What is intralogistics?
Intralogistics is typically defined as the organisation, control, implementation and optimisation of material flows, information flows and goods handling within a company.
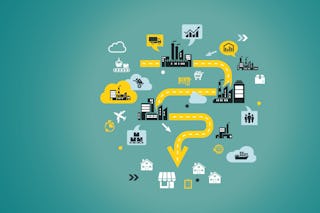
Brief introduction to the term intralogistics
An examination of the term "intralogistics" reveals a lot about its meaning. "Intra" stands for „within“, in this context it refers to internal company processes. By definition, "logistics" ensures that the right goods are available in the right quantity and quality, at the right place and time, for the right customer and at the right cost. Logistics encompasses the management and control of information and material flows that extend beyond the boundaries of the company itself. It refers not only to internal processes, but also extends to external processes such as transport and goods traffic outside the company. A succinct definition of intralogistics is "the organisation, control, implementation and optimisation of internal material and information flows as well as the handling of goods in industry, trade and public institutions".
Why is efficient material flow control so important?
In logistics, material flow includes the entire process of physically moving goods and materials along the supply chain, from the purchase of raw materials to the delivery of finished products to the end customer. This process includes transport, storage, handling and all associated activities. By definition, an efficient material flow ensures that the required quantities of material are available at the desired location at the right time. Efficient material flow processes are crucial for optimising logistics and production processes, reducing costs and increasing supply chain performance. Control technology, the exchange of information and the various types of conveyor technology are essential components in the control of the technical, economic and organisational transport of goods. Intralogistics goes beyond material flow control and also includes areas such as warehouse management, order compilation, packaging processes, internal transport and the coordination of materials and products within a company.
What areas can intralogistics be divided into?
The internal logistics of a company can be divided into the areas of "internal material transport", "inventory management" and "warehousing". It includes all processes from goods receipt to warehousing, internal transport and order processing through to goods issue. The areas of goods receipt, warehouse and administration, order compilation, packaging and goods issue can be derived from this.
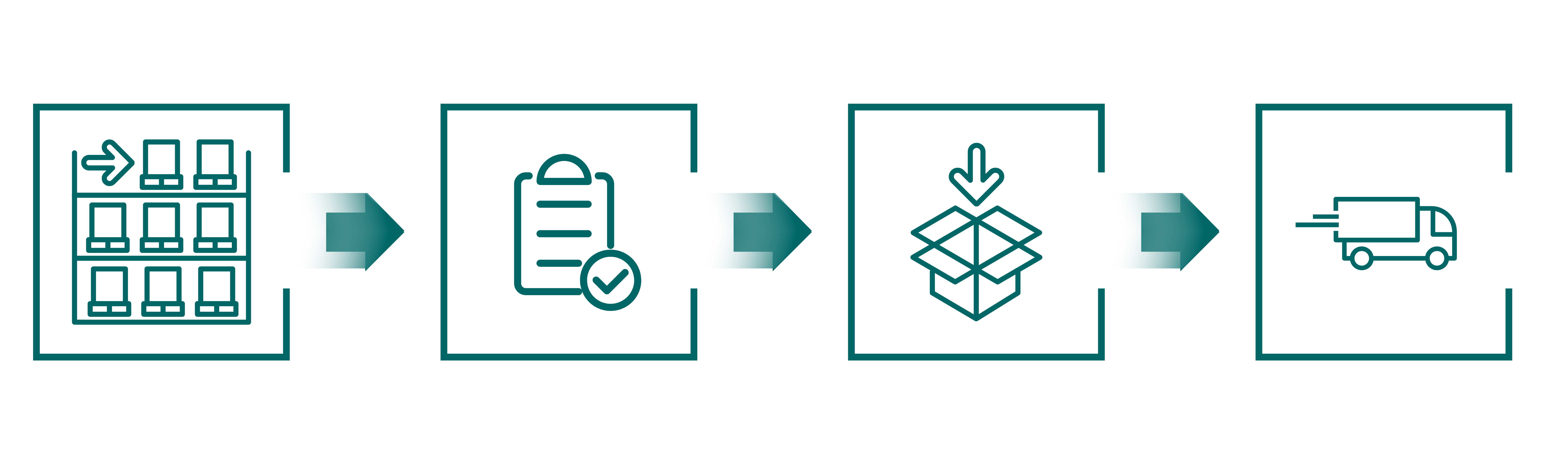
Which systems are used?
A wide variety of solutions for the intelligent planning, control, handling and monitoring of all processes in the areas of material and information flow are used in a company's internal logistics. Advanced sensor technologies and a high-performance warehouse management system (WMS) are essential for the needs-based, efficient control of all system components used in the areas of storage, order picking, conveyor technology and distribution. This system is in constant communication with the merchandise management system, continuously improves processes and issues precise transport instructions to the underlying material flow system.
Material flow system
A material flow system is made up of physical components such as the warehouse and conveyor technology and software such as the WMS or WMS and the material flow computer (MFR). The MFR software acts as the central interface in automated warehouse systems by controlling the data and information flows and thus establishing a connection between the warehouse technology and the WMS.
