Metoda kanban w logistyce produkcji
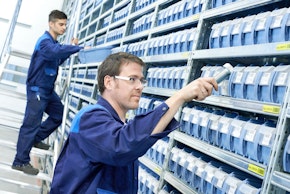
Każdy, kto interesuje się logistyką, techniką magazynową, przemysłem samochodowym lub zarządzaniem z pewnością słyszał o metodzie kanban. Na czym polega ta metoda? Kiedy można ją zastosować? Jakie przynosi korzyści? Jeśli ktoś nie jest pewien, czy ta metoda okaże się w jego zakładzie przydatna powinien zapoznać się z poniższym artykułem.
Zdecentralizowany proces sterowania produkcją w systemie kanban
Kanban jest metodą zdecentralizowanego sterowania produkcją, poszczególne procesy produkcyjne i logistyczne są wywoływane przy pomocy kart (jap. kanban). Metoda ta została wprowadzona w latach 50. w zakładach Toyoty przez menedżera Taiichi Ohno. Wywodzi się ona z przemysłu spożywczego, dokładnie mówiąc z organizacji pracy w supermarketach. Korzyści z zastosowania tej metody to zdecentralizowane sterowanie procesem produkcji, minimalizacja stanów magazynowych (Lean Lager – „odchudzony magazyn”) i dostawa niezbędnych części dokładnie na czas (Just-In-Time JIT). Na kartach umieszczone są takie dane jak numer artykułu, ilość, miejsce składowania etc. Dane stanowisko produkcyjne wysyła do poprzedzającego stanowiska sygnał, że potrzebne są nowe części - do magazynu wysyłany jest np. pusty pojemnik z kartą zamówienia określonej części i odbierany jest pełny pojemnik. Magazyn części otrzymuje tym samym informację, że taka liczba części musi zostać dodatkowo zamówiona i wysyła to zamówienie do dostawcy. Dostawca realizuje zamówienie i dostarcza te części do magazynu. Karta kanban służy zatem jako karta zamówienia ze stanowiska produkcyjnego - uruchamia określone zlecenie produkcyjne względnie impuls, który przekazywany jest kolejno z produkcji aż do dostawcy. W drugim wariancie karta kanban jest kartą identyfikacyjną wytwarzanej lub zamawianej części. Dwa kolejne stanowiska (etapy) produkcyjne tworzą zamknięty system w wewnętrzną regulacją, w ten sposób zapewniona jest pełna koordynacja pomiędzy kolejnymi stanowiskami produkcyjnymi. Przykład: stanowisko produkcyjne A pobiera z „odchudzonego” magazynu (magazyn buforowy) jakiś element, a stanowisko produkcyjne B od razu uzupełnia ten brak.
Zasada "Push" i „Pull”
Zasadniczą korzyścią po wprowadzeniu tej metody jest zdecentralizowane sterowanie procesem produkcji i mechanizm samosterowania połączony z zasadą "Pull". W porównaniu z klasyczną metodą opartą na zasadzie "Push" można znacznie zmniejszyć stany magazynowe. System kanban jest skuteczniejszy, a przy tym bardziej elastyczny niż metoda klasyczna. W metodzie klasycznej z centralnym sterowaniem produkcja opiera się na ocenie zapotrzebowania na dany produkt. W tym celu gromadzi się dane o stanie rynku i poziomie sprzedaży i na tej podstawie sporządza się prognozy. W magazynie przechowuje się wiele części, złożone zamówienia przekazuje się do realizacji w zależności od aktualnego stanu magazynowego. W systemie opartym na zasadzie "Push" istnieje niebezpieczeństwo błędnej kalkulacji. Z jednej strony może to skutkować nadmiarem zgromadzonego towaru - a z drugiej jego niedoborem i niezrealizowaniem złożonych zamówień.
