Case ConDoor, Clever ontwerp inrijstellingen en pientere opstelling
Dankzij de visgraatopstelling en de driehoekige consoles waarop de liggers rusten, profiteert ConDoor maximaal van de beschikbare ruimte.

De klant
Sinds mei 2021 maakt ConDoor Door Components zelf de veren van overheaddeuren. Daarvoor is in Emmen een verenafdeling opgezet met een uitgekiend logistiek proces. Daarin is een sleutelrol weggelegd voor de inrijstellingen van BITO. Dankzij de visgraatopstelling en de driehoekige consoles waarop de liggers rusten, profiteert ConDoor maximaal van de beschikbare ruimte en de hefhoogte van de AGV’s.
Montagetijd op locatie tot een minimum teruggebracht
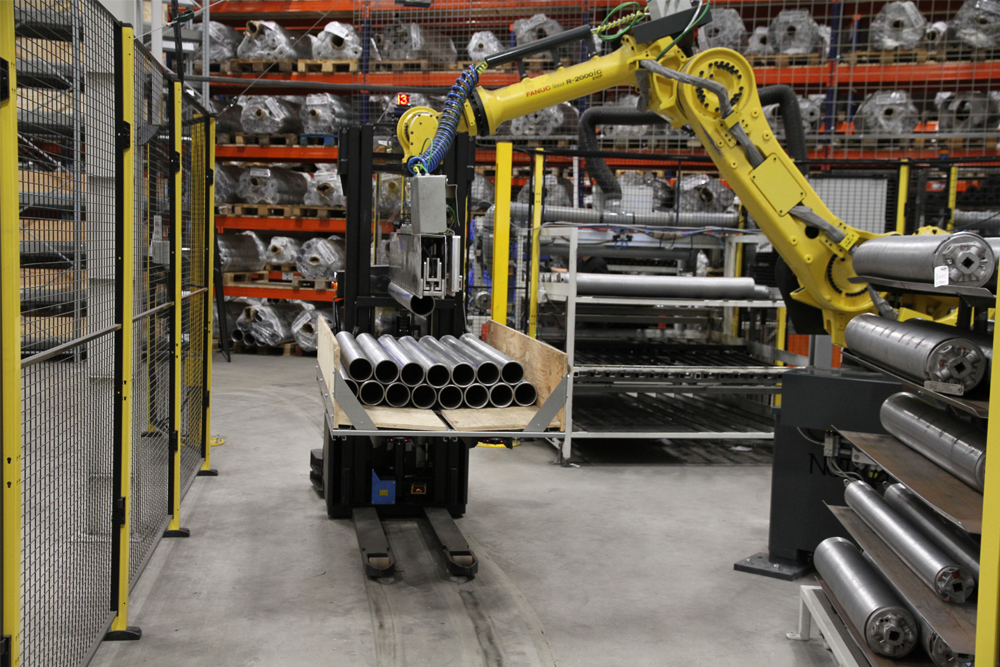
ConDoor produceert overheaddeuren en levert die via dealers aan zowel bedrijven als consumenten. Sinds de oprichting 25 jaar geleden is het bedrijf uitgegroeid tot een wereldwijde speler met twee productievestigingen in Nederland. De deuren zelf ontwerpt en maakt ConDoor op de hoofdvestiging in Zeewolde, terwijl alle andere componenten zoals profielen, veren en assen uit Emmen komen. “Wat ons onderscheidt, is dat we een groot deel van het productieproces zelf uitvoeren en daardoor optimaal onder controle hebben. Voor onze dealers fungeren wij als een one-stop-shop”, vertelt projectleider Johan Oosting van ConDoor Door Components in Emmen.
Sinds het voorjaar van 2021 beschikt ConDoor ook over een eigen productieproces voor veren. In Emmen zijn twee werkstations geplaatst waar de veren zodanig worden geprepareerd, dat de montagetijd op locatie tot een minimum is teruggebracht. “Vaak moeten de veren worden ingekort of opgevuld met een veervulling om slijtage van de as binnenin de veer tegen te gaan. En soms hebben we duplexveren nodig waarbij twee standaard veren in elkaar worden gedraaid”, vertelt Oosting.
