Optimiser la chaîne de valeur grâce aux AGV
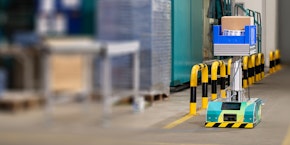
La quatrième révolution industrielle, avec le standard industriel 4.0, définit le cadre de l’évolution de l’industrie, des entreprises et des technologies utilisées. Les machines, les installations, les appareils et les systèmes cyber-physiques doivent être mis en réseau et communiquer entre eux pour, au final, optimiser l’ensemble de la chaîne de valeur (1). Par chaîne de valeur, on entend une série ordonnée d’activités au cours desquelles des valeurs sont créées et des ressources consommées pour produire des produits et des services (2). La production dite « intelligente » conduit à une amélioration des performances de fabrication grâce à l’analyse d’énormes quantités de données issues des systèmes en réseau et à l’automatisation des processus. L’utilisation de l’intelligence artificielle (IA, 3) permet de simuler des processus sur un jumeau numérique d’une installation ou d’une usine entière. L’analyse prédictive (Predictive Analytics) permet d’identifier des tendances, par exemple en ce qui concerne le comportement de la demande des clients d’une entreprise. De cette manière, le marketing et les ventes d’une entreprise peuvent également s’y adapter. La maintenance prédictive (Predictive Maintenance) doit permettre d’éviter la défaillance imminente de composants ou la panne de machines et d’installations entières, et donc les temps d’arrêt. L’analyse des données avec l’IA permet en outre de détecter une production ralentie ou inefficace et de la corriger en conséquence.
Automatisation pour améliorer la chaîne de valeur
Il existe également un potentiel d’optimisation, en particulier dans la logistique interne des entreprises. Par conséquent, les processus de l’entreprise ainsi que les flux de marchandises de la chaîne de valeur peuvent être automatisés et optimisés de manière particulièrement simple, notamment grâce à des systèmes de transport sans conducteur (4, 5). Selon la directive VDI 2510 « Systèmes de transport sans conducteur », un AGV se compose d’un ou de plusieurs véhicules sans conducteur pour le transport, de systèmes de contrôle de la puissance, de localisation, d’acquisition de la position et de transmission des données, d’une infrastructure correspondante ainsi que de systèmes périphériques dans l’entreprise, tels que des stations de chargement. Un AGV est un système de convoyage interne (chariot de manutention), généralement composé de plusieurs AGV destinés à tirer ou à porter des marchandises à transporter. Il existe des solutions qui se distinguent notamment par la commande du véhicule. Celle-ci peut être réalisée par exemple sur la base de procédés optiques ou inductifs, de marques magnétiques, de bandes adhésives au sol, de GPS ou de transpondeurs. Pour automatiser le transport et la manutention des marchandises, par exemple dans la production ou la préparation des commandes, on utilise des AGV (Automated Guided Vehicles) avec un entraînement intégré et des dispositifs de manutention actifs ou passifs. Grâce aux AGV, les flux de marchandises peuvent être automatisés de manière permanente, flexible et fiable. Ces systèmes sont facilement évolutifs et adaptables. Les AGV sont en concurrence avec d’autres systèmes de transport comme les chariots de manutention, les convoyeurs suspendus ou des tapis roulants, mais aussi avec la main-d’œuvre humaine. Cependant, les systèmes de production allégés dans l’entreprise exigent de plus en plus un fonctionnement sans chariot élévateur. Jusqu’à présent, l’industrie automobile, par exemple, utilisait encore le plus souvent des trains routiers avec chauffeurs. Mais dans ce domaine, l’automatisation ne cesse de croître. Dans la logistique de production d’une entreprise, les trains routiers et les AGV se complètent parfaitement et permettent un approvisionnement en marchandises et en composants jusqu’à la chaîne de production. Les trains routiers automatisés et les AGV contribueront ici largement à une plus grande valeur ajoutée ou à une chaîne de valeur optimisée.
Avantages et inconvénients des AGV
Les systèmes de transport par AGV présentent un nombre extraordinaire d’avantages (6) pour la valeur ajoutée d’une entreprise, comme par exemple :
Ils sont extrêmement flexibles et adaptables. Le système de transport sans chauffeur, qui se compose généralement de plusieurs véhicules sans chauffeur, peut être configuré et complété par d’autres véhicules en fonction de l’utilisation. Les trajets peuvent être facilement modifiés. En outre, il existe des AGV avec une faible charge utile de quelques kilogrammes jusqu’à des charges lourdes de 50 tonnes par exemple. Les plages de vitesse varient également fortement d’une solution à l’autre, celles-ci étant surtout limitées par l’éventuel trafic de personnes, les distances de freinage et les variations de charge dues aux marchandises transportées.
