BorgWarner
BITO Carton live storage enables optimal use of space and continuous product supply for assembly lines
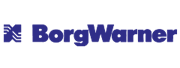
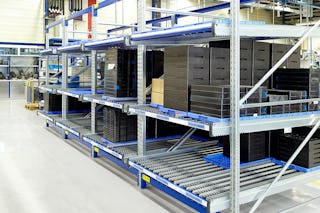
Our customer
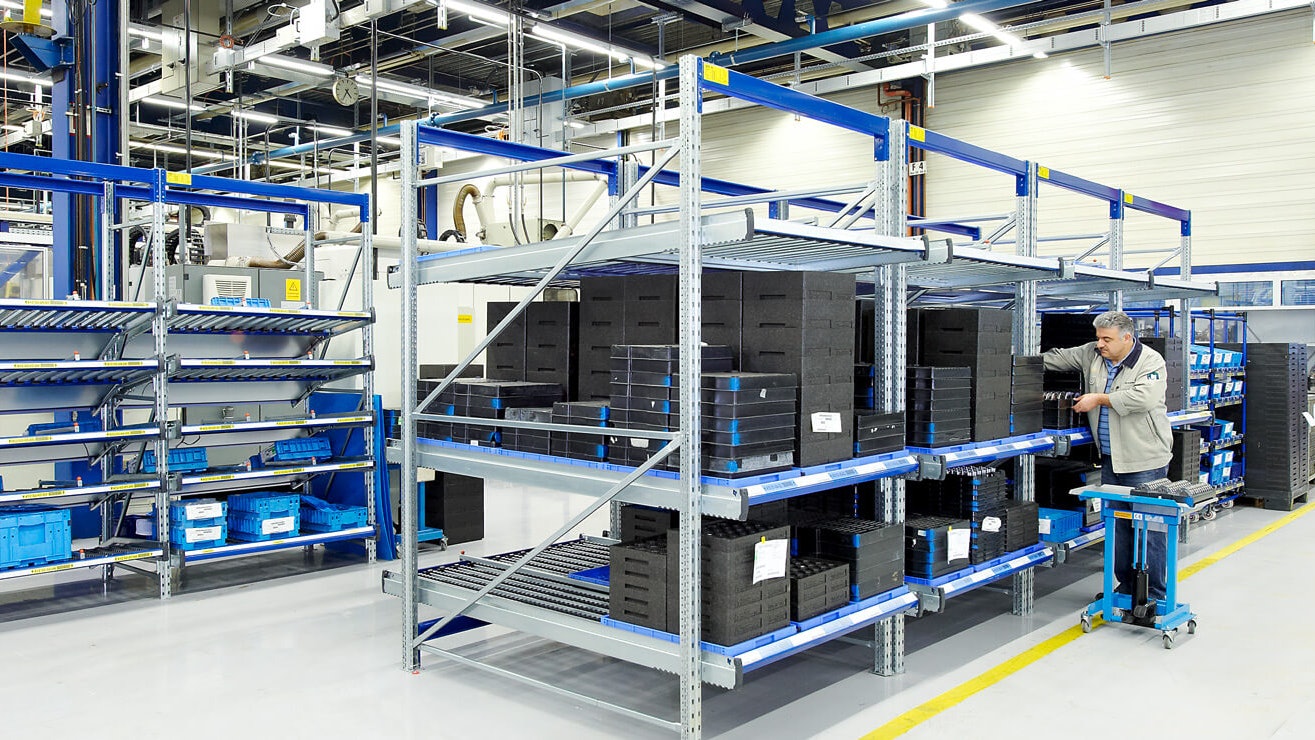
BorgWarner Turbo Systems is a leading global supplier of innovative charging systems and a competent partner to the automotive industry. In the power range of 20-1000 kW engine output per exhaust gas turbocharger, BorgWarner offers a wide range of turbochargers for passenger cars and commercial vehicles as well as for industrial, locomotive and marine engines. The company is headquartered in Kirchheimbolanden where the charging systems are assembled in two plants.
Initial situation and customer requirements
- Unit loads of different sizes and weights are to be stored on the same flow shelf level.
- All parts must be clearly arranged and it must be possible to adapt flow shelf spacing to load dimensions and shape.
- Trays stacked several high need to be stored on each level.
