Che cos'è il picking?
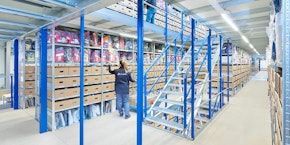
Ogni giorno, i clienti ordinano la merce online o offline che deve essere recuperata dal magazzino e resa pronta per la spedizione da parte dei commissionatori in base all'ordine in questione. In breve, l'allestimento degli ordini è la combinazione di merci secondo gli ordini di un determinato assortimento complessivo. Il processo di picking può essere a livello singolo o a multilivello. L'ordine di prelievo viene trasmesso sotto forma di liste di prelievo o per via elettronica all'addetto al prelievo corrispondente, che può essere un uomo o una macchina.
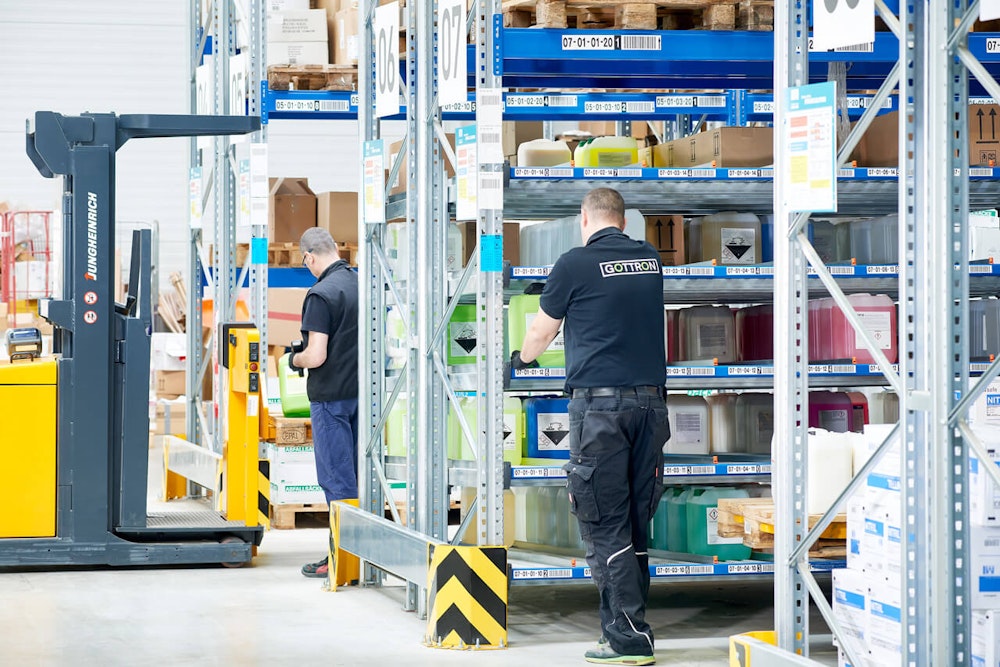
Fasi del processo di prelievo
Secondo la linea guida VDI 3590, il processo di picking consiste nelle seguenti fasi di processo individuali:
- Specifica delle informazioni di trasporto (per merci e/o commissionatori)
- Trasporto della merce al luogo di preparazione
- Fornitura della merce
- Spostamento del raccoglitore verso il luogo della preparazione
- Specifica delle informazioni sulla presa
- Rimozione degli articoli da parte del commissionatore
- Consegna del prelievo
- Conferma dell'operazione o delle operazioni di prelievo
- Trasporto della/e unità di raccolta per la consegna
- Specificazione delle informazioni di trasporto per l'unità o le unità di raccolta parziale
- Trasporto dell'unità di raccolta parziale (o delle unità di raccolta parziali)
Il tipo di merce e il magazzino determinano l'allestimento degli ordini
Il tipo di magazzino o di merce determina il tipo di prelievo. La procedura FIFO (First In First Out) significa che la merce immagazzinata per prima viene prelevata e rimossa dal magazzino per prima. Ciò significa che le merci appena arrivate vengono stoccate nella parte posteriore e quelle da recuperare per prime vengono stoccate nella parte anteriore dello scaffale. La procedura FEFO (First Expired, First Out) viene utilizzata quando un prodotto ha una data di scadenza e deve quindi essere scelto per primo. Se un periodo di stoccaggio più lungo non influisce sulla qualità della merce, come ad esempio prodotti metallici (viti o chiodi) o determinati materiali sfusi (sabbia, carbone o ghiaia), si applica il principio LIFO (Last In First Out).
