Facts & Challenges
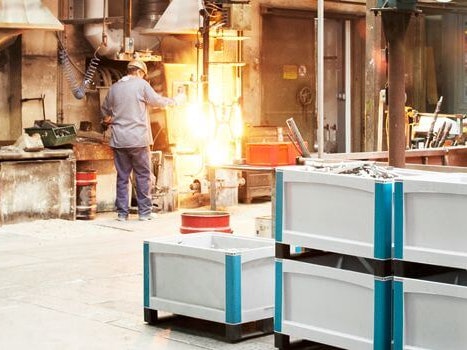
Industrial manufacturing is one of Germany's most important and long-established economic sectors. It comprises a large number of industries, including the automotive industry, mechanical engineering, electrical engineering, chemicals, pharmaceuticals, metal processing and many more. The largest sub-sector is the automotive industry with a turnover of around 440 billion euros. German car manufacturers such as Volkswagen, BMW and Daimler are global leaders and stand for innovative vehicle technology, quality and reliability. The automotive industry is also very important for the supplier industry, which provides a wide range of components and services for vehicle manufacturing. With a turnover of around 260 billion euros, mechanical engineering is the second most important sub-sector. German machines and systems are in demand around the world due to their precision, quality and durability. The sector includes companies that manufacture tool machinery, industrial robots, automation systems, food processing equipment and many other products. The country's entire industrial manufacturing sector generates a gross value added of around 750 billion euros per year and employs around 8 million people. Germany is one of the world's largest exporters of industrial goods. The export ratio in industrial manufacturing is around 48 per cent. Motor vehicles and parts are the most important export goods and account for a total of around 15 per cent of German exports (worth around 1.6 billion).
The coronavirus pandemic has had a major impact on manufacturing worldwide. The need for automation and robotics in in the manufacturing sector increased dramatically due to social distancing. Remote working, digital networking and safety optimisation in the workplace have increased. The disruption to the flow and supply of goods due to border closures, lockdowns and other coronavirus measures led to the need for measures to optimise supply chains.
There are many major challenges for the German industrial production sector. These include demographic change and the shortage of skilled labour, the implementation of Industry 4.0 technologies and the need to create sustainable production processes. Nevertheless, industrial manufacturing remains an important driver for the German economy and is of enormous importance for jobs, exports and innovation. The future belongs to so-called agile production systems that rely on iterative, incremental and collaborative approaches. This allows companies to react quickly to changes while ensuring high levels of quality and customer satisfaction.
Trends in industrial manufacturing
Industry standard 4.0 is accelerating digital transformation and automation
Digital transformation and automation as well as machine and system connectivity in production settings are receiving an enormous boost from Industry 4.0 technologies. Production processes are also being connected with all other areas of a company, such as logistics. Data exchange opens up many new possibilities, such as big data analysis using artificial intelligence (AI).
In the smart factory, it is possible to quickly convert production and individualise production down to batch size 1. At the same time, the increasing number of variants and varying article quantities must be handled by flexible warehousing.
The entire smart factory already exists as a digital twin before it is built. It can be used to simulate production processes and production planning.
Shorter development times and product life cycles require flexible and dynamic logistics systems. Intelligent manufacturing only makes sense in connection with "lean production" and "lean logistics". However, Kanban systems and just-in-time (JIT) delivery may need to be reviewed in the light of experiences made during the pandemic.
Machines and systems are monitored by AI-controlled predictive maintenance, with machine parts being replaced as required. Downtimes in industrial production are thus avoided.
Demand-orientated production:
The demand for certain goods is predicted by AI. As a result, only the required amount of goods is produced.
Process automation in production and the use of robotics continue to increase. Robots are used for a wide range of industrial tasks, from assembly and packaging to quality control. The use of collaborative robots (cobots), which can work safely alongside humans, has also become increasingly widespread.
3D printing and additive manufacturing are becoming increasingly important in industrial production. These technologies enable the production of high-precision, complex components and prototypes while reducing production times and costs.