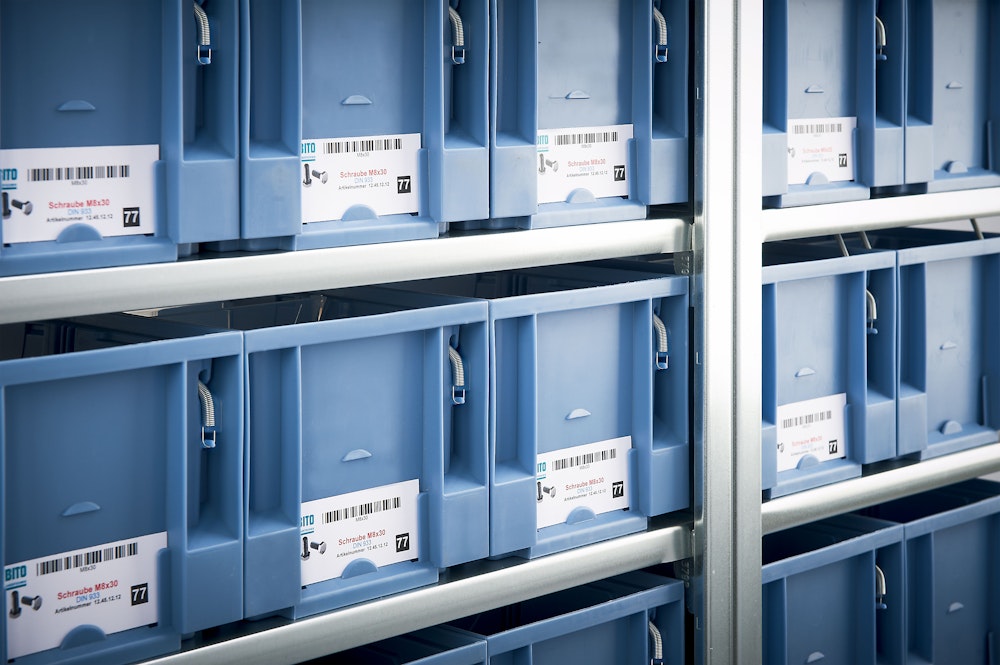
Zarządzanie w systemie kanban
W tym systemie nikt nie musi znać wszystkich elementów składających się na łańcuch procesów. Na danym stanowisku napełnia się pusty pojemnik - i to wszystko. System sam się organizuje i sam się reguluje, opiera się na lokalnych danych i na prostych zasadach. Można go porównać do naturalnych mechanizmów samoregulacji opartych na inteligencji zbiorowej - podaje się tu na przykład funkcjonowanie mrówek w mrowisku. W tym systemie zmienia się rola kierownictwa zakładu. Osoby zarządzające zakładem muszą najpierw opracować ogólne (ramowe) warunki, które umożliwią funkcjonowanie łańcucha procesów. Koncepcja zewnętrznego impulsu, który dociera do każdego stanowiska produkcyjnego także opiera się na inteligencji zbiorowej (na wiedzy wielu osób). Osoba zarządzająca zakładem przejmuje rolę kierownika zespołu, jej zadaniem jest tworzenie warunków do jego samoorganizacji. Poza tym pełni on rolę moderatora, motywatora, doradcy, koordynatora i mediatora (rozjemcy) - w ten sposób przyczynia się do harmonizacji procesu produkcji.
Kiedy warto wprowadzić metodę kanban?
System kanban nie zawsze się sprawdza. Jeśli w danym przedsiębiorstwie wytwarza się tylko pojedyncze produkty lub krótkie serie metoda ta nie ma zastosowania. Metoda ta sprawdza się tam, gdzie produkuje się duże serie mało zróżnicowanych części/elementów. Sterowanie produkcją, przepływ materiałów, logistyka i uzupełnianie zapasów oparte są wyłącznie na rzeczywistym zużyciu materiałów w miejscu udostępnienia/zużycia. Jak już wspomniano prowadzi to do dużej elastyczności i znacznego zmniejszenia poziomu zapasów. Może to jednak prowadzić do przerwania łańcucha dostaw - stanie się tak, gdy wypadnie z niego choćby jeden element. Przed wprowadzeniem systemu kanban trzeba wypełnić kilka warunków:
- produkcja ciągła,
- wysoki stopień standaryzacji produktu wytwarzanego metodą cykliczną,
- jednoznaczne oznaczenia zapewniające prawidłowe przydzielenie kart i pojemników, ścisłe zarządzanie pojemnikami, sprawny system kontroli jakości,
- należy unikać dużych wahań poziomu produkcji,
- należy skrócić i uprościć drogi transportu.
