Facts & Challenges
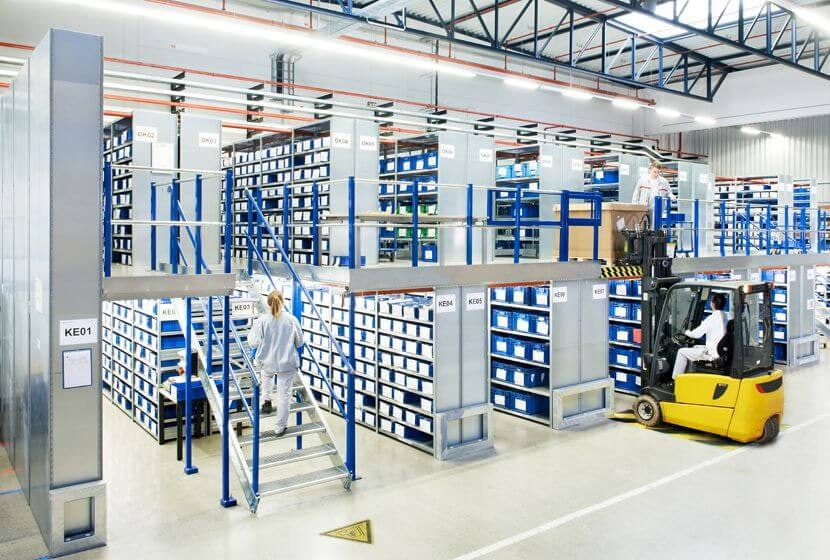
The global automotive industry is undergoing profound change. New concepts of mobility, autonomous driving, digitisation and electrification are creating significant pressure for transformation. Crises such as the pandemic and the Russia-Ukraine war are changing supply chains and causing companies to rethink their procurement and production strategies. For example, in Germany, climate change is forcing companies to operate sustainably and has brought about the Supply Chain Act, greenhouse gas reporting according to scopes 1-3 and a new CSR guideline for improved transparency in corporate sustainability reporting. According to the Federal Ministry for Economic Affairs and Climate Protection, the automotive industry is Germany's strongest industry in terms of employment. It provides jobs for around 2.2 million people in production, the supplier industry, the aftermarket (e.g. spare parts) and retail. The largest car manufacturers in the country are Volkswagen, Daimler AG and BMW.
The future of mobility
Transport transformation, i.e. the switch to more sustainable and environmentally friendly transport, affects not only companies in the automotive industry, but society as a whole. The increased use of electric and hybrid vehicles, the expansion of local public transport, cycle paths and footpaths as well as the promotion of car sharing and other forms of shared mobility are all on the agenda. Smart mobility not only affects the automotive industry, but also transport and urban planning as well as politics. The mobility transformation will probably be so far-reaching that new legislation for the automotive industry and internal company transformation will not be enough. Companies, politicians, trade unions and consumers must all pull together. In order to secure jobs and companies, a joint pact for the future must be concluded between manufacturers, suppliers, the federal and state governments and local authorities.
Connected and automated mobility
