Why should you minimize inventory levels?
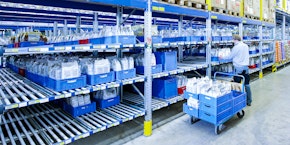
Many companies maintain excessive stocks of individual items. These include, for example, goods that have not been sold or not sold sufficiently, products sold seasonally only, and articles that have too much safety stock. Many companies are afraid of not being able to deliver. However, this results in too much capital being tied up in the warehouse, storage costs being too high and the company's liquidity declining.
Inventory management pays off
Inventory management is very closely related to assortment and portfolio management. In each assortment there are "hit" and "runner" or, measured by the turnover frequency, fast, slow and middle turners. In addition, the individual products in the portfolio go through phases in the product life cycle. They change from „Question Marks“ to „Stars“ and then to „Cash Cows“ and „Poor Dogs“. It is extremely important to know where the individual item is in its product cycle. Every company is also interested in having as many racers as possible, a healthy number of middle turners but virtually no bums in their assortment or stock. In order to increase liquidity and reduce storage costs, it is therefore worth carrying out an ABC (turnover) and XYZ (turnover frequency or uniformity) analysis and consistently clean up the assortment or warehouse.
What defines an optimal inventory level?
Inventory optimisation is a method of balancing the constraints or objectives of capital investment with the objectives of service level across a broad range of SKUs (stock keeping unit), taking into account demand and supply fluctuations. The basic objectives of inventory management are to minimize inventory costs and the associated reduction in capital tie-up, as well as to supply departments and customers with the required materials in a targeted manner while avoiding shortage costs in the course of production downtimes or delays and ensuring delivery on time (1). An optimal stock level must therefore meet all these requirements.
Optimize stocks sensibly
Particularly in small and medium sized companies, the workforce and management are often not aware of the exact stock levels. Inventories (raw materials, materials, finished goods) accumulate, which tie up capital unnecessarily and cost money. With streamlining measures, the space and rental costs for storage space can be saved. In addition to these, superfluous operating, maintenance and personnel costs are incurred. A lean warehouse leads to an increase in liquidity. The capital released can be used to repay loans or make investments.
- You should first perform an inventory count of the warehouse items or use the data from the last inventory, if it was not taken long ago.
- Then rate the purchased parts, finished and semi-finished goods by price (purchase price/cost price). To assess your inventory levels, use warehouse metrics such as average inventory level, inventory value, average storage duration, inventory turnover rate and warehouse interest rate. You will find the definitions of the key figures in every good textbook or online.
- Free your stock from „shopkeepers“ (by recycling, supplier credit, special depreciation and scrapping)
- Optimize the remaining stocks. For materials and goods with a high stock value, optimization is most worthwhile, since even slightly higher stocks lead to a rapid increase in capital commitment. An optimal stock level is achieved with the ABC-XYZ analysis (segmentation of stock levels), by adjusting the ordering behaviour (optimal order quantity and time) and by maximum quantities for valuable parts. The optimum stock level is the economic stock level, which leads to minimum relevant total costs (consisting of storage costs plus procurement costs) for a given degree of readiness for delivery.
- For parts with a high inventory value, you should implement an optimal delivery that meets your requirements (delivery close to use).
- For procurement parts, you should continuously look out for improved or optimal conditions with suppliers.
- Keep a constant eye on your inventories and liquidity - preferably with suitable liquidity planning software and an ERP system.
Do you need a warehouse at all?
Of course, this depends on the individual business model and the willingness to become dependent on other companies. However, there are possibilities to maintain no or hardly any existence of an own warehouse. This includes just-in-time delivery, dropshipping solutions and manufacturing principles such as "Make to Order (MTO)". With just-in-time delivery, the material or semi-finished product for production is delivered exactly when required (see also Toyota Production System, TPS). However, retailers such as computer retailers are also increasingly ordering on a just-in-time basis. Hardly anyone is still burdened with large, expensive warehouses. Even distributors usually only have a few good products in small quantities in stock. When dropshipping products, you can completely dispense with warehousing, as individual suppliers or manufacturers take over the delivery and possibly also the production of the goods. With MTO, the sales order is the trigger for production. Frequently used materials and components are stored, but further processing into higher-value goods only takes place after a customer has placed an order. As a rule, MTO is organized as single-part or small series production. Inventories are relatively low, which means that the fulfilment of customer requirements is often associated with longer delivery times. From the assortment only „racers“ or fast-moving items are stocked in the warehouse. All other articles are manufactured only with available pre-planning or sales order. For security reasons, inventory risk management must be introduced.
If you would like to learn more about minimizing stock levels, storage strategies and storage technology, the BITO guide will provide you with valuable knowledge on all important topics in the field of intralogistics. Please also contact our warehouse technology experts via contact form, email or phone.