1. il picking delle merci trasportate all'uomo
Qui la merce viene portata direttamente al commissionatore tramite la tecnologia del trasportatore. L'addetto alla preparazione ordini accetta quindi la merce alla stazione di picking e preleva la quantità specificata dal sistema di gestione del magazzino. I contenitori vuoti o i contenitori pieni di quantità residue vengono poi trasportati al magazzino con lo stesso trasportatore.
Vantaggi
- elevate prestazioni di prelievo grazie ai ridotti tempi di viaggio
- vasta gamma di articoli possibili
- basso tasso di errore
- i contenitori vengono trasportati indietro facilmente e automaticamente
- possibilità di progettazione di un posto di lavoro ergonomico
Svantaggi
- costi di investimento relativamente elevati per i sistemi di scaffalatura e recupero automatizzati
- minore flessibilità grazie al numero fisso di stazioni di prelievo
- Se la macchina si guasta, il buffer può arrestarsi.
- nessuna flessibilità per il commissionatore con esigenze fluttuanti
Esempi
caroselli, scaffalature paternoster, scaffalature a torre, sistema di stoccaggio automatico di picking (AKS), scaffalature di flusso con RFZ automatico, scaffalature a grande altezza con trasportatori a cremagliera automatici (RFZ)
2. il picking da uomo a uomo
