Driverless transport systems - keeping you in the picture
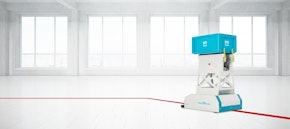
Industry 4.0 leads to boom in automated guided vehicle systems
The first Automated Guided Vehicles (AGVs) were developed in the USA and England in the 1950s. In Germany, the first AGVs were used for transport in the 1960s. Even then, the need to increase productivity led to greater automation of work processes and a reduction in manual work. Automated Guided Vehicles (AGVs) with integrated drive and active or passive load handling devices are used to automate material transport and handling, for example in production or order picking. Driverless transport systems are internal floor-bound conveyor systems and usually consist of several AGVs for pulling or carrying goods. According to the VDI Guideline 2010 "Automated Guided Vehicles", an AGV consists of the following components: one or more Automated Guided Vehicles, a control system, equipment for position determination and position detection, equipment for data transmission, infrastructure and peripheral equipment. In addition, a driverless transport vehicle is subject to the scope of the Machinery Directive in the European Economic Area.
FTS systems have many advantages
The application possibilities of driverless transport systems are constantly being expanded by technical advancements, e.g. in load handling, energy concepts and vehicle navigation. An AGV competes with conventional forklift trucks for internal material flow as well as with continuous conveyors (pallet conveyor technology) and electric suspension conveyors for automated systems. Compared to manual transport with forklift trucks, a driverless transport system has some advantages and is therefore used more and more frequently. Reduced forklift traffic can minimize accidents and transport damage. Due to the savings in personnel costs, especially in shift operation, FTSs often pay for themselves after a few years. In addition, they have high flexibility and availability (24-hour operation) as well as reliability and can also continue to run in emergency operation with reduced throughput capacity.
Effects on internal logistics
Lean production systems such as those in the automotive industry increasingly require forklift-free operation. Due to the rapid evolution of the technology, the vision of a "forklift-free factory" is realizable today. So far, the industry still frequently uses route trains with drivers. However, this could change quickly in the future if route trains become increasingly automated and driverless. In production logistics, too, the last few metres to the assembly line are the real challenge. Driverless transport systems and route trains complement each other perfectly and will thus make a decisive contribution to revolutionising the speed, safety and cost efficiency of production supply and logistics. Modern FTFs are also equipped with laser scanners and various other sensor types. The system automatically detects the reflector marks on walls, shelves, columns, etc. and measures the distance to them. In Natural Navigation, fixed fixtures in the surroundings are used as landmarks. The future of intralogistics is networked, digital and automated. Driverless transport systems will play a decisive role in this.
Different FTS solutions depending on the application
There are driverless transport systems for various functions and applications, such as internal transport vehicles, tractors or assembly platforms. Various applications can be considered, e.g. indoors and outdoors, in industrial environment or a sterile area of a hospital. Further parameters for the design of a driverless transport system are the duration of use, throughput capacity, building layout, drive technology (e.g. combustion engine or electric motor), energy supply (e.g. carried or inductive), vehicle control, safety system, requirements for mobility (linear or surface movement) and data transmission to the control system. The navigation system plays a special role here. Using vehicle computers, software and suitable sensors, the vehicles of the AGV determine their position and course, i.e. actual and target values for direction of travel and speed. There are various technical solutions for this task. In the procedures with physical guidance, the driverless vehicles follow certain installations that are placed on and in the ground along the driving course. These include inductive (including energy transmission to the vehicle), optical and magnetic track guidance. The vehicle can also follow a virtual guideline in the form of software in the vehicle computer without a driver and carry out its transport task, e.g. in the warehouse. Virtual methods include laser, contour-oriented (contour scanning of the environment), radio direction finding and GPS (relatively inaccurate) navigation.
Depending on the scope and purpose, FTSs can be controlled by software, i.e. connected to the IT infrastructure or installed by radio and optical control. FTS solutions without IT are flexible and self-sufficient and can be used in any area of a company.
Future Trends
In general, the trend in industry and logistics is towards increasing automation and digitization with flexibly adaptable systems. Intelligent color factories, the industry standard 4.0 and booming e-commerce - all these trends are leading to increasing scrutiny of processes with regard to automation. Since development is generally moving towards individual system solutions that can adapt flexibly to rapidly changing requirements, autonomous transport robots are also the predominant means of transport of the future. Only they can ensure the necessary flexibility in material flow in intelligent factories and intralogistics environments. Since large fleets of manual forklift trucks will soon be history in these areas, all well-known suppliers of industrial trucks are entering the FTS business. Driverless transport systems are also the focus of large e-commerce companies such as Amazon. The Internet giant Google is also already developing self-propelled shuttles in the area of autonomous driving - although for passenger transport. A quantum leap in technology and the use of driverless transport systems can therefore be expected in the future.