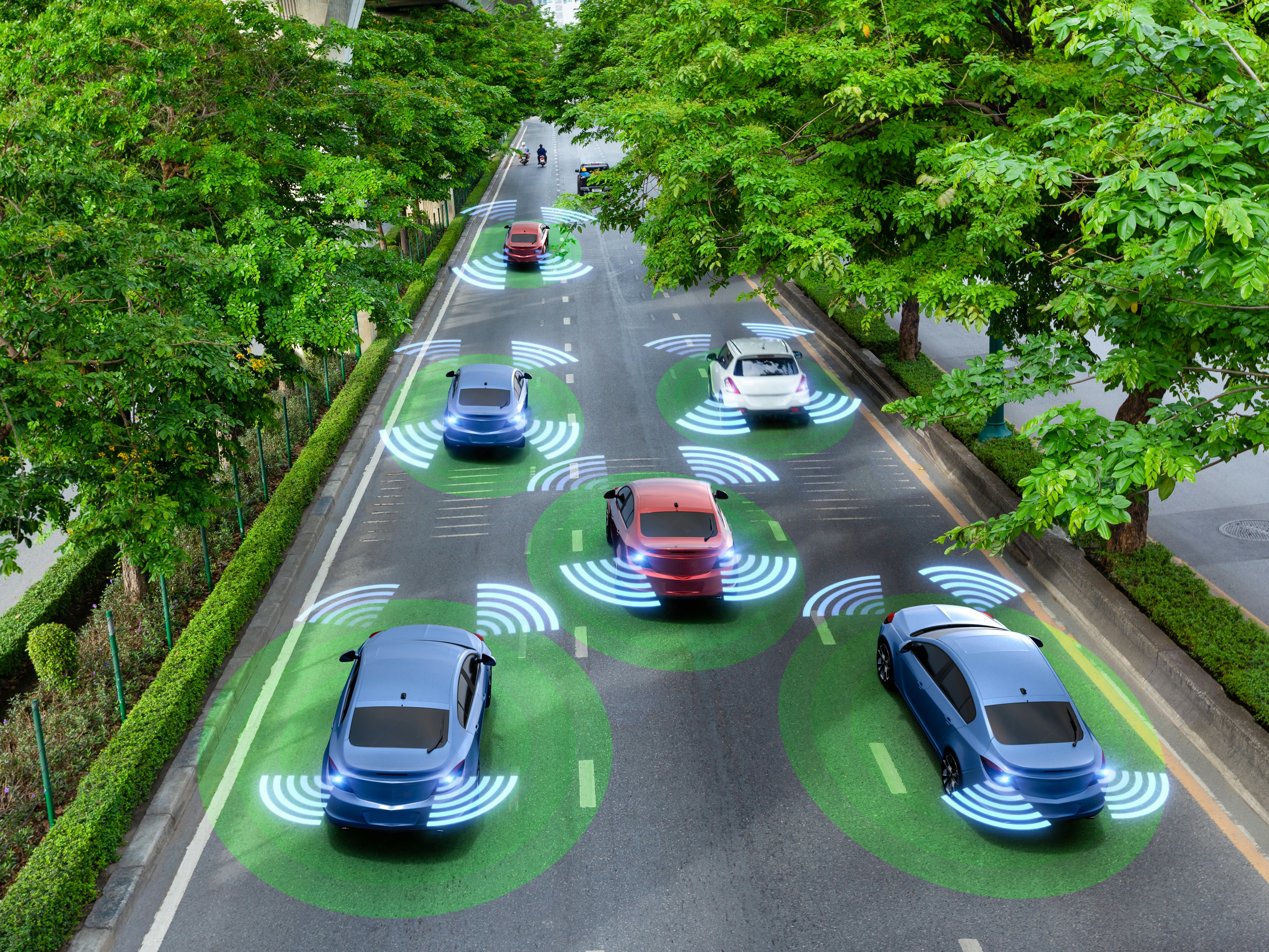
In the future, vehicles will not only move autonomously, but will be connected as well. According to the Fraunhofer Institute for Cognitive Systems (IKS), the development stages of autonomous driving include driver assistance systems, partial automation, high-level automation, full automation and autonomous driving. In Germany, only partially automated level 2 systems have been approved for cars to date. There are still many legal and technological hurdles to overcome in the development of all subsequent stages. From level 3, the systems must be able to monitor the driving environment independently and react to changes. Autonomous driving is not possible without artificial intelligence (AI). Self-driving cars and trucks use radar and lidar to monitor their surroundings in real time.
The systems receive further information from digital maps and GPS data. The vehicles also communicate with each other in order to take into account other vehicles' planned driving behaviour. All data is merged and evaluated by AI (machine perception). Based on this perception, a situational 3D model of the surroundings is created and predictions are made by AI. The AI plans actions such as activating the indicators and brakes and executes them independently.
It is difficult to make an exact prediction about when level 5 autonomous driving will be possible in Germany. There are still many technical, legal, regulatory and social hurdles that need to be overcome before completely autonomous driving can become a reality. Another problem is data security and the prevention of cyber attacks.
In general, autonomous driving has the potential to increase road safety by reducing human error. It can also make traffic more efficient by making better use of road capacity and reducing traffic congestion. The technology can be used, for example, in cabs, buses, private vehicles, vehicles in production and warehouses, trucks in industry or for convoys transporting goods.
