Facts & Challenges
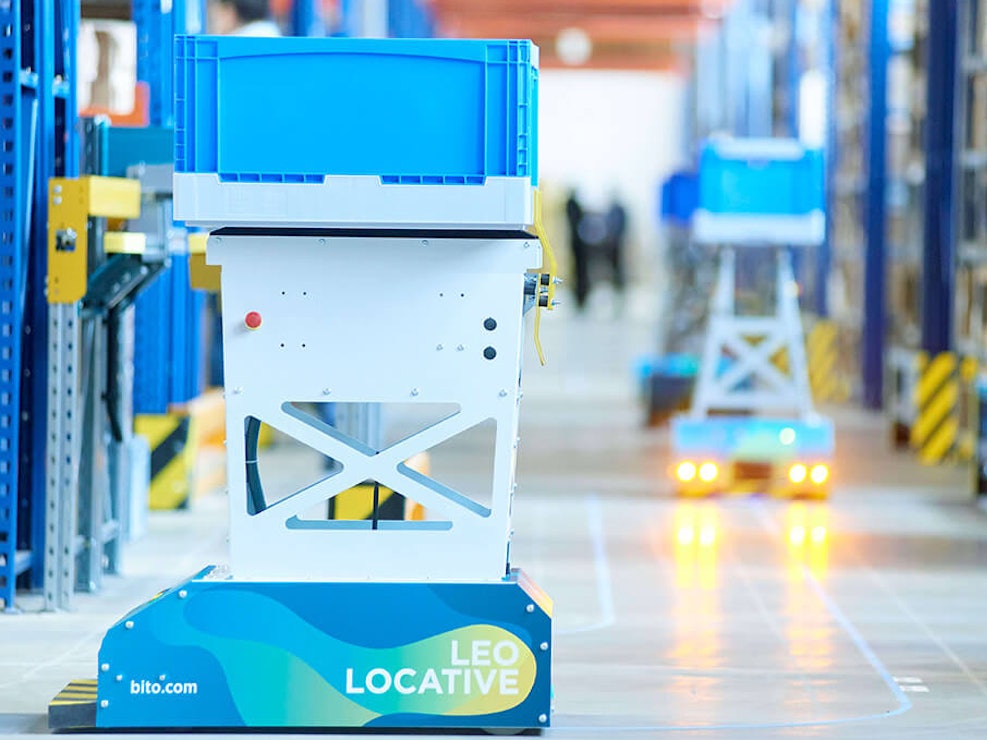
Production logistics refers to the planning, control and optimisation of material flows and logistical processes in industrial production. It aims at ensuring the smooth supply of materials, components and resources within a company. As all manufacturing companies must look at material flow processes in their value chain, production logistics is not considered a separate field. Production logistics deals with sub-areas such as material flow planning, production planning and control, inventory management, quality assurance and supplier management. Material flow planning includes determining storage positions, defining transport routes and avoiding bottlenecks. Production planning and control are used to define production targets, plan production processes and coordinate a wide range of production activities. Warehouse management involves determining optimum order quantities, minimising stock levels and avoiding bottlenecks or excess stock.