Pojemniki i regały w systemie kanban
Specjalne systemy regałów i pojemników dla systemów kanban w intralogistyce są dzisiaj standardem. Należą do nich pojemniki do składowania części C - które łączą w sobie zalety pojemników regałowych i pojemników warsztatowych SK - albo pojemniki Euro EMB. Pojemniki do składowania części C pozwalają na optymalne wykorzystanie miejsca na regałach. Części można pobrać od przodu (po przesunięciu szybki w dół) i z góry (po częściowym wysunięciu pojemnika, który utrzymywany jest na regale przez specjalny element blokujący). Szybka dozująca umożliwia pobieranie części od dołu do góry. Przezroczysta szybka przednia umożliwia bieżącą kontrolę stanu magazynowego. W systemie kanban z jednym pojemnikiem zasada jest realizowana w jednym pojemniku - po pobraniu od przodu ostatniej części można podnieść szybkę dozującą i zacząć pobierać części z kolejnej partii. Proces zamawiania nowych części C jest uruchamiany przez odebranie karty lub znacznika RFID umieszczonego na tylnej stronie pojemnika. W systemie kanban z dwoma pojemnikami pierwszy pojemnik jest po opróżnieniu wyjmowany z regału, karta jest odbierana, co uruchamia proces zamawiania - a drugi pojemnik jest przesuwany do przodu. Zamówiony pojemnik z kolejną partią części jest wsuwany od tyłu (zasada FIFO). Również pojemnik Euro EMB - który można składować na regałach przepływowych dla towarów drobnicowych - bardzo dobrze nadaje się do metody kanban. Ma długość 600 mm, dostępne są wersje o różnej wysokości i szerokości. Zestaw modularnych pojemników jest tak zaprojektowany, że można je układać i trwale łączyć (sztaplować) na jednej europalecie. Pojemnik jest bardzo stabilny, można go bezpiecznie sztaplować, ma przy tym dużą pojemność. Gładka powierzchnia umożliwia łatwe mycie/czyszczenie pojemnika. Zintegrowane ergonomiczne uchwyty ułatwiają przesuwanie i przenoszenie pojemnika.
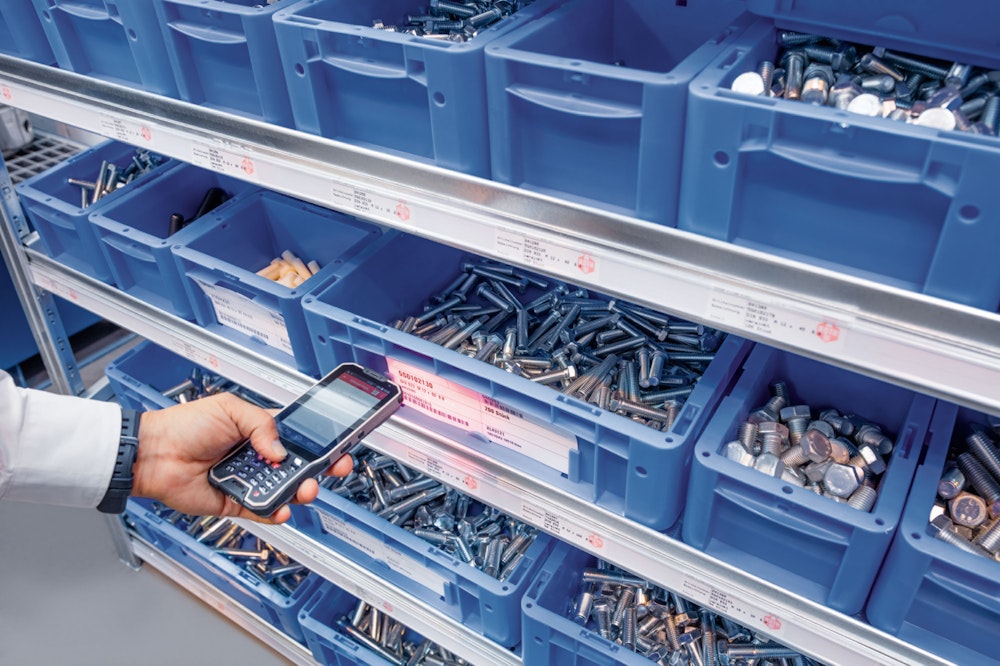
Zamiast kart kanban stosuje się dzisiaj takie nośniki danych jak kody kreskowe lub znaczniki RFID. Dane lub zlecenia są przy tym przekazywane do magazynowego systemu informatycznego, systemu ERP lub odpowiedniego dostawcy przez sieć Wi-Fi. W systemie z kodami kreskowymi kod na pustym pojemniku przeznaczonym na określoną część jest ręcznie skanowany przez pracownika i przekazywany do dostawcy, który dostarcza kolejną partię towaru. W systemie ze znacznikami RFID proces ten jest zautomatyzowany. Dane artykułu oraz pojemnika są przekazywane automatycznie ze stanowiska produkcyjnego u klienta do magazynu głównego drogą radiową z zastosowaniem techniki RFID, ręczne skanowanie nie jest tutaj potrzebne. Znacznik RFID jest wyposażony w antenę i jest przytwierdzony do danego przedmiotu lub pojemnika kanban. Każdy znacznik ma własny numer, który pozwala na jego identyfikację i zapewnia bezpieczeństwo danych. System RFID składa się ponadto z czytnika do identyfikacji transponderów i nadajnika do przekazywania danych lub automatycznego zamawiania kolejnych części potrzebnych na danym stanowisku produkcyjnym.