Some impressions of our customer solution
Project brief
The BITO Solution
BITO Carton live storage FLEX
» The automotive supplier opted for BITO carton flow racks.
Brake rollers
» The flow shelves for heavy loads are equipped with brake rollers to ensure that products move at an even speed to the picking side.
Stackable BITO trays
» Sturdy plastic trays provide a safe seat for individual parts and components.
On-site application and key features of our storage solution
- The automotive supplier provides small parts in BITOBOX KLT containers stored in flow racks.
- The flow shelves for light-weight loads have been mounted with a stronger gradient.
- Parts and components needed for the same assembly unit are stored on the same flow level. In order to store heavy loads on the same storage level as the lightweight load carriers, the flow levels have been equipped with brake rollers to slow down travel speed to the pick face and prevent potential dropping.
Customer benefits
In what way has the BITO solution helped our customer to realise their full potential?
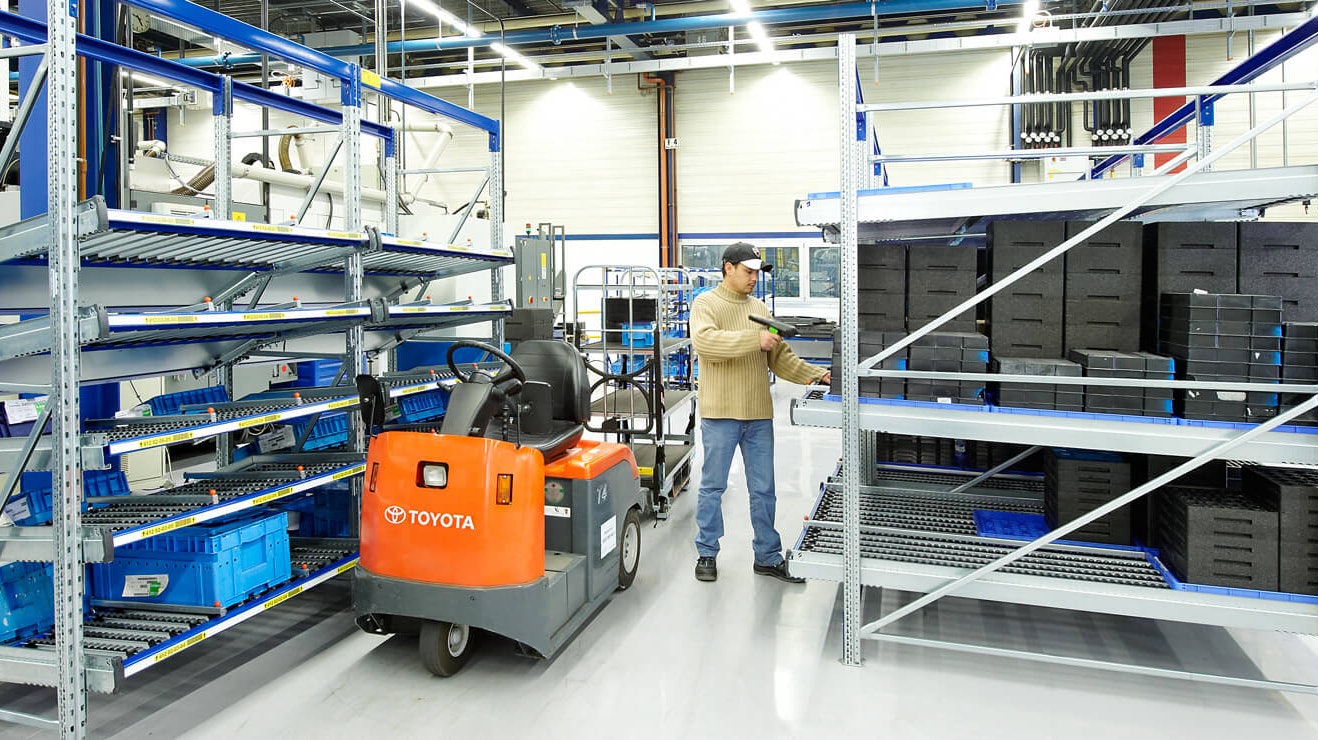
- The FIFO solution ensures constant product availability at the picking face on any one level.
- Optimum use of storage space with stackable trays.
- All required assembly parts are stored in a tidy and organised way thanks to the system’s high degree of flexibility and configurability.