L'addetto all'allestimento degli ordini si reca nel luogo di stoccaggio e preleva la merce necessaria in loco. Di solito questo viene fatto senza aiuti automatici. Questo tipo di picking è quindi particolarmente adatto per ordini più piccoli e merci di peso ridotto. Se si utilizza il picking a più stadi (vedi sotto), questo metodo può essere gestito in modo economico anche nei grandi centri di distribuzione.
Vantaggi
- bassi costi di investimento necessari
- elevate prestazioni di prelievo con possibilità di percorsi di prelievo ottimizzati
Svantaggi
- maggiore impegno durante il ritiro della merce
- maggiori distanze a piedi e tempi di percorrenza
- difficile design ergonomico del posto di lavoro
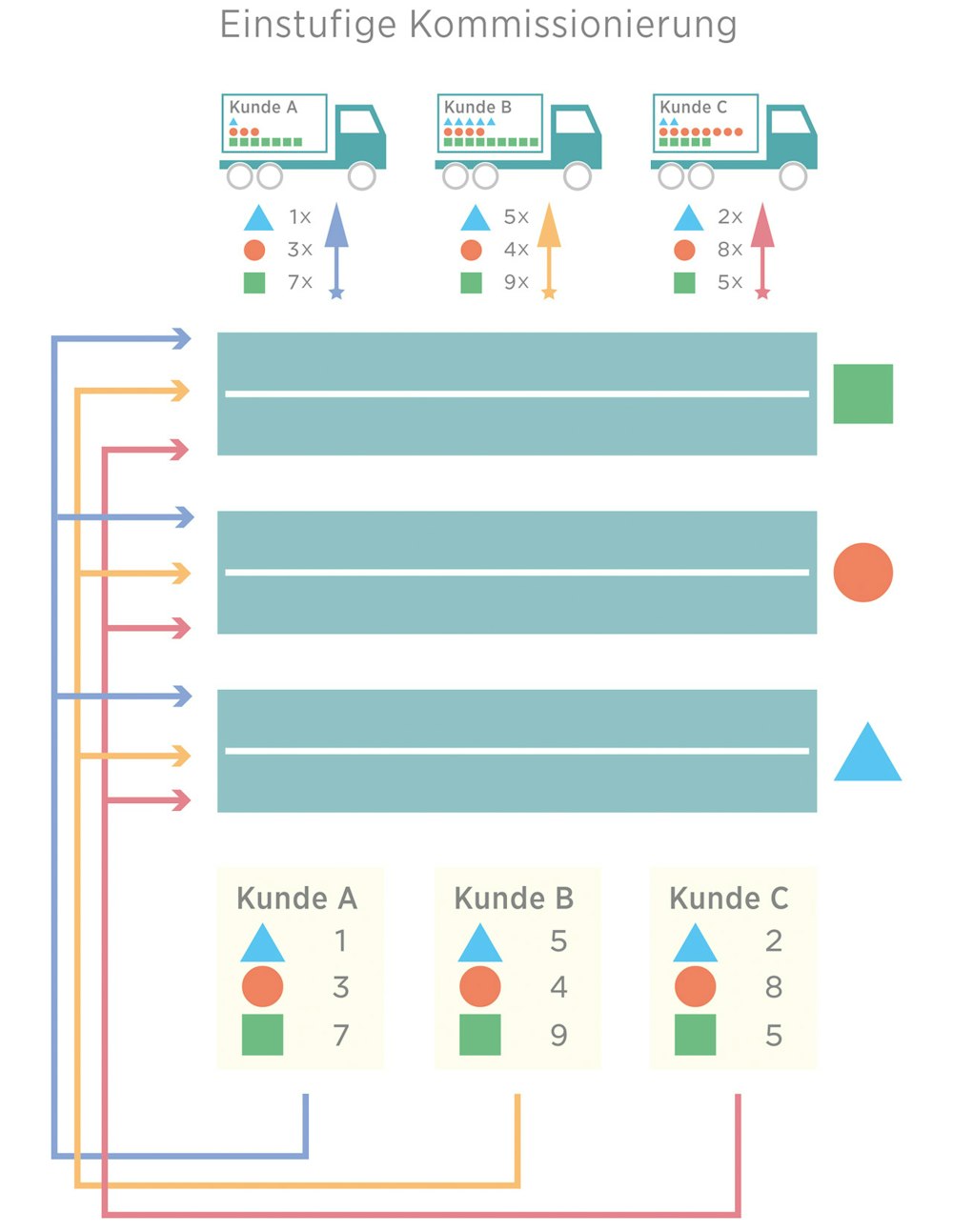
Picking a un solo livello
Con il prelievo in una sola fase, ogni ordine del cliente viene compilato individualmente. Come metodi di prelievo vengono utilizzati il prelievo in serie, in parallelo e in ordine. Con il prelievo in parallelo, un ordine viene suddiviso in diverse zone di prelievo ed elaborato contemporaneamente. Gli ordini (più grandi) vengono suddivisi ed elaborati contemporaneamente in diverse zone di stoccaggio. Non appena tutti gli ordini parziali sono stati completati, vengono nuovamente riuniti (consolidati) in un punto di raccolta per formare il rispettivo ordine completo. Questo porta ad un risparmio di distanze e ad un tempo di elaborazione degli ordini più breve. Tuttavia, è necessaria un'unità di consolidamento per combinare gli ordini dei pezzi. L'intero processo deve essere coordinato e controllato da un sistema di gestione del magazzino.
