Optimización de la cadena de valor con AGVs
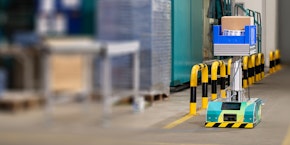
La cuarta revolución industrial con el estándar industrial 4.0 establece el marco para el desarrollo de la industria, las empresas y las tecnologías utilizadas. Las máquinas, las instalaciones, los dispositivos y los sistemas ciberfísicos deben conectarse en red y comunicarse entre sí para, en última instancia, optimizar toda la cadena de valor (1).
Una cadena de valor es una secuencia ordenada de actividades en las que se crea valor y se consumen recursos para producir productos y servicios (2). La llamada producción inteligente permite mejorar el rendimiento de la fabricación mediante el análisis de enormes cantidades de datos procedentes de sistemas conectados en red y la automatización de los procesos.
Mediante el uso de la inteligencia artificial (IA, 3), los procesos pueden simularse en un “gemelo digital“ de una planta o una fábrica entera. El análisis predictivo puede utilizarse para identificar tendencias, por ejemplo en el comportamiento de la demanda de los clientes de una empresa. De este modo, el marketing y las ventas de una empresa también pueden adaptarse a ellas. El mantenimiento predictivo pretende evitar el fallo inminente de componentes o el fallo de máquinas y sistemas enteros y, por tanto, los tiempos de inactividad. El análisis de datos con IA también permite detectar la producción ralentizada o ineficiente, y consecuentemente, corregirla.
Automatización para mejorar la cadena de valor
También existe potencial de optimización en la intralogística de las empresas. En este caso, los procesos de la empresa y los flujos de materiales y mercancías de la cadena de valor pueden automatizarse y optimizarse con especial facilidad, por ejemplo, mediante vehículos de guiado automático (AGV) (4, 5).
Según la directriz VDI 2510 "Vehículos de guiado automático", un AGV se compone de uno o varios vehículos sin conductor para el transporte, sistemas para el control del rendimiento, la determinación de la ubicación, la detección de la posición y la transmisión de datos, una infraestructura correspondiente, así como sistemas periféricos en la empresa, como estaciones de carga.
Un AGV es un sistema de transporte interno que circula por el suelo del almacén (como una carretilla industrial) que suele constar de varios vehículos AGV para arrastrar o transportar mercancías. Existen soluciones que se diferencian, entre otras cosas, por el sistema de control de los vehículos. Esto puede realizarse, por ejemplo, mediante procesos ópticos o inductivos, marcas magnéticas, tiras adhesivas en el suelo, GPS o transpondedores.
Para la automatización del transporte y la manipulación de materiales, por ejemplo en la producción o la preparación de pedidos, se utilizan vehículos de guiado automático (AGV) con accionamiento integrado y dispositivos de manipulación de carga activos o pasivos. Los AGV permiten automatizar el flujo de mercancías y materiales de forma permanente, flexible y fiable. Son fácilmente ampliables y adaptables. Y por ello, los AGV pueden competir con otros sistemas de transporte, como las carretillas industriales, la tecnología de transporte, como los transportadores aéreos o las cintas transportadoras, pero también con la mano de obra humana.
Sin embargo, los sistemas de producción ajustada (“lean production“) de las empresas exigen cada vez más un funcionamiento sin carretillas elevadoras. Hasta ahora, por ejemplo, la industria automovilística ha utilizado sobre todo sistemas (trenes de remolque) con conductor. Pero es un hecho que la automatización también aumenta constantemente en este ámbito. En la logística de producción de una empresa, los trenes remolcadores y los vehículos autoguiados se complementan a la perfección y permiten suministrar material y componentes directamente a la línea de montaje. Los trenes de remolque y AGV automatizados contribuirán en gran medida a una mayor creación de valor y a una cadena de valor optimizada.
Ventajas e inconvenientes de los AGV
Los vehículos de guiado automático presentan un extraordinario número de ventajas (6) para la creación de valor en la empresa, como son:
Su elevada flexibilidad y adaptabilidad. El sistema de transporte sin conductor, que suele constar de varios vehículos sin conductor, puede configurarse y completarse con vehículos adicionales en función de la aplicación. Las rutas pueden modificarse fácilmente. Además, existen AGV con cargas útiles bajas de unos pocos kilogramos hasta la gama de carga pesada con, por ejemplo, 50 toneladas. Los rangos de velocidad de las soluciones también varían mucho, ya que están limitados principalmente por el posible tráfico de pasajeros, las distancias de frenado y los cambios de carga provocados por las mercancías transportadas.
