Jak zredukować pokonywane trasy w magazynie – 5 pomysłów na szybkie do wdrożenia działania
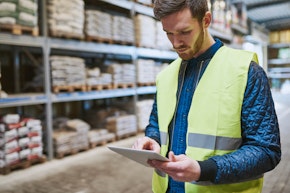
Czynnik kosztowy – logistyka i komisjonowanie
Niezbędne dla dobrze funkcjonującego działu logistyki jest płynny i bezusterkowy przebieg wszystkich procesów roboczych. Zwłaszcza w przypadku procesów zachodzących w magazynie wszystko powinno działać bez zarzutów. Kompletacja zamówień i związane z nią trasy do pokonania mają jako centralne funkcje działu logistyki ogromne znaczenie dla ogólnego sukcesu gospodarczego całego przedsiębiorstwa. Jednakże w większości przypadków to właśnie tu powstaje najwięcej błędów i zakłóceń w przebiegu pracy. Badania naukowe przeprowadzone przez UT w Monachium wykazały, że poziom błędu wynosi tutaj około 0,3 procenta. Jednocześnie około połowy wszystkich kosztów magazynowania przypada na kompletację zamówień. Tym ważniejsze jest więc unikanie niepotrzebnych dodatkowych kosztów spowodowanych błędami. To może mieć poważne konsekwencje.
1. Organizacja i strategia
Nic nie zabiera pracownikom magazynu więcej czasu niż źle rozmieszczone i posortowane towary. Ci, którzy biegną z jednego miejsca do drugiego bez konkretnego planu i nie mając logicznej strategii pokonywania tras, tracą cenny czas. Należy zatem koniecznie unikać zbyt dużych, a jednocześnie nieuporządkowanych i źle zorganizowanych zapasów. W przeciwnym razie składowane artykuły szybko stają się trudną do ogarnięcia masą przepełnionych pojemników z towarami ułożonymi w stosy. Znalezienie optymalnej trasy jest trudne, a kompletacja wcześniej czy później staje się zwykłą stratą czasu – sporo czasu marnuje się na pokonywanie dużych odległości między regałami. Dlatego też szczególnie ważny jest wcześniejszy wybór odpowiedniej metody składowania, takiej jak zasada Fifo lub Lifo. Zależy to od np. asortymentu lub częstotliwości rotacji. Pomocna może być przy tym analiza metody magazynowania lub kompletacji.
Pomóc w tym może zminimalizowanie powierzchni magazynowej dzięki logistycznej strategii zaopatrywania i usuwania towarów lub zainwestowanie niewielkiej ilości pracy w efektywną organizację magazynu. Dzięki przeprojektowaniu magazynu możliwe jest osiągnięcie przejrzystej organizacji i utworzenie krótkich ścieżek komunikacyjnych, co przyczynia się do lepszej wydajności magazynu i zaprojektowania optymalnych ścieżek. Należy również koniecznie uwzględnić bezproduktywny, ale jednocześnie niemożliwy do uniknięcie dodatkowy czas powstały podczas komisjonowania w związku z czynnościami przygotowawczymi i następczymi. Ten tak zwany "czas martwy" oznacza na przykład wyszukiwanie lub identyfikację miejsca przechowywania artykułu. Postaraj się więc, aby ten nieproduktywny czas był jak najkrótszy dzięki krótkim odległościom do pokonania – to przyniesie korzyści całemu przedsiębiorstwu.
2. Przygotowanie to połowa sukcesu
Utworzyć i wyposażyć magazyn bez planu? Po prostu wysłać na własną rękę pracowników w poszukiwaniu towarów? Zapisywanie ścieżek na górach papieru? To nie jest dobry pomysł. Ponieważ złe i ewentualnie ręczne przygotowanie nigdy nie pomoże wydajności magazynu. W zaprojektowaniu efektywnych i optymalnych tras pomoże praca z oprogramowaniem specjalnie zaprojektowanym do pracy w magazynie. Wesprze ono Państwa w obliczeniu odpowiednich tras dla każdego pracownika i każdego pobrania towaru. Stosując systemy cyfrowe oszczędza się nie tylko papier i wszelkie listy - które poza tym można szybko zgubić - ale także chroni się środowisko naturalne.
