La “Black Week“: Optimización del picking en las horas punta
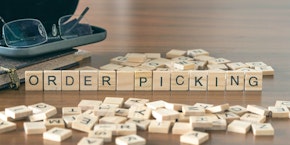
Originalmente, el Black Friday se originó en Estados Unidos y sirvió para aumentar las ventas minoristas al comienzo de la temporada de compras navideñas. El Black Friday cae el viernes siguiente a la festividad de Acción de Gracias. El Día de Acción de Gracias se celebra siempre el cuarto jueves de noviembre en Estados Unidos. Por otra parte, el Viernes Negro ha sido adoptado en muchos países y también se ha ampliado hasta convertirse en la “Black Week“ (Semana Negra). La semana de descuentos y rebajas se extiende ahora desde el lunes anterior al Black Friday hasta el llamado Cyber Monday.
Ya generalizado por todo el mundo, en España el Black Friday tiene lugar en España desde hace años, y la mayoría de los descuentos se ofrecen on line. Por ejemplo en Alemania, donde se implantó desde 2013, entre ese año y 2020 se han generado unos 5.000 millones de euros, y las ventas de la Black Week en Alemania no paran de aumentar (2).
La avalancha de pedidos provoca retos en el almacén
La Black Week, al igual que otros periodos de picos de ventas, supone un enorme reto para las empresas y su logística, que tienen que hacer frente a una auténtica avalancha de pedidos en poco tiempo. Se ve especialmente afectada toda la logística, el almacén y sobre todo la preparación de pedidos (3), así como el área de aprovisionamiento. Lógicamente, esto plantea la cuestión de cómo el almacén y el área de preparación de pedidos pueden hacer frente a un repentino y drástico aumento de los pedidos. ¿Cómo puede una empresa ajustarse a estos espectaculares picos de ventas? ¿Qué tipos y métodos de preparación de pedidos son adecuados? ¿Cómo puede establecerse un sistema de almacenamiento óptimo en la empresa? ¿Cómo gestionar la automatización de los procesos en general?
¿Cómo se puede optimizar el picking?
Para poder hacer frente al aumento súbito de los pedidos, los procesos de la empresa y del almacén deben ser fácilmente escalables. En un almacén manual, esto significa, en primer lugar, que hay que contar con más empleados y, posiblemente, con más puestos de picking. En este caso, el personal auxiliar suele contratarse a través de empresas de trabajo temporal, estudiantes en periodos de prácticas, etc. Sin embargo, hay que formarlos muy rápidamente, lo que a menudo contribuye a una mayor frecuencia de errores en el almacén manual o en el picking manual.
La ventaja de los procesos y almacenes automatizados es, por un lado, la velocidad de procesamiento de los pedidos o el mayor rendimiento, la menor frecuencia de errores y una más fácil escalabilidad.
Por otro lado, los almacenes manuales trabajan según el principio de “hombre a mercancía“, lo que supone una gran carga para los empleados. Los almacenes automatizados funcionan según el principio de "mercancía a hombre" (aunque también lo hacen las estanterías manuales), lo que es mucho más ergonómico y libera de mucha tensión al personal. Con todo, el sector del comercio electrónico no se presta a la automatización total del almacén debido a la gran variedad de productos con pedidos a veces muy reducidos en cantidad y muy variados en referencias. En estos casos, la automatización parcial de los procesos mediante robots de almacenaje y picking, cobots y vehículos de guiado automático (AGV) puede ser a menudo más prometedora para la optimización en el almacén.
Ventajas de un sistema de gestión de almacenes
La introducción de un sistema de gestión de almacenes (SGA, 4) suele ser rentable y conduce a una mayor transparencia de las existencias y a la optimización del almacenamiento. Un SGA constituye la base de las soluciones automatizadas. Además, permite una asignación caótica de los almacenes.
Un SGA ofrece muchas ventajas, como la gestión y el control simplificados y eficaces del almacén, el aumento de la eficiencia, la reducción de las tasas de error y el aumento de la fiabilidad del proceso. Además, el SGA permite un rápido intercambio de datos, tiempos de reacción cortos, así como la adaptación y flexibilidad de las operaciones. Asimismo, permite la conexión en red de sucursales y filiales y la conciliación óptima de las existencias.