También se pueden realizar y mejorar fácilmente cambios en la disposición del almacén y en la estructura de la mercancía.
Se reduce la tasa de errores mediante el uso de vehículos sin conductor en la empresa y aumenta la productividad de los procesos de la empresa, ya que muchos empleados pueden ser retirados de estas áreas de trabajo (ahorro en costes de personal) y ser desplazados a otras áreas y tareas de mayor valor añadido. Además, pueden utilizarse permanentemente las 24 horas del día sin interrupción, lo que aumenta enormemente la creación de valor y la productividad.
Se incrementa la velocidad de los procesos intralogísticos.
Debido al menor número de empleados y a la ausencia de carretillas elevadoras, casi no se producen accidentes. Además, se descarga físicamente al resto de empleados.
El sistema también se adapta de forma autónoma a los procesos cambiantes durante los picos de pedidos.
Se pueden utilizar tanto en exteriores como en interiores.
Se amortizan con bastante rapidez gracias al aumento de la productividad, la optimización de la cadena de valor y el ahorro de personal. Además, los costes de funcionamiento y mantenimiento son muy bajos.
Lógicamente, toda solución con vehículos sin conductor también puede tener desventajas para una empresa.
El sistema de vehículos de guiado automático aún no puede reaccionar por sí solo ante fallos operativos como estanterías vacías y averías. Aquí todavía tienen que intervenir los humanos.
El sistema de vehículos sin conductor compite con la mano de obra humana. Existe el peligro de que los humanos sean sustituidos cada vez más por IA y robots. Sin embargo, una solución puede residir en la interacción armoniosa de los conocimientos y la experiencia de los humanos con la IA y los robots de apoyo (cobots).
FTS LEO locative
Con LEO locative (7), BITO ofrece a las empresas un sistema de transporte sin conductor para mejorar los procesos empresariales y optimizar la cadena de valor, que no requiere WLAN ni costosas tecnologías de la información (TI), como pueden ser ordenadores de flujo de materiales.
LEO se controla mediante una cinta óptica pegada al suelo, que actúa como un riel, así como otros marcadores también pegados al suelo que indican paradas, giros, etc.
El sistema de transporte sin conductor está diseñado como una aplicación "plug and play": basta con pegar la cinta de color del riel en el suelo en la dirección de desplazamiento deseada, colocar los marcadores para las órdenes de parada y desplazamiento y situar las estaciones LEO en las posiciones de parada definidas. Los comandos de los marcadores son escaneados por el LEO y ejecutados directamente. Gracias a la configuración fácilmente modificable es posible probar nuevas ideas, por ejemplo de los grupos de trabajo CIP, sin largos tiempos de espera. Así, paso a paso, se pueden optimizar los procesos al utilizar el sistema y encontrar la mejor solución para el flujo de materiales.
Mediante la optimización de los procesos de la empresa, por ejemplo en la logística de producción (8), se mejora toda la productividad de la cadena de valor. Los costes de inversión del sistema son muy bajos, por lo que la solución se amortiza en poco tiempo.
Literatura
1 BITO Fachwissen, Flexible Fertigung in der Smart Factory, Link
2 Logistik für Wirtschaftsfachwirte, Wertschöpfungskette, Link
3 BITO Fachwissen, Einsatzmöglichkeiten von KI in der Logistik, Link
4 BITO Fachwissen, Digitalisierung in der Intralogistik, Link
5 BITO Fachwissen, Fahrerlose Transportsysteme - so behalten Sie den Überblick, Link
6 Raphael Michalek, Fahrerlose Transportsysteme, Was sind fahrerlose Transportsysteme? Definition & Vorteile, Januar 2019, MM Logistik, Link
7 BITO Lagertechnik Bittmann GmbH, LEO Locative, Das fahrerlose Transportsystem für Behälter und Kartonagen, Link
8 BITO Fachwissen, Prozessoptimierung in der Produktionslogistik, Link