Tak więc każdy, kto podczas projektowania optymalnych ścieżek stosuje system zarządzania magazynem, wspiera jednocześnie najlepsze możliwe wykorzystanie swojej personelu i najlepszy możliwy podział czasu pracy. Im bardziej płynnie przebiegają prace logistyczne w magazynie, tym szybsza staje się realizacja zamówień. To z kolei ma pozytywny wpływ na całą firmę. Do tego potrzeba jednakże odpowiednich warunków. Ponieważ zarządzanie przy pomocy oprogramowania jest bezużyteczne, jeśli osoby kompletujące zamówienia muszą mimo to pokonywać długie trasy. Konkretnie oznacza to, że metoda przechowywania musi pasować do tras i odwrotnie.
3. Regularna kontrola tras i procesów
Zaufanie jest dobre, kontrola lepsza – jak mówi przysłowie i ma w tym rację. Ponieważ właśnie dla projektowania i wykorzystywania optymalnych tras decydujące znaczenie ma kontrola wszystkich procesów zachodzących w magazynie. Jak często pracownicy pokonują trasy i dokąd się udają? Ile czasu zajmuje im pokonywanie odległości między kolejnymi pobraniami? Ile błędnych pobrań ma miejsce? I jak często dany artykuł jest pobierany? Pytania takie jak te i dokładne odpowiedzi na nie są niezbędne do zaprojektowania jak najbardziej efektywnych ścieżek w magazynie. Proszę obserwować czas realizacji zlecenia, rejestrować poszczególne pobrania i szczegółowo analizować wszystkie zebrane dane. Pozwala to na szybką identyfikację ścieżek, które nie są optymalne i wymagają optymalizacji.
4. Unikanie bałaganu
Porządek w logistyce jest bardzo ważny. Za duże powierzchnie magazynowe i zapasy towarów nie powinny mieć miejsca w magazynie. Zbyt duże powierzchnie magazynowe prowadzą bowiem do powstawania dużych zapasów, co z kolei sprzyja wzajemnym uszkodzeniom produktów. Ma to negatywny wpływ nie tylko na kompletację zamówień, ale także utrudnia pracę pracowników i oznacza bałagan w zapasach i jednocześnie zastawione i zablokowane ścieżki kompletacji.
Dlatego należy zredukować zapasy i zainwestować odpowiednią ilość czasu w dobrze zorganizowane struktury i swobodny dostęp do ścieżek. Tutaj również kontrola odgrywa pewną rolę: Niezbędne są regularne przeglądy skuteczności i potencjału racjonalizacyjnego. Państwa trasa może być naprawdę efektywna tylko wtedy, gdy wszystkie prace logistyczne i cały łańcuch logistyczny zostaną włączone w proces organizacji kompletacji zamówień. W tym właśnie tkwi największy potencjał trwałego sukcesu ekonomicznego i optymalnego projektowania tras.
5. Szczególne uwzględnienie towarów promocyjnych i nowych części
W projektowania optymalnych ścieżek należy uwzględnić również towary promocyjne i nowe części. Są one narażone na wahania w zakresie pobrań, cieszą się popytem tylko przez krótki czas i szybko opuszczają magazyn. Z tego powodu powinny być one przechowywane w magazynie w sposób strategiczny i logiczny pozwalający na szybkie dotarcie do nich. Dzięki temu możecie Państwo szybko zareagować na potrzeby swoich klientów oraz szybko zrealizować spontaniczne zamówienia.
Organizacja i strategia, dogłębne przygotowanie i regularna kontrola, jak również unikanie nieporządku i oddzielne obchodzenie się z towarami promocyjnymi to pięć ważnych czynników, które należy wziąć pod uwagę podczas projektowania optymalnych tras. Ma to kluczowe znaczenie dla Waszej konkurencyjności. Ponieważ klienci, którzy szybko otrzymują swój towar, są zadowolonymi klientami – a zadowoleni klienci z pewnością pozostaną Waszymi klientami przez długi czas. Aby to osiągnąć, wskazane jest zaangażowanie w planowanie optymalnych tras również pracowników. Zapytajcie swoich pracowników, gdzie można zredukować trasy, które mają pokonać. Zaangażujcie zewnętrznego doradcę i poproście go o ocenę warunków panujących w magazynie. Wspólnie z nim zastanówcie się Państwo, czy w niektórych miejscach można nawet całkowicie zlikwidować trasy. Pomocne mogą się tu okazać systemy FTS (np. system transportu bez kierowcy LEO Locative), które mogą w sposób elastyczny połączyć określone miejsca w magazynie. Może to znacznie zwiększyć wydajność magazynu.
Fotoquelle Titelbild: © Flamingo Images/shutterstock.com