Werkvoorraad
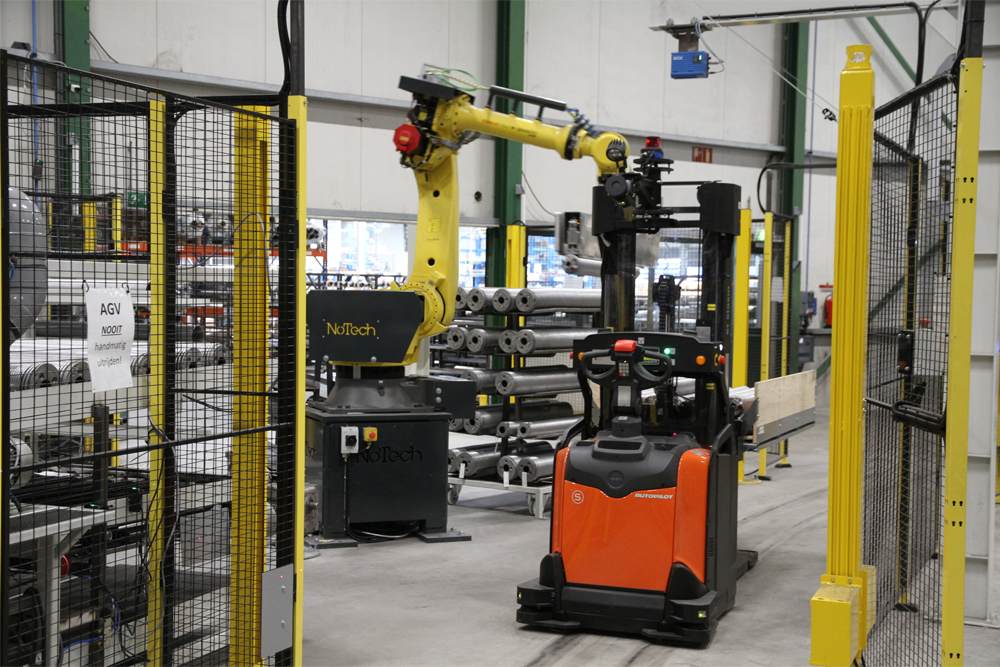
De aanvoer van veren is volledig geautomatiseerd met behulp van drie automatisch geleide voertuigen (AGV’s) en één knikarmrobot. “De zwaarste veren zijn handmatig niet te tillen”, verklaart Oosting. “Daarom hebben we gekozen voor automatisering. De AGV’s brengen de veren naar de robot, die beschikt over een speciaal ontwikkelde magneetgrijper. De robot pakt de veren een voor een op en plaatst die in de werkstations.”
De bulkvoorraad ligt op pallets
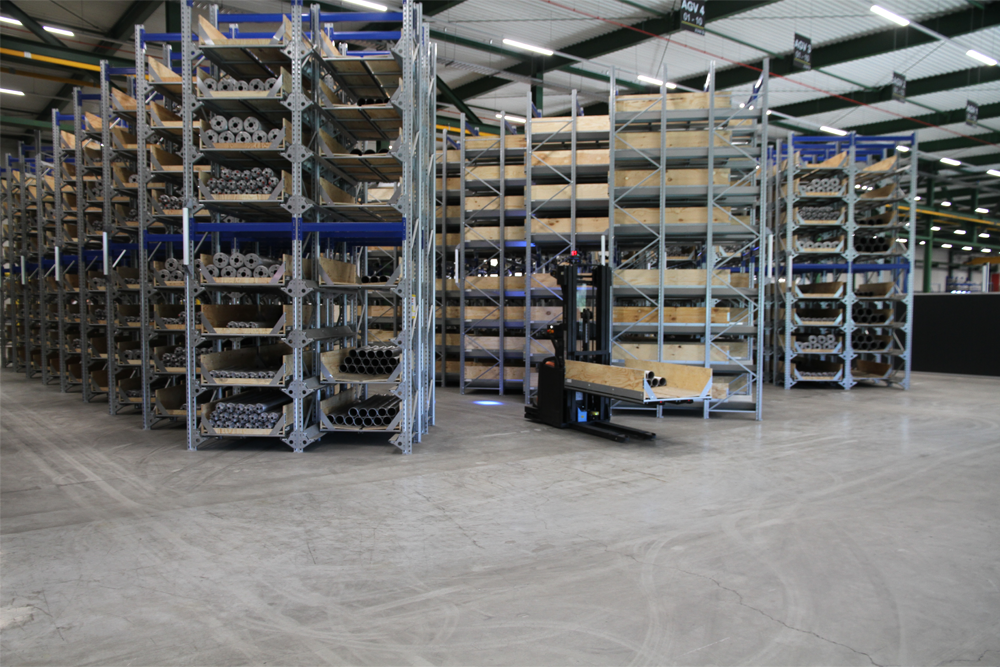
De standaard veren komen van overzee en liggen in Emmen op voorraad. De bulkvoorraad ligt op pallets die met een reachtruck in standaard palletstellingen worden geplaatst. Vanuit de bulkvoorraad wordt wekelijks de werkvoorraad aangevuld. Die bestaat uit houten bakken. Omdat die bakken lang zijn, is gekozen voor een opslagsysteem met inrijstellingen. De AGV’s plaatsen de bakken op de liggers, die door de driehoekige vorm ervoor zorgen dat de lading automatisch wordt gecentreerd.