Industry 4.0 and the evolution of smart production logistics
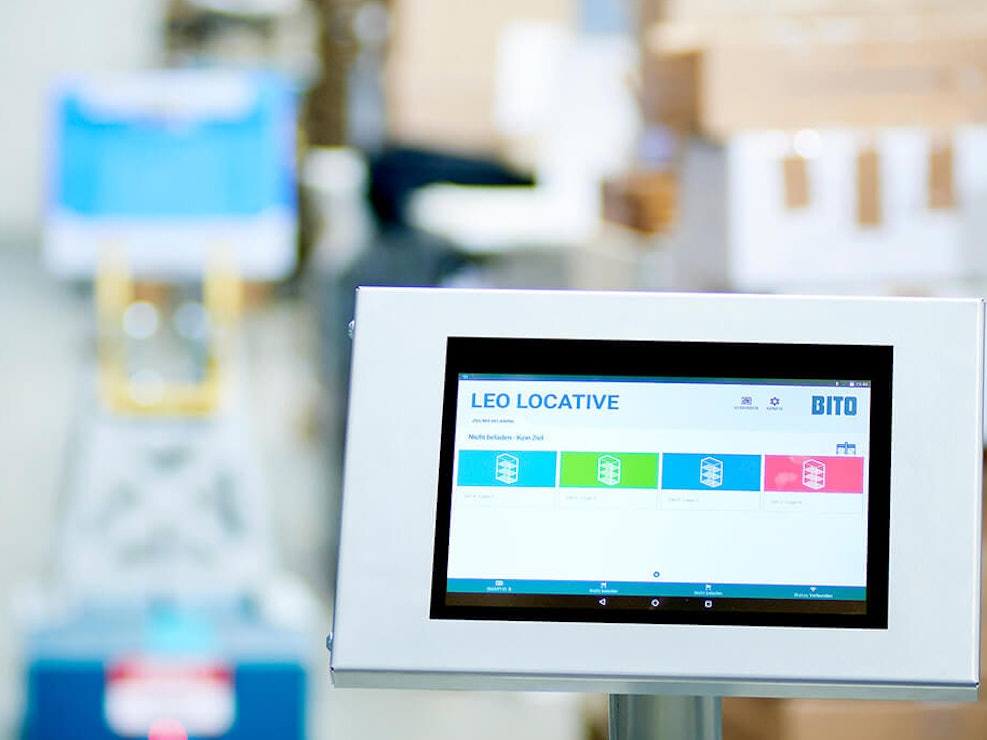
Industry 4.0 technologies such as digitisation, automation and machine networking are leading to the evolution of intelligent production processes, hence smart production logistics. Machines, systems and cyber-physical systems can exchange data with each other. By using artificial intelligence (AI) and the digital twin of the factory, large amounts of data (big data) can be analysed. This leads to the step-by-step optimisation of production and production logistics. Smart production enables batch size 1, i.e. customised production, to be realised. Implementing customised production generally requires advanced manufacturing technologies and flexible production processes, digitisation, automation, robotics and digital manufacturing technologies. As a result, production becomes highly complex and therefore requires equally complex and intelligent production logistics. The solution for efficient, cost- and resource-saving production is to use dynamic systems, improved networking and decentralised warehouses. This means that the industrial revolution and digital transformation are also finding their way into production logistics.
Trends in production logistics
The fourth industrial revolution (Industry 4.0) is based on digitisation, automation and networking as well as big data analysis through artificial intelligence. Production becomes more customised, more complex, more efficient and more economical in terms of costs and resources.
New Industry 4.0 manufacturing technologies such as rapid prototyping and additive laser manufacturing dominate the smart factory.
Highly complex production processes require smart production logistics which can be realised by networking systems as a part of Industry 4.0, by collecting real-time data, using artificial intelligence and predictive analytics, automation, robotics, intelligent warehousing and supply chain integration.
Intelligent warehousing:
By using IoT and RFID technologies, stock levels can be monitored and controlled in real time. This enables efficient inventory management, avoids overstocking and reduces storage costs.
Smart production logistics integrate multiple players in the supply chain, including suppliers, manufacturers, logistics services providers and customers. Material flows are seamlessly coordinated through data communication and real-time data exchange, bottlenecks are avoided and the responsiveness to changes in the supply chain is improved.
Decentralised warehouses contribute to efficient production. Decentralisation can shorten transport routes, create customer proximity, avoid bottlenecks, improve and reduce stock levels and reduce the risk of disruptions in the supply chain.
Smart production logistics also contribute to greater sustainability for companies. Industry 4.0 optimises production and logistics processes, improves transparency along the supply chain, makes efficient use of resources, optimises the disposal, reuse and recycling of materials, reduces emissions and supports other sustainable practices such as route optimisation.
