El contenedor: factor clave en el flujo de material
Los contenedores juegan un papel importante en el flujo de material. Como portadores de carga y transmisores de información, también son muy importantes para la optimización de los procesos en la empresa.
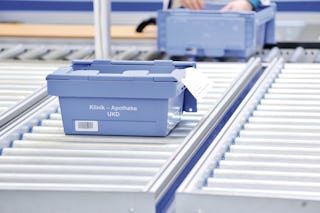
El diseño o la selección correcta de los contenedores es extremadamente importante para el flujo ininterrumpido de materiales en una empresa. No solo actúan como portadores de carga en la logística, sino también como transmisores de información y, por lo tanto, constituyen la base de los sistemas Kanban. También desempeñan un papel importante en la optimización de los procesos en la empresa. Por ejemplo, el diseño de los contenedores tiene un enorme impacto en las características de funcionamiento y en la generación de ruido en las líneas de transporte. Por lo tanto, también son una parte importante del diseño de los lugares de trabajo ergonómicos.
No solo los transportadores de carga
El flujo de material incluye todos los procesos desde la extracción de las materias primas, pasando por el procesamiento y el tratamiento, hasta la distribución al proveedor y la ruta hasta el consumidor final. También incluye los procesos relacionados con el transporte y la logística, el almacenamiento y las pruebas de producto. Si tiene lugar dentro de la empresa, se denomina flujo de material interno. Suele ir acompañado de un flujo de información, que se registra, transporta, procesa y produce en forma de datos. Los contenedores desempeñan un papel importante en el almacenamiento, el transporte y la transferencia de información. Sin embargo, el flujo de material solo puede automatizarse mediante la normalización de los portadores de carga.
Los portadores de carga como paletas, cajas, contenedores, etc. deben estar claramente definidos, es decir, normalizados, de modo que los transelevadores, las lanzaderas, los vehículos de guiado automático (AGV), los camiones industriales y la tecnología de transporte puedan aprovechar todo su potencial en la logística. Por ejemplo, los pequeños transportadores de carga (KLT), también conocidos como eurocontenedores o eurocajas. Por lo tanto, pueden ser enviados para su reciclaje conjunto. Los KLT se desarrollaron para optimizar la cadena logística en la industria de fabricación y suministro de automóviles. El sistema se adapta de forma modular a las superficies de base de 1200 × 800 mm (europallet) y 1200 × 1000 mm (ISO). La superficie base se duplica en cada caso y tiene las dimensiones nominales 300 × 200 mm, 400 × 300 mm y 600 × 400 mm. Asimismo, los eurocontenedores también se utilizan fuera de la industria automotriz debido a su estandarización. Los contenedores también sirven como portadores de información gracias a su número de identificación único (almacenado en el código de barras, RFID). En el sistema de gestión de almacenes (SGA) o en el ordenador de flujo de materiales, esta identificación está vinculada a un artículo o pedido específico. Esto permite el reconocimiento y el control automáticos de los contenedores y las mercancías en el almacén.
Ejemplos de diseño funcional de contenedores
Las propiedades mecánicas de las cajas modernas permiten una amplia gama de operaciones de logística. Por ejemplo, los contenedores de los sistemas de transporte deben funcionar de la manera más silenciosa y con la menor fricción posible. También hay tolerancias extremadamente pequeñas para la desviación de la base del contenedor. Por ejemplo, la XL-Motion de BITO ha sido diseñada especialmente para almacenes automatizados, de manera que cumple óptimamente los requisitos de planitud, rugosidad y coeficiente de fricción. Esto se asegura con el nuevo piso giratorio. Para poder soportar altas cargas durante el funcionamiento del almacén, se ha equipado con una construcción de bastidor liso que se conecta a la caja con costillas de apoyo diagonales. Esta construcción en forma de sándwich evita que el piso se doble bajo altas cargas. Debido a que siempre es plano y liso, la caja XL-Motion funciona de forma extremadamente silenciosa en el sistema de transporte. Esto hace que el ambiente de trabajo en el almacén sea mucho más agradable. El bajo nivel de ruido no solo conlleva un menor estrés y, por tanto, un menor tiempo de inactividad, sino también a menos errores y a una mayor satisfacción en el trabajo.