Opslaghoogte
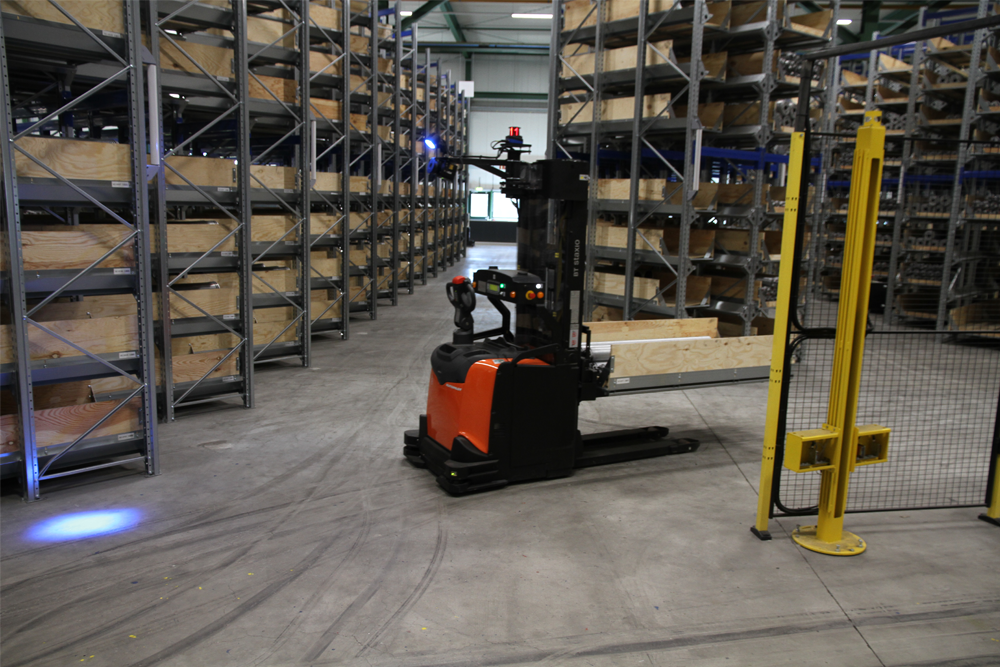
Een kritieke factor in het ontwerp van het opslagsysteem is de opslaghoogte van de inrijstellingen. Vanwege de beperkte ruimte in Emmen wil Condoor de bakken graag acht hoog opslaan. “De hoogte-indeling luisterde zeer nauw”, legt Oosting uit. “Als we het achtste opslagniveau iets te hoog hadden gemaakt, zouden die opslaglocaties buiten het bereik van de AGV’s liggen. Dan hadden we natuurlijk kunnen overstappen op grotere AGV’s, maar die hebben meer manoeuvreerruimte nodig waardoor we per saldo nog minder bakken kwijt konden.”
Het punt is dat de inrijstellingen van de meeste magazijninrichters zijn uitgerust met liggers die rusten op rechthoekige draagbalken. Door de vorm van deze consoles zouden de opslaglocaties niet de vereiste zeven centimeter vrije hoogte hebben om de bakken veilig te kunnen in- en uitslaan. “We hebben zeven magazijninrichters gevraagd om een oplossing. Vijf daarvan moesten meteen afhaken. BITO was slechts één van de twee partijen die aangaf ons te kunnen helpen”, weet Oosting.