Digitisation
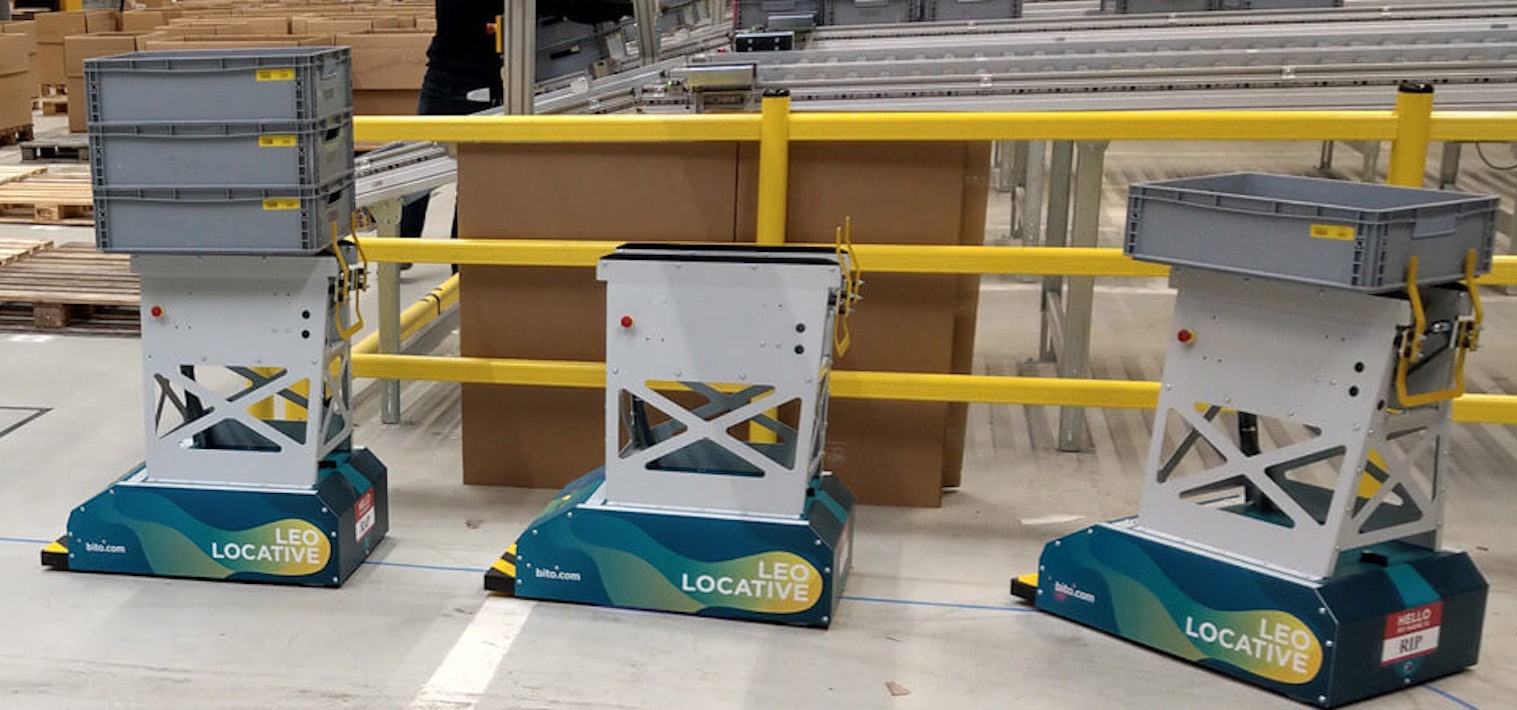
The digital transformation in the automotive industry plays a pioneering role, if only because of the size of the industry. Industry 4.0 technologies, and along with them digitisation, automation and connectivity, have increased significantly in recent years. In the future, vehicles will be manufactured in "smart factories" in which all components such as machines, robots and sensors are connected and exchange data. This enables a very high degree of flexibility as well as a high level of quality and efficiency in production.
In a smart factory, production processes can be changed over quickly and even highly customised vehicle types can be manufactured. Smart factories use AI and machine learning to make complex decisions and optimise production. However, digital technologies can be used in almost all areas of the automotive industry, e.g. in manufacturing, along the entire supply chain through to sales and, of course, in the vehicles themselves (see above). Digital technologies are also increasingly being used in sales and marketing to better reach and support customers.
This includes online sales and reservation systems as well as digital platforms for exchanging knowledge and experience between customers and manufacturers. Blockchain technology will also play an important role in the automotive industry. It can be used for secure payment transactions in vehicles, data protection, decentralised carpooling and proof of vehicle ownership.
Electromobility and alternative energy sources
Electromobility encompasses different types of vehicles, including battery electric vehicles (BEVs), which are powered solely by a battery, plug-in hybrid vehicles (PHEVs), which can be powered by both the battery and an internal combustion engine, and fuel cell vehicles, which run on hydrogen and emit only water. The energy used to charge the batteries can come from fossil or from renewable sources, which makes a difference in the environmental footprint of vehicles. The automotive industry is currently focussing on the development and production of climate-friendly fuels, more efficient energy storage systems and batteries, and alternative drive concepts such as fuel cells.