Las bandejas se utilizan en los almacenes automáticos de piezas pequeñas para transportar y almacenar mercancías no transportables como cajas de cartón. Están especialmente adaptadas a los requisitos de la tecnología de transporte correspondiente. Para la carga y descarga automática, existe una función de elevación que separa la mercancía de la bandeja. La mercancía puede ser apilada en pallets, por ejemplo.
Sistemas y contenedores Kanban
El Kanban es un método de control descentralizado de la producción, en el que los procesos individuales de producción y logística se activan con la ayuda de tarjetas de datos - conocido como Kanban en japonés. Las ventajas del método Kanban son el control descentralizado, el almacenamiento ajustado y la logística Just-In-Time (JIT) de las piezas necesarias para la producción. Los datos importantes, como el número de artículo, la cantidad, el lugar de almacenamiento, etc., se anotan en las tarjetas. Por lo tanto, la producción envía una señal a la etapa de producción anterior de que se necesitan nuevas piezas. Por ejemplo, un contenedor vacío con una tarjeta de pedido para un componente específico se envía al almacén (Lean) y un contenedor lleno se retira de nuevo. El almacén de piezas sabe ahora que este artículo debe ser pedido de nuevo en una determinada cantidad y envía este pedido a la fuente (el proveedor). El proveedor cumple la orden y lleva el componente correspondiente al almacén en la cantidad deseada. Por lo tanto, la tarjeta kanban sirve como tarjeta de pedido para la fabricación, lo que desencadena una determinada orden de fabricación o una “onda de resonancia”. En el sistema Kanban, ninguna persona individual necesita conocer toda la cadena de procesos. Solo se rellena el contenedor Kanban abierto en el punto local correspondiente. Por lo tanto, el sistema demuestra ser autorregulado y auto-organizado y se basa en el conocimiento local y en reglas simples. Hoy en día, se utilizan medios de almacenamiento como códigos de barras o chips RFID en lugar de la tarjeta Kanban. Aquí, los datos o la orden de producción se transfieren vía WIFI al sistema de gestión de almacenes, al sistema ERP o al correspondiente proveedor de componentes.
Punto de partida para la optimización del proceso
Especialmente en la era de la Industria 4.0, los flujos de trabajo y los procesos deben ser optimizados y racionalizados incluso en las empresas más pequeñas. Un buen punto de partida es el transporte y el flujo de materiales. Concretamente, los tiempos de rendimiento de los materiales y productos deben ser revisados. Estos pasan por estaciones innecesarias, de ahí que los tiempos de procesamiento puedan ser acortados. Cada reducción de los tiempos de producción significa un ahorro de costes. ¿Se utiliza el medio de transporte óptimo en cada punto de la empresa? ¿Son necesarias las construcciones especiales? Los contenedores de transporte son, por supuesto, igual de importantes. ¿Se utilizan los contenedores de transporte adecuados para los productos, los puestos de trabajo y los procesos? En este punto es donde el almacenamiento, el transporte o la intralogística pueden racionalizarse de manera decisiva, lo que puede reducir los costos.
Importancia de las estanterías en el flujo de materiales
Las estanterías suelen ser la fuente o el sumidero del flujo de material. Es decir, las mercancías se retiran de la estantería y se colocan en el flujo de material, o bien las mercancías proceden de la entrada de mercancías o del área de producción y se transportan a las estanterías y se almacenan. A veces, sin embargo, el flujo de material también tiene lugar en las estanterías, por ejemplo, en los estantes de flujo para pallets o contenedores y cajas de cartón. Puede tratarse de una acción de reposición en un sistema Kanban o de una acción de control de reposición en un proceso de picking. En este caso, la dirección del flujo del sistema de estanterías dinámicas desde la entrada en almacén hasta la salida garantiza automáticamente un movimiento según el principio FIFO (primero en entrar, primero en salir). Las zonas de seguridad intermedias asumen una función adicional en el flujo de materiales. En el caso del picking de varios niveles, por ejemplo, las cajas de pedidos "recogidas" suelen tener que esperar en una estantería para los demás artículos.
¿Le gustaría hacer más eficiente el flujo de material? Podemos ayudarle con esto.