Driehoekige consoles
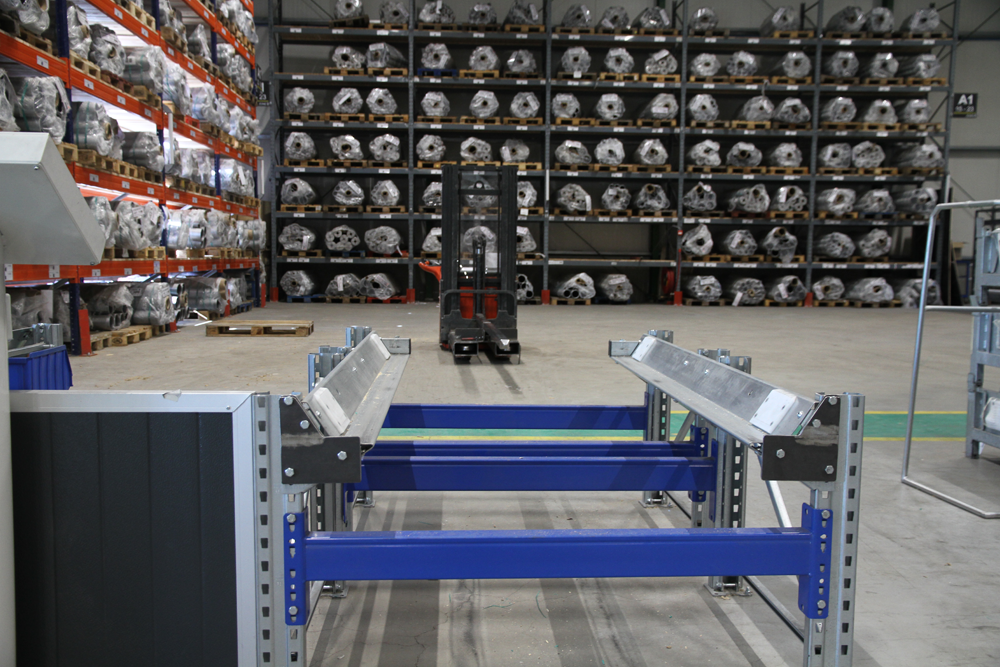
Anders dan de meeste inrijstellingen beschikken die van BITO over consoles met een driehoekige vorm. Die schuine hoeken bezorgen ConDoor net die paar centimeter extra speling die nodig is om de bakken acht hoog inclusief de zeven centimeter vrije hoogte te kunnen opslaan. “Het gebruik van driehoekige in plaats van rechthoekige consoles scheelt minimaal één en misschien zelfs wel twee opslagniveaus. Dankzij de oplossing van BITO kunnen we optimaal gebruik maken van het vloeroppervlak en de hefhoogte van de AGV’s.”
Opslagdichtheid is nog verder vergroot
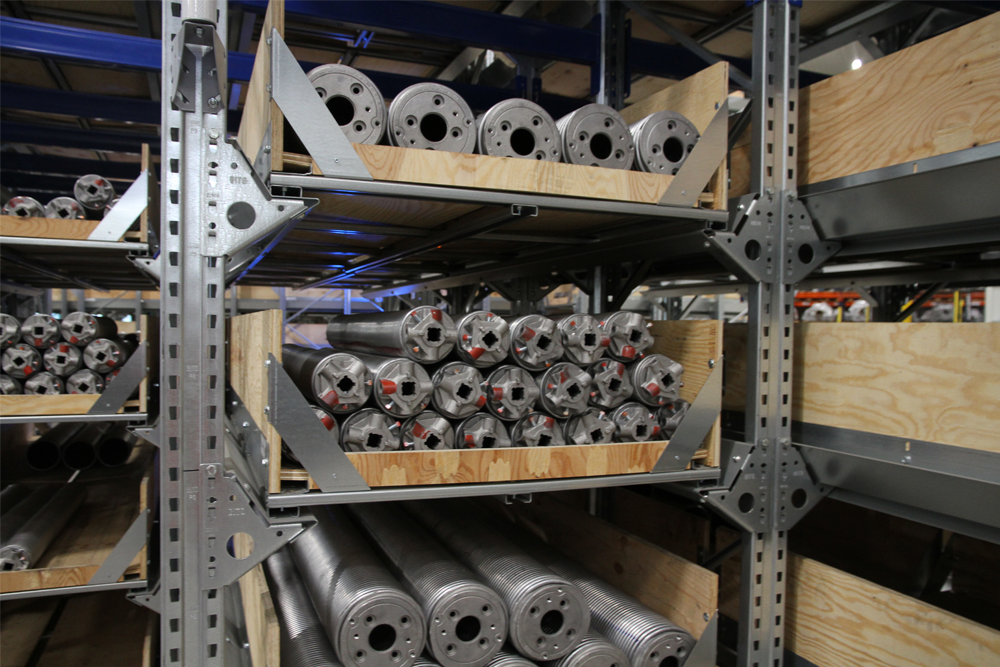
De opslagdichtheid is nog verder vergroot door de inrijstellingen in visgraatopstelling te plaatsen. “Dat heeft te maken met de draaicirkel van de AGV’s en de lengte van de bakken. Als we de inrijstellingen recht tegenover elkaar hadden geplaatst, zouden we erg brede gangpaden nodig hebben gehad. Door ze schuin te plaatsen, hebben de AGV’s relatief minder manoeuvreerruimte nodig en kunnen we meer stellingen kwijt.”
