Optimisation of labelling in the warehouse
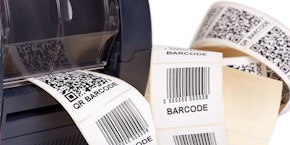
Using a sophisticated system for signage, labelling and marking will help achieve the important goal of maintaining an ordered warehouse in which items can be found easily and quickly.
Different types of labelling
In shelving areas, stick-on labels that can be read with a scanner still predominate, while RFID or electronic shelf labels (ESL or E-Ink labels) are still considered generally as being an exotic option. Signs and information boards, floor and shelf markings as well as cardboard and product labels provide orientation in a warehouse. While signs and information boards can be used to partition a warehouse into different areas, more specific location guidance can be provided by floor and shelf markings that determine where certain items are to be stored. At a more precise level, carton and product labels are used to mark and identify goods, allowing them to be found again easily if stored incorrectly.
Efficient warehouse labelling
Shelf labels and self-adhesive warehouse labels are employed to fulfill different labelling tasks that may require either letters, number stickers, adhesive letters, floor markings, storage space markings, load markings, label sheets, etc. A combination of letters and number keys, for example, can form the basis for efficient warehouse labelling, because they will guide warehouse workers and forklift drivers to the correct storage location in the shortest possible time. Search times are reduced, access times are shortened and order throughput time is reduced. Number and letter stickers are ideal for marking storage locations, shelves, boxes, containers, equipment and machines. Warehouse stickers and warehouse signs can also be custom-made by a service provider. These are then printed with any desired imprint or order numbers, quantity, barcodes, position arrows, etc.
Cardboard and product labels
All the necessary information must be printed on the packaging of goods and sometimes on the products themselves. A wide variety of information is stored in the barcode on a label (1), including: Article number, expiry date, serial number, ingredients and safety instructions. Price, serial or product number and other information about the product are also often printed on the labels, which is all very important for controlling the flow of goods in logistics. Using scanners, incoming and outgoing goods can be recorded and controlled using a merchandise management system.
There are many different barcode types (1D, 2D) with different codes (Code 128, Code 39, EAN, QR-Code, Datamatrix, etc.). Code 128 is widely used and can be read by all barcode scanners. It is used for shipping labels in particular. Wholesalers and retailers mainly use the EAN code to read the desired article information and prices for customers from the database at scanner checkouts.
Shelf labels must be highly durable. It is advisable to think in depth about where you want to use a particular label, which barcode to opt for and in what quality? Also consider what information is needed and where? In addition, the barcodes must be printed cleanly and legibly. Changing the system later on is likely to involve a considerable amount of effort. Also consider the fact that carefully labelled products will facilitate stocktaking.
RFID or Electronic Shelf Labels
RFID technology (2) is being used more frequently in logistics for incoming and outgoing goods, goods tracking, inventory management and order picking. The RFID system consists of an RFID transponder (with antenna coil, circuits and memory) that has an identification number or an Electronic Product Code (EPC), a reader via which the information can be read, and a transmitter unit for data transmission. Advantages of RFID technology include fast acquisition of data without visual contact (in contrast to barcodes), objects do not need to be aligned, it is possible to capture larger amounts of data and there is the possibility of acquiring several data carriers in a fraction of a second (bulk acquisition).
Given there are many cost-intensive manual processes in traditional order picking, applying RFID offers potential for the interface design of material and information flows. With paperless picking processes such as RFID technology, pick lists can be updated online. Also, there are no handwritten details that have to be transferred to the warehouse management system (WMS). Goods that are not present or not in sufficient quantity can be transferred to follow-up pick lists and picked later. Basically, paperless picking leads to cost savings, simple and complete documentation of all goods and material movements, increased performance, higher efficiency and an improvement in delivery quality and thus higher customer satisfaction.
RFID chips are more expensive than barcode labels. Barcodes are easy and inexpensive to generate on a computer. The data carriers are cheap and readers are available in almost every company, and Barcodes can also be easily scanned on high shelves. RFID tags are used when the application possibilities of the barcode are exhausted or when further optimisation is necessary. RFID transponders are more likely to be chosen for tracing high-value goods.
Electronic shelf labels are based on electronic ink, such as that used in e-book readers. The advantage of E-ink labels is the easy adaptability of the display: if prices change, the ESL can be easily updated. Price management is centrally controlled at the touch of a button, while work processes for staff are made easier. Customers, products and e-commerce can be networked and, importantly, errors in the labelling of goods can be avoided. Further advantages include warning messages, key figures, stock changes at the push of a button, bi-directional communication between label and software. ESLs are much more expensive to buy than paper labels but they can be used for a very long time. The screen display does not need a constant power supply and power is only consumed when the display changes.
Optimisation of labelling
As already mentioned, efficient labelling can be achieved with the right labelling or labels, and by choosing the right barcode. In addition, the quality of the label printing and care for the labelling are crucial. Ultimately, the right label for the appropriate application must be carefully selected.
E-commerce commonly involves a huge range of products and rapid purchasing processes (goods receipt, processing, shipping and delivery), which place high demands on shelf labelling (3). Insufficiently coordinated automation of labelling will lead to wasted space and inefficient warehousing, which can result in financial and business losses. Colour coding, for example, will help create orderly labelling and can be used for labeling and 2D barcodes for high information density. When printing labels for different shelf sides, thermal transfer printing technology and flexographic colour coding can be combined in a single, optimised process.