Sustainability and environmental awareness are becoming increasingly important in the manufacturing industry. The companies are working towards adopting more environmentally friendly industrial production processes, using renewable energies, recycling materials and reducing the consumption of energy and resources. Nearsourcing, multisourcing and multishoring are changing industrial procurement.
With increasing networking and the use of IoT technologies, the importance of cyber security in manufacturing is growing. Companies must protect their production facilities and data from cyber attacks and implement effective security measures.
Reliable and intelligent storage systems with barcodes and RFID integrate seamlessly into material flows.
What are the requirements for logistics?
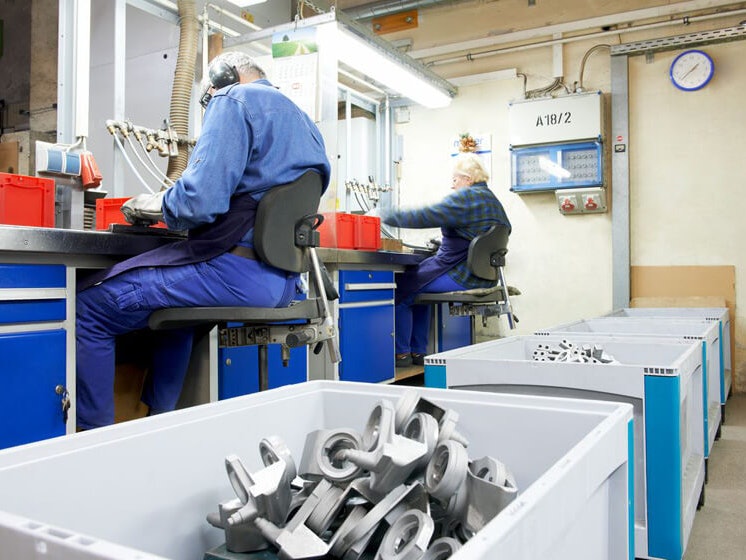
Intelligent production requires lean and smart logistics systems as a part of the Logistics 4.0 transformation. Logistics 4.0 aims to improve efficiency, transparency and flexibility in the supply chain. By using technologies such as the Internet of Things, AI, machine learning, big data analysis and robotics, companies can collect, analyse and use real-time data about their supply chains to make informed decisions and optimise their operations. Logistics 4.0 is leading to new technological solutions and new business models in logistics. Examples include predictive maintenance, improving supply chain visibility, optimising supply chains via AI and the use of autonomous drones and delivery vehicles on the last mile. By utilising IoT sensors and RFID technology, companies can track and manage their stock levels in real time. This enables them to optimise inventory levels through AI, avoid bottlenecks and implement more efficient and intelligent warehousing processes. Kanban systems and JIT delivery will continue to determine industrial production, albeit in a different form. Supply chains can be made more resilient, for example, by broadening the supplier base across different countries. Having a larger buffer stock also is a way of ensuring greater security of supply with components and semi-finished products. However, this conflicts with a strict JIT philosophy.
The BITO range includes Kanban shelving and bins such as C-item containers, which combine the advantages of handling bins and open fronted storage bins, and Euro containers in modular sizes. Of course, all bins and containers can be marked with barcodes or RFID tags. The mobile pallet racking systems BITO PROmobile and PROmobile synchro are particularly suitable when storage space needs to be utilised to the maximum and access to all references must be guaranteed. They are particularly useful for a wide range of goods and for batch size 1 production. Other applications and scenarios include changing product ranges or seasonal fluctuations in manufacturing and production settings. The driverless bin and container transport system LEO locative from BITO is particularly attractive for use in automated processes due to its flexibility, plug-and-play installation, ease of use, low purchase costs and decentralised controls. The BITO LEO AGV eliminates a lot of unnecessary walking and reduces the strain on employees.
Of course, BITO offers many other storage solutions for industrial manufacturing environments, such as static and live storage shelving and racking systems, single-tier and multi-tier installations as well as bins and containers for storage, transport and order picking.