Nel prelievo in serie, gli articoli dell'ordine vengono elaborati in successione. O un order picker passa attraverso tutte le zone del magazzino oppure un ordine viene trasferito da un order picker di una certa zona al successivo order picker e alla sua zona, come in una corsa a relè, fino al completamento di tutte le posizioni dell'ordine. Le distanze percorse sono relativamente piccole, dato che un picker si muove in piccole zone di prelievo. Poiché l'ordine non viene suddiviso ma trasmesso, non è necessario alcun consolidamento. Lo svantaggio è che gli ordini devono essere temporaneamente conservati nei punti di trasferimento. Questo può anche portare ad una fornitura non equa dei commissionatori con gli ordini.
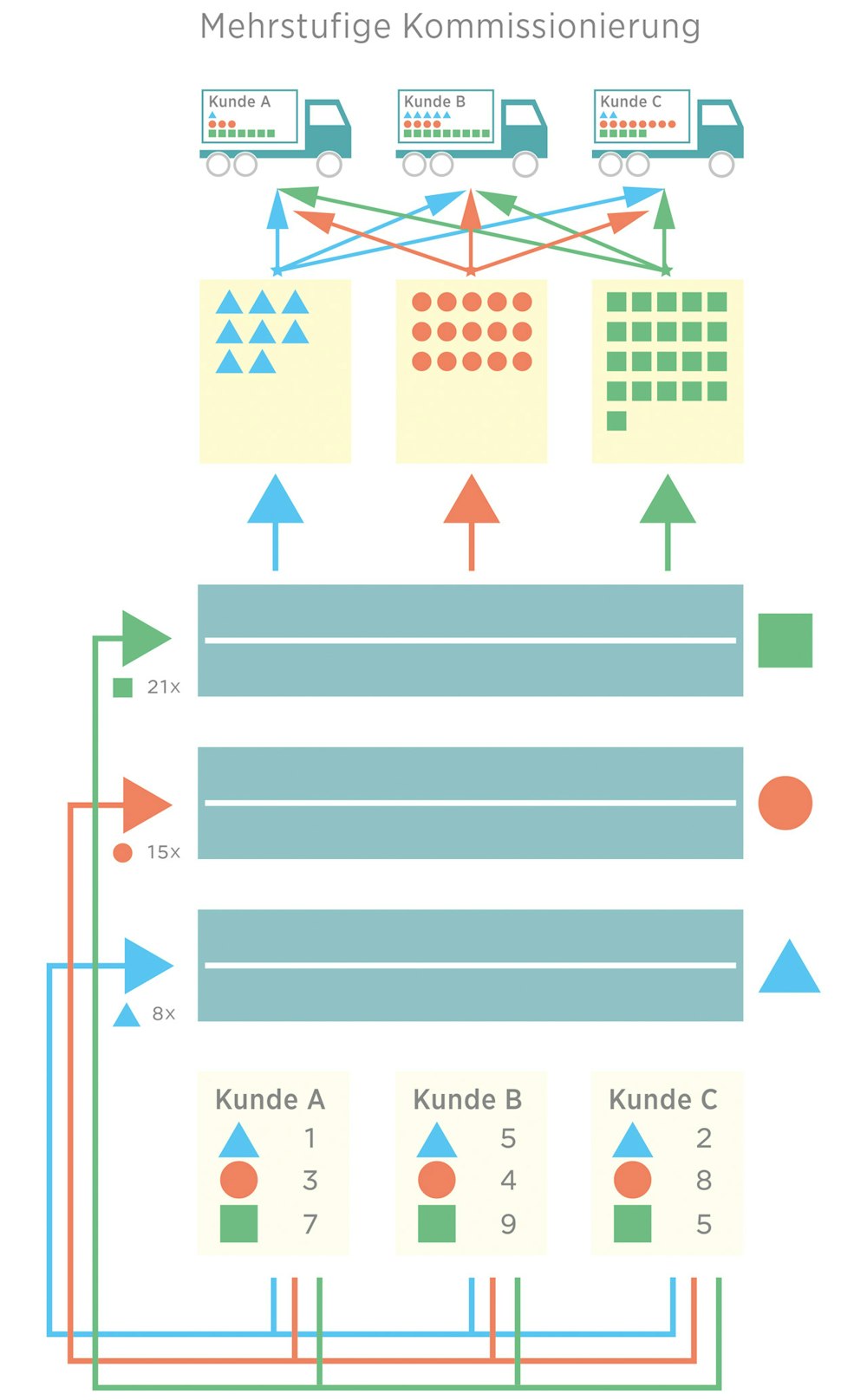
Picking a due o più livelli
Con il prelievo in due fasi, l'intero quantitativo di un articolo può essere prelevato contemporaneamente o in parallelo per un gran numero di ordini. Il numero di accessi ad un articolo è drasticamente ridotto (nel migliore dei casi una sola volta) e quindi anche la quota di percorso nel processo di prelievo. Diversi ordini vengono raggruppati in un ordine totale (una commissione), poi raccolti in base agli articoli e confezionati in seguito in base agli ordini. L'utilizzo di un'istanza di smistamento a valle (selezionatore completamente automatico o manuale) consente un ampio disaccoppiamento dal riferimento dell'ordine durante il prelievo dell'ordine. Il picking a due stadi è chiamato anche picking in serie e parallelo. Al giorno d'oggi vengono raggruppati fino a 10.000 articoli in un solo ordine. Un grande vantaggio è che le frequenze dei contenitori nelle singole aree di stoccaggio sono notevolmente ridotte e i limiti prestazionali della tecnologia di trasporto sono meno sfruttati. Poiché molti ordini vengono scambiati con pochi o molti articoli, il picking in due fasi è adatto, ad esempio, per la vendita per corrispondenza o per i grossisti di prodotti farmaceutici.
Pick-by-Light