LVS and WMS
In logistics, the terms WMS and WMS are often used interchangeably, although they fulfil different functions and tasks by definition. The WMS focuses on the management of warehouse stocks, i.e. product quantities and storage locations, and can therefore be regarded as an inventory management system. It can also include elements such as the control of transport systems. In contrast, a WMS is far more comprehensive and complex. It maps the entire internal material and information flow of a company. The WMS receives orders from higher-level systems such as Enterprise Resource Planning (ERP) or a merchandise management system, manages them in a database and, after optimisation, forwards them to the connected transport systems for control. A WMS controls, monitors and improves complex warehouse and distribution systems. It contains the basic functions of a WMS and also offers a wide range of additional functions, including sophisticated methods for system status monitoring and various operating and optimisation strategies. In summary, the WMS is used to manage and optimise internal warehouse processes. Modern WMSs have a modular structure and can be expanded as required. They consist of core functions such as incoming goods, internal warehouse processes and outgoing goods, which are essential for warehouse operations, as well as additional functions such as cross-docking, dock and yard management, hazardous goods and hazardous materials management, resource planning, returns management and forklift control systems, which are implemented according to customer requirements.
Storage technology
Storage technology comprises various racking systems, including high-bay racking, archive racking, drive-in racking, pallet racking, cantilever racking, flow racking and shelving. This is supplemented by systems for internal material transport, which can be divided into two main categories: Continuous conveyors and discontinuous conveyors. Continuous conveyors include roller conveyors and belt conveyors, while non-continuous conveyors include forklift trucks, automated guided vehicles (AGVs), loading systems and platform trucks. Fleet management systems and identification systems are also used in the warehouse, which help to increase transport safety. Furthermore, automatic stapling and strapping machines as well as various devices for measuring, counting and weighing are standard equipment in warehouse environments.
Fleet management systems
Fleet management systems play a major role in optimising the management, planning, control and monitoring of vehicle fleets (including forklift trucks and other industrial trucks). They combine sophisticated hardware components such as on-board computers on vehicles, software for data analysis and performance monitoring, and communication technologies for real-time data transmission. Fleet management systems perform a variety of tasks, such as monitoring vehicle locations and conditions, analysing vehicle usage to increase efficiency, managing maintenance schedules to ensure vehicle availability, managing safety to reduce accidents and injuries, and optimising routes and schedules to increase productivity.
Order picking systems
Different types of order picking systems are used when compiling orders. By definition, a distinction is made between manual systems that work either according to the goods-to-man principle (dynamic) or the man-to-goods principle (static). Another innovative and adaptable solution in intralogistics is the automation of order picking using picking robots. These robots consist of a mobile base, a rotating lifting column with a gripper system and an integrated, travelling shelf. In addition, modern paperless picking methods such as pick-by-light and pick-by-voice are also used.
Cyber-physical systems
In the age of Industry 4.0, flexible, intelligent cyber-physical systems are increasingly being used in the digitalisation and automation of production and warehouse processes. These systems integrate information and software technology elements with mechanical components. Data is transferred and exchanged as well as monitored and controlled in real time via the Industrial Internet of Things (IIoT), which enables seamless and efficient networking and coordination of processes. In intralogistics, they ensure efficient control and monitoring of material flows. With their help, processes can be adapted and optimised in real time. Predictive maintenance can be carried out in order to avoid breakdowns. This makes intralogistics smarter, faster and more reliable.
Increasing automation and digitalisation
In view of Industry 4.0, global competitive pressure and the rapid developments in the field of e-commerce, automation or at least partial automation of operational processes is becoming increasingly important. Companies are faced with the complex decision of which processes they can or should automate. Is it perhaps even advantageous in some cases to retain certain manual processes in the warehouse? Particular attention must be paid to the integration of interfaces between automated and manual solutions. In particular, areas such as goods transport within the warehouse, picking and order allocation as well as efficient route planning, which is usually regulated by a warehouse management system, are well suited to automation measures. It is crucial for companies that their automation solutions are both flexible and scalable to meet changing market demands and business growth. For many companies, partial automation can be advantageous from an economic point of view. Large-scale, highly technical complete solutions are often not optimal for cost reasons and because of the risk of losing flexibility. With partial automation, investments are focussed on those areas that offer the greatest economic added value through automation. This leads to cost-efficient implementation and short amortisation periods. Areas that have less economic potential, are subject to strong fluctuations in workload or are affected by unforeseeable external influences are not taken into account. When introducing partial automation, it is advisable to develop a long-term, holistic concept, even if only a few specific areas are automated initially.
With BITO, you can automate your warehouse processes in stages or introduce a fully automated warehouse system, such as an automated small parts warehouse (AS/RS) or an automated pallet warehouse. One example of BITO's flexibility and cost efficiency is the AGV LEO, which automates container transport between different work and picking stations without the need for a master computer or WLAN.
Intralogistics solutions from the experts
As an expert in warehouse technology, BITO is the ideal partner for intralogistics, especially in areas such as warehouse design, racking systems, order picking technology, conveyor systems, storage and storage solutions, transport containers, rack protection and securing systems as well as automated guided vehicles (LEO Transporter). Thanks to its many years of extensive experience in almost all sectors, BITO can supply effective storage solutions for various industries. We specialise in the optimisation of existing processes. In view of the complexity of warehouse technology, a customised consultation is recommended in order to develop an ideal and efficient warehouse solution.