Twee invoerstations
De inrijstellingen van BITO vormen niet alleen de basis van het opslagsysteem, maar ook van de invoerstations. Als de werkvoorraad moet worden aangevuld, plaatst een AGV een lege bak op het invoerstation. Een reachtruck haalt een pallet met veren uit de bulkvoorraad, zodat de lege bak kan worden gevuld. Het zelf ontwikkelde warehouse management systeem stuurt de AGV’s vervolgens naar één van de lege opslaglocaties. “We hebben twee invoerstations, zodat het aanvulproces continu kan doorgaan”, aldus Oosting.
Over de keuze voor BITO hoefde ConDoor niet lang na te denken. BITO had eerder al doorrolstellingen geleverd voor het pick-to-light-gebied waar alle kleine onderdelen worden verzameld en verpakt. De samenwerking verliep prima, ondanks de coronapandemie. “Daardoor hebben we uitsluitend via videocall, telefoon en email gecommuniceerd. De stellingen hebben we zelf gemonteerd op basis van instructies van BITO. Ik heb de mensen van BITO pas persoonlijk ontmoet toen de hele operatie al draaide.”
Zuinig op personeel
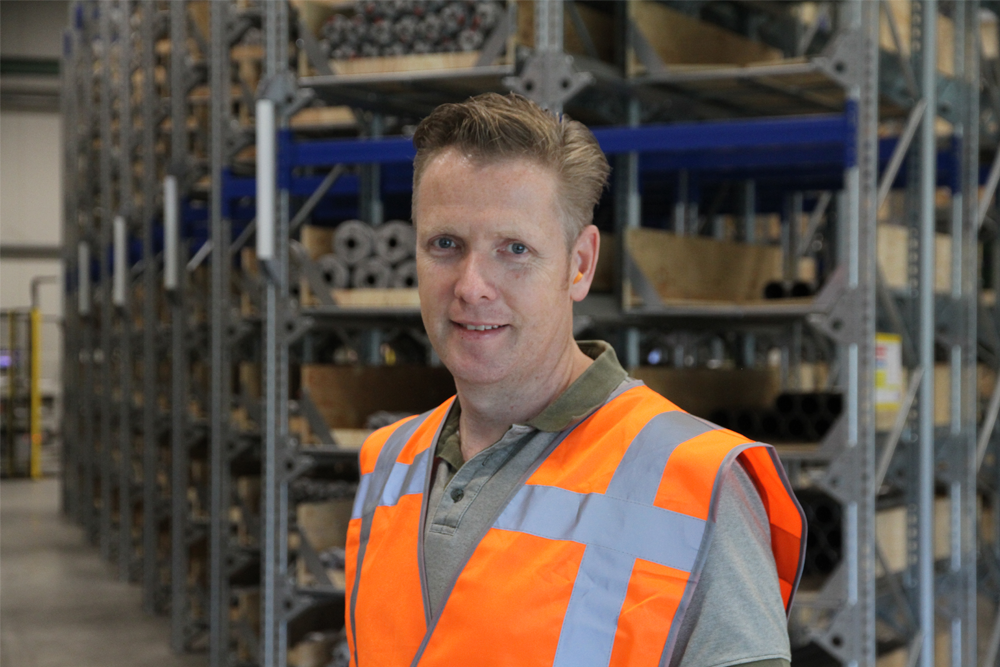
De verenafdeling draait op dit moment uitstekend. ConDoor is gestart met twee AGV’s, maar heeft na een jaar besloten een derde aan te schaffen. Die bieden samen meer dan voldoende capaciteit om de twee werkstations te bedienen en de werkvoorraad aan te vullen. Oosting: “De medewerkers zijn eveneens tevreden. Ze hoeven niet zelf te zoeken en te sjouwen met veren en kunnen zich volledig concentreren op het productieproces. Dat was precies de bedoeling, want we moeten vandaag de dag zuinig zijn op ons personeel.”