Si tratta di una procedura di prelievo ottica, senza supporto cartaceo. Le luci di facile lettura, posizionate direttamente sul luogo di stoccaggio, indicano dove deve essere presa l'unità successiva. Un display indica inoltre il numero di unità da prelevare. Dopo il prelievo, il picker conferma il processo premendo un pulsante e il segnale scompare. Pick-by-Light viene utilizzato per alte velocità di prelievo con basse percentuali di errore.
Pick-by-Voice
Si tratta di una procedura di prelievo a voce, senza supporto cartaceo. Il picker può tenere le mani libere e concentrarsi indisturbato sul prelievo. Il sistema di gestione del magazzino (WMS) trasmette gli ordini tramite un cliente vocale e li riporta direttamente al WMS dopo la conferma. Non è necessaria alcuna ricerca dispendiosa in termini di tempo, i tassi di errore si riducono e le prestazioni di prelievo aumentano.
Scelta per ogni terminale
I dati vengono trasmessi via radio ad un terminale installato in modo permanente sul mezzo di movimentazione industriale. Questa procedura di prelievo viene utilizzata dalle aziende che commerciano prevalentemente merci di grandi dimensioni e ingombranti. Dato che il terminale viene azionato in modo intuitivo, non è necessario troppo tempo per l'apprendimento dei picker. Il tasso di errore è molto basso, ma le barriere linguistiche dei dipendenti possono diventare fonti di errore.
Pick-by-MDE / Pick-by-Scan
Il pick-by-scan coinvolge i dipendenti che si spostano attraverso il magazzino con terminali mobili o carrelli elevatori per la raccolta mobile dei dati. La lista di prelievo viene visualizzata direttamente ai dipendenti dall'LVS sulla rispettiva unità PDC. Gli articoli rimossi vengono confermati sull'apparecchio e possono essere inserite anche quantità mancanti o quantità zero. Lo stato attuale del processo di prelievo può essere monitorato nel WMS. Tra i vantaggi vi sono tempi di ricerca più brevi e meno errori di prelievo. Gli svantaggi sono un investimento iniziale relativamente elevato (fino a 2000 Euro per ogni dispositivo MDE) e il prelievo non a mani libere.