Il est également facile d’apporter des modifications à la disposition de l’entrepôt, à la structure de l’entrepôt et des marchandises et de les améliorer.
Le taux d’erreur est réduit grâce à l’utilisation de véhicules sans conducteur dans l’entreprise et la productivité des processus de l’entreprise est augmentée, car de nombreux collaborateurs peuvent être retirés de ces domaines de travail (économie de frais de personnel). De plus, il peut être utilisé en permanence, 24 heures sur 24, sans pause, ce qui augmente considérablement la valeur ajoutée et la productivité.
La vitesse des processus intralogistiques est augmentée.
Grâce au nombre réduit d’employés et à l’absence de chariots élévateurs, les accidents sont en grande partie évités. De plus, les collaborateurs en poste ont moins de charge physique à supporter.
Le système s’adapte en outre de manière autonome aux changements de processus en cas de pics de commandes.
Ils peuvent être utilisés aussi bien à l’extérieur qu’à l’intérieur.
Ils sont amortis assez rapidement en raison de l’augmentation de la productivité, de l’optimisation de la chaîne de valeur et des économies de personnel. Par ailleurs, les coûts d’exploitation et de maintenance sont très faibles.
Bien entendu, toute solution avec des véhicules sans chauffeur présente aussi des inconvénients pour une entreprise.
Jusqu’à présent, le système de véhicules autonomes ne peut pas encore réagir seul à des incidents de fonctionnement tels que des rayonnages vides ou des dommages. L’intervention humaine reste nécessaire dans ce domaine.
Le système de véhicules sans conducteur fait concurrence à la main-d’œuvre humaine. Il existe un risque que les humains soient de plus en plus remplacés par l’IA et les robots. Toutefois, une solution peut résider dans l’interaction harmonieuse du savoir-faire et de l’expérience de longue date de l’homme avec l’IA et les robots d’assistance (cobots).
LEO locative
Avec LEO locative (7), BITO propose aux entreprises un système de transport sans conducteur pour améliorer les processus de l’entreprise et optimiser la chaîne de valeur, le tout sans réseau Wi-Fi ni système informatique coûteux (ordinateur de flux de marchandises). LEO suit une piste optique au sol et des marqueurs à code également posés au sol. Le système de transport sans conducteur est conçu comme une application plug-and-play : il suffit de coller la bande de marquée colorée sur le sol dans le sens de la trajectoire souhaitée, de positionner les marqueurs pour les consignes d’arrêt et de déplacement et de placer les stations LEO aux positions d’arrêt définies. Les commandes des marqueurs sont scannées par LEO et directement exécutées. En raison de la configuration facilement modifiable, il est possible d’essayer de nouvelles idées, par exemple celles des processus d’amélioration continue, sans avoir de longs délai d’attente. Pas à pas, il est ainsi possible d’optimiser les processus lors de l’utilisation du système et de trouver la meilleure solution pour le flux de marchandises. L’optimisation des processus d’entreprise, par exemple dans la logistique de production (8), permet d’améliorer la productivité globale de la chaîne de valeur. Les coûts d’investissement pour le système sont très faibles, c’est pourquoi il est amorti en peu de temps.
Références
1 Expertise BITO, Fabrication flexible dans l’usine intelligente, Lien
2 Logistique pour les diplômés en économie, chaîne de création de valeur, Link
3 Expertise BITO, Possibilités d’utilisation de l’IA dans la logistique, Lien
4 Expertise BITO, Numérisation dans l’intralogistique, Lien
5 Expertise BITO, Systèmes de transport sans conducteur - comment garder une vue d’ensemble Lien
6 Raphael Michalek, AGV, Que sont les systèmes de transport sans conducteur ? Définitions et avantages, janvier 2019, MM Logistik, Lien
7 BITO Lagertechnik Bittmann GmbH, LEO Locative, Le système de transport sans conducteur pour bacs et cartons, Lien
8 Expertise BITO, Optimisation du processus dans la logistique de production, Lien