Elegir el método de picking adecuado
Cuando se trata de la eficiencia del proceso de picking, la minimización de los tiempos de picking (tiempo base, tiempo de desplazamiento, tiempo de recogida, tiempo muerto, tiempo de distribución, 5, 6) mediante medidas organizativas y técnicas desempeña un papel importante. En los sistemas de “mercancía a hombre“, el tiempo de desplazamiento es, por supuesto, cero. La tecnología de transpondedores RFID también se utiliza cada vez más en la preparación de pedidos. Uno de los motivos es la automatización y la digitalización en el marco de la norma Industria 4.0. Los procesos especiales de preparación de pedidos, como el Pick-by-Light, el Pick-by-Voice, el Pick-by-Terminal, el Pick-by-MDE y el Pick-by-Point® (3) se están trasladando a la preparación de pedidos. Los sistemas Pick-by-Light y Pick-by-Voice, en particular, ofrecen un gran potencial de optimización y mejor ergonomía para el preparador de pedidos. Pick-by-Voice es un proceso de preparación de pedidos sin papel y controlado por voz. La solución permite al preparador centrarse completamente en la preparación de pedidos. Además, sus manos permanecen libres para el proceso de picking. El SGA transmite las órdenes de picking a través del cliente de voz, el preparador confirma el picking, que se comunica directamente al SGA. De este modo, se eliminan las intermninables búsquedas, se reducen las tasas de error y se optimiza el rendimiento del picking.
Si utiliza sistemas de almacenamiento basados en el principio de “hombre a mercancía“, debe organizar la mercancía en función del tamaño de la demanda. Los artículos de alta rotación deben almacenarse lo más cerca posible de los puestos de picking. En general, también conviene optimizar las existencias (4, 7) y planificar las ventas con antelación (véase más adelante). Los artículos también deben organizarse en clases de productos para evitar búsquedas complicadas y que impliquen demasiado tiempo. Si el almacenamiento ya está organizado y controlado con un SGA, el sistema suele encargarse también de la optimización de las rutas para un picking eficaz.
Picking en un paso y en dos pasos
Al hacer el picking en el almacén, se utilizan diferentes métodos de composición de pedidos: en serie o en paralelo orientados a los pedidos (picking de una etapa), en paralelo orientados a las series (picking de dos o varias etapas). También se utilizan sistemas de picking manuales o automatizados.
La combinación de pedidos en serie y en paralelo es especialmente adecuada para cuando hay muchos pedidos (más de 1.000) con pocos artículos (de 1 a 5), es decir, especialmente para el comercio electrónico. Con esta solución, los artículos idénticos de diferentes pedidos se combinan en serie y se procesan en paralelo en diferentes zonas de almacenamiento. Esto reduce drásticamente el volumen de accesos a un artículo y también la distancia del proceso de picking. Varios pedidos se combinan en un pedido total, luego se hace el picking orientado a los artículos y solo después se distribuye y embala orientado a los pedidos. Esto permite optimizar los recorridos de picking del preparador de pedidos para cada artículo. También se tienen en cuenta otros factores como la superficie de almacenamiento, el peso, el volumen y las cantidades. Por supuesto, los artículos también pueden alimentarse según el principio de “mercancía a hombre“ o recogerse con robots de picking.
Tras el picking, es necesario un proceso de clasificación eficiente para que el artículo en cuestión pueda ser asignado a su pedido correspondiente. Sin embargo, los sistemas de clasificación y distribución necesarios (clasificadores) son bastante costosos. La eficacia del picking en dos o varias etapas es mucho mayor que la del picking en una sola etapa.
Utilizar la planificación predictiva de ventas con IA
Existen soluciones de software de inteligencia artificial (IA) para la optimización y disposición de los inventarios que permiten ajustar los niveles de existencias a la fluctuación de la demanda.
Basándose en las cifras de ventas de años anteriores e incorporando métodos estadísticos, se calcula automáticamente la cantidad óptima de pedidos para un periodo concreto (planificación y previsión predictivas). Las fluctuaciones estacionales se incluyen en la previsión, y los cambios espontáneos de la demanda se suavizan mediante algoritmos. Si se quiere alcanzar un nivel de servicio muy alto y, por tanto, garantizar la ejecución inmediata de un gran número de pedidos, las existencias de seguridad en el almacén deben ser consecuentemente elevadas (7). En general, esto permite a la empresa ajustarse mucho mejor a las horas punta.
Literatura:
1 Black Friday, Wikipedia, Link
2 Statista, Aktionsausgaben durch Online-Shopper an Black Friday und Cyber Monday in Deutschland (2016 bis 2020), Link
3 BITO Fachwissen, Was versteht man unter Kommissionierung?, Link
4 BITO, Checkliste "Tipps zur Erhöhung der Produktivität und Lagerleistung", Link
5 BITO Fachwissen, Mehr Effizienz durch beleglose Kommissionierung plus Whitepaper "Das 1x1 der Kommissionierung", Link
6 Kommissionierung, Luca Logistics Solutions, Link
7 BITO Fachwissen, Optimieren Sie Ihre Lieferperformance, Link