Plastics recycling is becoming increasingly important, even for industrial containers
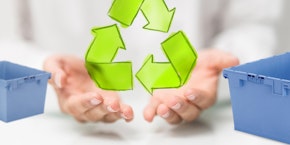
Effective plastics recycling is one of the biggest challenges we urgently need to face. Every day, vast amounts of plastic waste end up in nature, on dumps, in the oceans, and above all, as microplastics in our food chains. Huge carpets of garbage float in the oceans. One example of this is the Great Pacific Garbage Patch, which is now three times the size of France and contains 1.8 trillion plastic parts - 250 for each person on earth. The size and volume of this accumulated trash make it the biggest dump on the planet. Fact that, once again, underlines the importance of establishing well-functioning recycling systems and effective recycling.
Only 16 percent of plastic waste is recycled
In Germany, roughly 16 percent of plastic waste is recycled (1). Worldwide, the number is even less, according to the "Plastic Atlas 2019" (2) published by the German Environmental Protection Agency. According to the study, the "official recycling rates are relatively high - they were 45 percent in 2016 according to the study. However, these figures only refer to deliveries to recycling companies, not to the total quantity actually recycled." In addition, manufacturers tend to use new plastic for their products rather than recycled material, which is often not as pure. The low price of new plastic and the expensive sorting and reconditioning of used plastic in Europe have led to a large proportion of plastic waste being shipped overseas. As a result, Germany is the world's third largest exporter of plastic waste after the USA and Japan. The largest importer of plastic waste, China and Malaysia, have now imposed a ban on imports or significantly limited the quantities purchased. The authors of the study describe the contamination of the planet with plastic as one of the greatest environmental crises. "At current and projected growth rates, the production of plastics by 2050 will cause emissions of 52.5 gigatons of carbon dioxide. Plastics alone could thus consume between ten and 13 percent of the total carbon budget that the world's population must meet to limit global warming to 1.5 degrees," write the authors of the Plastic Atlas 2019.
Functioning cycles and new technologies are urgently needed
Therefore, it is urgent that considerably more plastic is recycled and reused for new products. For this to happen, the recycling cycles must work in a real and global way. In addition, new effective processes must be developed, which would allow manufacturers to better apply the use of recycled plastic granulates.
Diversity of recycled plastic raw materials is increasing
Even though the problem of waste export still exists, a much greater variety of raw materials (ground and recycled materials) are offered on the market today than ten years ago. In the past, companies reused material directly from its own grinding of production waste and customer returns. This is referred to as ground material.
Regenerated plastics are recycled plastics which are first ground and then melted down. Alternatively, the material is sorted, melted down, added and re-compounded. Compounding is the addition of aggregates (fillers, additives, etc.) to achieve desired property profiles. Depending on the origin, a distinction is made between post-consumer and post-industrial raw materials. The post-consumer raw material usually comes from the "yellow bin" (Dual System Germany) which has to be elaborately processed due to the large number of different plastics and states. This includes sorting, grinding, cleaning and de-aromatising. Tremendous improvement during this process is made to the recycled material. The result is post-industrial raw material that is usually relatively homogeneous, so its properties are well defined.
New processes for plastics recycling
There are companies that have perfected the complicated plastic recycling process of synthetic polymers including polyethylene (PE) and polypropylene (PP), as well as the compounding of post-consumer recyclables, so that plastic recyclates in compliance with market requirements can be offered. Thus, the production of plastic does not have to be based on crude oil. With precise sorting, optimized separation, degassing, and filtration, a particularly high purity of the plastic granulates can be achieved during recycling. Special recipes and processes allow them to be manufactured as required in terms of flowability, stability, UV and heat resistance or colouring. Users or manufacturers of plastic products can also apply for the "Blue Angel" environmental seal in order to stand out positively from the competition. Considerable amounts of greenhouse gases are saved in the production of the recyclates and, in addition, upcycling is carried out through their use as a durable plastic product. In this way, cheap disposable articles are turned into high-quality articles which, due to their durability, replace many disposable products.
As a complement to mechanical recycling, research into chemical recycling is being conducted. This offers an alternative solution, making the recycling of plastics possible where recycling solutions or capacities are lacking. During chemical recycling, plastic waste is converted into raw materials or monomers, for example, by thermochemical processes, hydrolysis or solvolysis. The resulting starting material can be used in the production of new plastics. Examples are contaminated plastics, multilayer food packaging, or composite plastics for the automotive and construction industries. The production method uses thermochemical processes to convert plastic waste into raw materials (pyrolysis oil), which can then be used to produce high-quality plastics, like in packaging, for example.
Upcycling with BITO boxes
In situations of reusable use, it is essential to ensure that the recycling cycle really works properly, as is the case with BITO reusable containers. The BITO boxes are made of environmentally friendly recyclable plastic (PP granulate). Additionally, they do not produce any unnecessary waste at the end of their product life, but instead are ground, and the ground material is used to produce new articles. [A closed raw material cycle exists for the containers.] There are possibilities to create reusable and deposit systems with matching plastic containers made of high-quality recycled material.
BITO reusable boxes are extremely durable. The customer receives a five-year warranty on each box. Statistically, the MB reusable container manages over 300 cycles. This means that 300 disposable packages per container are saved. BITO also uses, on request, processed recycling plastics from the Dual System Germany or other recycling systems worldwide. This helps to increase the proportion of plastic waste that is recycled as raw material. BITO containers are a result of a particularly environmentally friendly way of upcycling.
Literature:
1 Only a fraction of plastic waste is reused, Zeit Online, 6.6.2019, to the article
2 Plastic Atlas 2019, Facts and figures about the world of syntetic polymers, Federation for Environment and Nature Conservation Germany (Bund) and Heinrich Böll Foundation, Berlin, 2019, Download
3 ChemCycling: Henkel and Alpla present a special Perwoll bottle, Packaging Journal, October 21, 2019, to the article