vs. robotic arms are lower load capacity and lower precision in the long term. Automation through AGVs and cobots also leads to considerable cost savings. As the need for manual labour is reduced, operating costs decrease and companies can achieve long-term savings as the autonomous systems work continuously and efficiently. The integration of these technologies optimises the workflow, as materials can be delivered just-in-time (JIT). This avoids bottlenecks and minimises stock levels. In addition, the continuous development of technology promotes the introduction of new optimised and more efficient applications. The use of artificial intelligence and machine learning will further increase the performance of AGVs and cobots in the future and make their integration into logistics even more seamless. Companies that rely on the combination of both systems can thus increase their competitiveness.
Examples of application
The combination of automated guided vehicles and collaborative robots has a wide range of applications in various industries. In the automotive industry, automated transport systems move car body parts to assembly lines, where cobots take over and install them. This increases production speed and reduces errors. In large e-commerce warehouses, automated transport systems such as AGVs bring products to picking stations, where cobots pack the items for despatch. This increases warehouse throughput and shortens delivery times. In pharmaceutical production, AGVs transport raw materials to cobots, which carry out precise mixing and filling processes to ensure consistently high product quality and safety. Permanently mounted cobots on mobile, autonomous platforms can be used as autonomous mould setters and tool setters. They transport tools and holders from the tool store to the set-up station and then move autonomously for measurement and cleaning. Finally, they insert the tool into the machine. The autonomous solution enables efficient and precise tool handling, which shortens set-up times and increases machine availability.
Technological challenges and solutions
The integration of driverless transport systems and cobots into operational practice poses a variety of technological challenges that can, however, be overcome with targeted solutions. The seamless cooperation of these systems is ensured through the use of standardised communication protocols and middleware platforms that facilitate interoperability. To ensure safety in the workplace, advanced sensors and safety standards are implemented. In addition, modular and reconfigurable systems as well as the use of AI and machine learning enable driverless vehicles and cobots to adapt flexibly to new tasks and environments. Predictive maintenance systems ensure high reliability and minimised downtimes through predictive maintenance. By taking the above measures, companies can successfully overcome the technological hurdles and fully utilise the benefits of AGVs and cobots.
Tips for the successful integration of AGVs and cobots
The successful integration of automated guided vehicles (AGVs) and cobots in companies requires more than just technical expertise. Change management is key to success with one main person having responsibility to manage the entire project, ensure communication between departments and involve all employees. This person ensures that the new technologies are seamlessly integrated into the existing processes and that potential resistance is recognised and addressed at an early stage. With clearly defined change management and a committed leader, the introduction of AGVs and cobots becomes significantly more efficient and sustainable.