Så undviker du vanliga plockfel och ökar lönsamheten
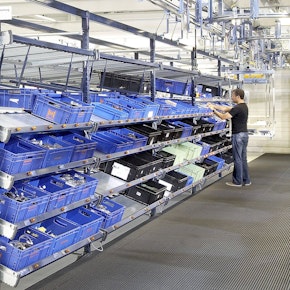
Lagerlogistikens hjärta
De flesta företag som säljer varor har en logistikavdelning. Den centrala funktionen här är plockningen, som i sin tur har stor betydelse för företagets ekonomiska framgång. Ungefär hälften av alla lagringskostnader uppstår i orderplockningsområdet. Desto viktigare att inte orsaka onödiga, extra kostnader på grund av plockfel som kan undvikas. Ändå har en vetenskaplig studie vid tekniska universitetet i München visat att felfrekvensen vid orderplockning ligger runt 0,3 procent. Det här kan få allvarliga konsekvenser, som visar sig på många olika sätt.
Generellt sett gäller att ju senare ett plockfel upptäcks, desto allvarligare och kostsammare blir effekterna av det. Om felet upptäcks under plockprocessen har det ingen relevans för kunden, men orsakar ändå ytterligare tidsåtgång och kostnader för felsökning och korrigering. Om felet inte upptäcks förrän hos kunden blir resultatet kostnadsintensiva efterleveranser eller till och med kundförluster – onödiga konsekvenser som kan undvikas.
Koncentration och kontroll som säkerhet
Trots att en mängd olika former av automatiserad orderplockning är möjliga redan idag, tillämpar majoriteten av företagen en mix av helautomatisk och manuell orderplockning. Plockare till gods-principen är fortfarande den vanligaste metoden. Den erbjuder stor flexibilitet eftersom människans kognitiva förmåga är användbar i olikartade eller ständigt föränderliga system. En människa kan hitta varor placerade i statiska hyllor och plocka ihop dem med hjälp av en lista. Samtidigt är just det här orsaken till många vanliga plockfel.
Det första felet som bör nämnas är kvantitetsfelet. Under tidspress eller på grund av bristande uppmärksamhet kan det hända att en medarbetare plockar fel antal artiklar, så att kunden får fler eller färre varor än begärt. Det här kostar pengar och om en ny leverans måste ordnas går det åt mer tid. Dessutom hänger det ihop med utelämningsfelet. Om orderplockaren inte har hanterat sin plocklista korrekt, eller har godkänt ett steg i processen innan han/hon har genomfört det, finns risken att en artikel inte bearbetas och därmed inte levereras till kunden. Det här är ett plockfel som du kan undvika genom djupgående kontroller och koncentrerat arbete. Samma sak gäller för typfelet, det vill säga att en felaktig artikel levereras som ersättning för eller utöver en befintlig, korrekt artikel.
Korta avstånd och tydliga strukturer motverkar plockfel
Lagerlokalens utformning kan också ha en negativ inverkan på plockningen. Ett misstag som du till varje pris bör undvika är alltför stora och samtidigt oordnade och dåligt strukturerade lagernivåer. Då utvecklas lagerhyllorna snabbt till en oöverblickbar massa av överfyllda behållare med staplade varor. Att hitta bland hyllorna och plocka samman rätt artiklar i rätt kvantiteter blir onödigt tidskrävande för medarbetarna.
Det här hänger samman med ett annat fel vid orderplockning: alltför stora lagringsutrymmen. Med stora avstånd mellan hyllorna går mycket tid förlorad, vilket i sin tur försätter medarbetarna i tidspress och resulterar i misstag. Därför bör du antingen minimera lagringsutrymmet med hjälp av logistikstrategier för leverans och bortskaffande, eller investera i en effektiv lagerstruktur. I detta fall kan en optimering eller redesign av lagret också hjälpa, vilket är i linje med en mer effektiv lagerprestanda. Tydliga strukturer och korta avstånd är nyckeln till framgångsrik orderplockning.
Framgångsrik orderplockning börjar med organisationen
Stora lagerytor leder till stora lagernivåer, som i sin tur bidrar till att produkterna kan orsaka skador på varandra. Det här har också en negativ effekt på plockningen. Minska därför dina lagernivåer och investera tillräckligt med tid i ordentligt organiserade strukturer.
Ett annat misstag som du bör undvika i samband med plockning är att enbart ta hänsyn till logistikavdelningens befintliga status. Regelbundna granskningar av effektiviteten och möjligheterna till rationalisering är ett måste. Din logistikavdelning kan bara fungera effektivt om hela logistikkedjan inkluderas. Här finns den största potentialen för varaktig ekonomisk framgång och minimerad felfrekvens i orderplockningen.
Ignorera inte den mänskliga faktorn
Ja, människor gör misstag. Det ligger i vår natur och kan inte undvikas till 100 procent. Slarv, tidspress eller felaktig hantering av plocksystemen kan leda till fel och få en betydande negativ inverkan på plockningen. Att bortse från den mänskliga faktorn är därför ett av de största misstag som görs av lager- och anläggningschefer. Därför bör du förlita dig på tydliga arbetsinstruktioner, transparenta och enkla processer med få steg. Det här underlättar dina medarbetares dagliga arbete och stärker deras motivation, vilket i sin tur bidrar till en god arbetsmiljö och minimerar stressrelaterade orsaker till fel.
Det här är en av orsakerna till att långa avstånd bör nämnas separat som ett av de misstag du bör undvika vid plockning. Om en medarbetare måste förflytta sig alltför långa sträckor för att samla varorna, i synnerhet mellan enskilda plock, försämras medarbetarens koncentration och motivation, vilket i slutänden resulterar i en felaktig produktsammanställning. I en studie utförd av Fraunhofer Institute for Material Flow and Logistics i Dortmund har man till exempel konstaterat att cirka 93 procent av alla plockfel uppstår till följd av bristande uppmärksamhet.
Slutligen bör du vara noga med att inte bortse från så kallad dödtid. Det vill säga den oundvikliga, icke-produktiva tid som uppstår under plockning på grund av för- och efterbearbetningsåtgärder. Det kan till exempel vara sökning eller identifiering av lagringsplatsen för en artikel. Även här bör du förlita dig på en djupgående organisation, där du tar hänsyn till de fel som redan nämnts och som bör undvikas, för att minimera den icke-produktiva tiden så mycket som möjligt. På så sätt får du en heltäckande lösning som lyfter orderplockningen och därmed hela ditt företag till en ny, framgångsrik nivå.