What are the requirements for logistics?
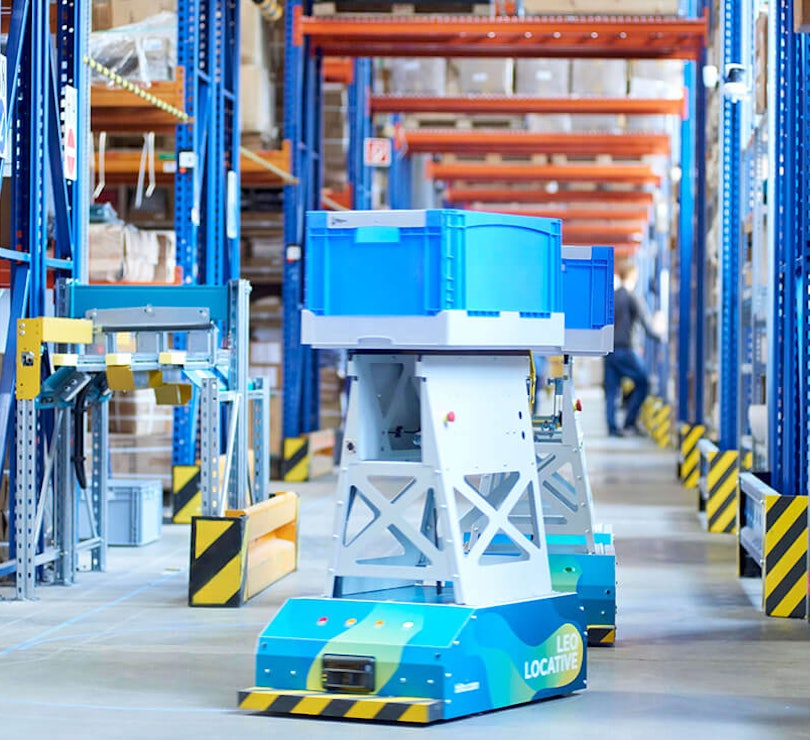
The task of smart production logistics against the backdrop of the digital transformation in the production environment is to provide corresponding lean, holistic, intelligent and optimised logistics processes for the industrial sector. The digital factory also includes intelligent connected production logistics, as materials and goods need to be transported to their destination ever faster. By digitising and connecting machines, systems, vehicles and cyber-physical systems, AI-based software solutions can significantly optimise material flows. The actual material requirements of production, for example, serve as the basis. AI calculates ideal routes for transport and organises material flows to increase efficiency and optimise costs and resources. In addition, all material flows within and outside the factory become transparent. Intelligent production logistics and intralogistics use for example warehouse management systems (WMS), automated transport systems such as automated guided vehicles (AGVs), sensor technology and the Internet of Things (IoT), RFID technology, AI and big data analysis, virtual and augmented reality (VR, AR).
AGVs are increasingly being used to connect individual production, assembly or order picking areas and to automate material flow. With LEO Locative, BITO has launched a particularly innovative and inexpensive AGV that operates without Wifi or a central computer. The LEO vehicle is guided by an optical track and code markers applied to the floor. LEO self-installs and is immediately ready for use (plug and play). LEO routes can be quickly adapted to new requirements. It is also possible to use a tablet for communicating transfer stations to LEO. Stops along the route and destinations are determined by markers on the ground. The LEO system, combining a LEO vehicle and LEO stations, is ideal for any application where materials need to be moved to specific points along same routes x-times a day. LEO saves many kilometres of travel routes that would otherwise have to be covered by employees, thereby improving ergonomic conditions at work. LEO AGVs are also flexibly adaptable and scalable and help to streamline material flow patterns.
The BITO portfolio also includes automated storage and order picking systems as well as matching bins and containers to help you with all automation requirements in internal distribution and production logistics.