Supply chain diversification
The crises of recent years have made companies and consumers painfully aware of how fragile supply chains are. The pandemic and the Russia-Ukraine war caused supply chains to break down and severely disrupted the flow of goods. In many places, goods could not be delivered at all. In the automotive and computer industries, there was a serious chip shortage, which led to production downtime, delays, price increases and changes in model ranges. Companies, not only in the automotive industry, responded by diversifying their supply chains and adapting their purchasing strategies.
In particular, the resilience of supply chains can be increased through so-called “multisourcing” and “multishoring”. In multisourcing, parts and components are purchased from more than one supplier, some of whom are competitors. If the supplier base is spread across many countries, this is referred to as multishoring. The pandemic in particular has shown the strong dependence on Chinese suppliers, which is now to be reduced. In this field too, digital technologies enable significant improvement by creating efficient, global supplier platforms and networks as well as by implementing targeted supply chain management.
Trends that will shape mobility transformation
Many new mobility concepts are emerging: These include electromobility, and also the expansion of local public transport, bike paths and footpaths as well as the promotion of car-sharing and other forms of shared mobility.
New energy sources and improved energy storage:
Development of climate-friendly energy sources and fuels as well as more efficient energy storage systems (hydrogen fuel cells, supercapacitors, molten salt batteries).
Digitisation and AI are being used in all fields:
AI processes big data and optimises all processes in the smart factory, in autonomous driving, in supply chains, in warehouses, in sales and in marketing.
Smart Factory and new flexible manufacturing:
Thanks to the digital factory, the finished car is configured in detail before it goes into production and the necessary production steps are planned appropriately. The result is an optimised production plan that can significantly reduce production time. This development will have a major impact on logistics and intralogistics for both manufacturers and suppliers.
- Making custom products and many different variants is possible in the smart factory with Industry 4.0 technologies.
- Medium-sized companies in particular are preparing for digital production with lean production processes and fully automated intralogistics.
- Digitisation and increasing cost pressure are leading to the implementation of excellent logistics systems and optimised processes across the globe.
- New providers, some of them Chinese, such as Polestar, Lucid Motors, NIO and Byton are entering the market and intensifying innovation pressure in R&D.
- Climate change and CO₂ restrictions and taxes will be a major challenge to the automotive industry. Examples include diesel driving bans and CO₂ taxation which require new technical solutions.
- Autonomous driving: AD has the potential to increase road safety by reducing human error. Traffic can be made more efficient as vehicles can communicate with each other. One major problem is the risk of cyber attacks.
- Diversification of supply chains, adapted procurement strategies such as multisourcing and multishoring, digital supplier platforms and optimisation through AI are shaping supply chains.
What are the requirements for logistics?
There are indicators that the COVID-19 pandemic has changed or will change the way the automotive industry works. While just-in-time (JIT) production has long been a common practice in the automotive industry, the pandemic has exposed some weaknesses in this approach and prompted companies to consider alternative production methods. Disruptions in the supply chains caused a bottleneck for parts and components, which had a massive impact on vehicle production. Car manufacturers such as Toyota have started to reorganise their production. In doing so, car manufacturers are focussing on local suppliers and the local production of parts and components. Alternative storage options and larger stock holdings are also being considered.
Buffer storage is thus experiencing a renaissance in the automotive industry, which was previously dominated by JIT.
In addition, manufacturing processes are becoming more digitised and hence more efficient. Automation and connectivity via the Internet of Things (IoT) also speed up manufacturing processes (smart factory). This means that logistics and intralogistics must be integrated seamlessly and, in particular, without delay. This is why especially medium-sized companies are preparing for this trend with lean production processes and by fully automating their intralogistics processes. High-bay warehouses and automated small parts warehouses (AS/RS systems) serviced by storage and retrieval machines or shuttle systems, automated guided vehicles (AGVs), tugger trains, flow racking and Kanban racking, powered conveyor systems etc. are the means of choice in this case.
Custom automotive load carriers are also often used and integrated into storage systems. This is why it is extremely important for companies to work with an experienced warehouse technology specialist such as BITO, a one-stop shop for intralogistics solutions ranging from load carriers over AGVs to shelving and racking systems.