Warehouse order picking
Every day, customers order goods online or offline that need to be retrieved from the warehouse and made ready for shipment by order pickers to fulfil the order. The items to pick are transmitted in the form of paper or electronic pick lists to the corresponding picker.
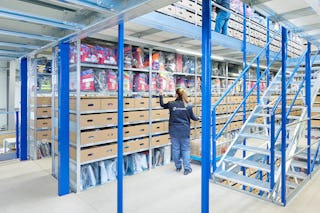
Every day, customers order goods online or offline that need to be retrieved from the warehouse and made ready for shipment by order pickers to fulfil the order. The items to pick are transmitted in the form of paper or electronic pick lists to the corresponding picker.
The nature of the goods and the warehouse determine the type of order picking
The type of warehouse or goods determine the type of picking to use. The FIFO (First In, First Out) procedure means that the goods stored first are picked first and removed from storage. This means that newly arrived goods are stored at the rear and the goods to be retrieved first are stored at the front of the racking. The FEFO (First Expired, First Out) procedure is used when a product has a best-before date and must therefore be picked first. If a longer storage period has no influence on the quality of the goods, such as metal products or certain bulk materials the LIFO (Last In First Out) principle is applied.
Two picking methods
1. Goods-to-man picking
With Goods-to-man picking the goods are brought directly to the order picker by means of conveyor technology. The order picker then accepts the goods at the picking station and removes the quantity specified by the warehouse management system. The empty containers or containers filled with residual quantities are then transported back to the warehouse using the same conveyor.
Advantages:
- High picking performance due to reduced travel times
- Wide range of articles possible
- Low error rate
- Containers are transported back easily and automatically.
Disadvantages:
- Relatively high investment costs for automated shelving and retrieval systems
- Less flexibility due to fixed number of picking stations
- If the machine fails, the process may come to a standstill.
- No flexibility for the order picker with fluctuating requirements.
Examples of goods to man picking equipment include: carousels, vertical storage racks, tower racking, automatic picking storage system, flow racking with automatic conveyors and high-bay racking with automatic rack conveyors.
2. Man-to-goods picking
With Man-to-goods picking the order picker goes to the storage location and removes the required goods. This type of picking is therefore particularly suitable for smaller orders and goods of low weight. If multi-stage picking is used (see below), this picking method can also be operated economically in large distribution centres.
Advantages:
- Low investment costs necessary
- High picking performance with optimized picking routes possible.
Disadvantages:
- Increased effort during the withdrawal of goods
- Longer walking distances and travel times
- Difficult ergonomic workplace design.
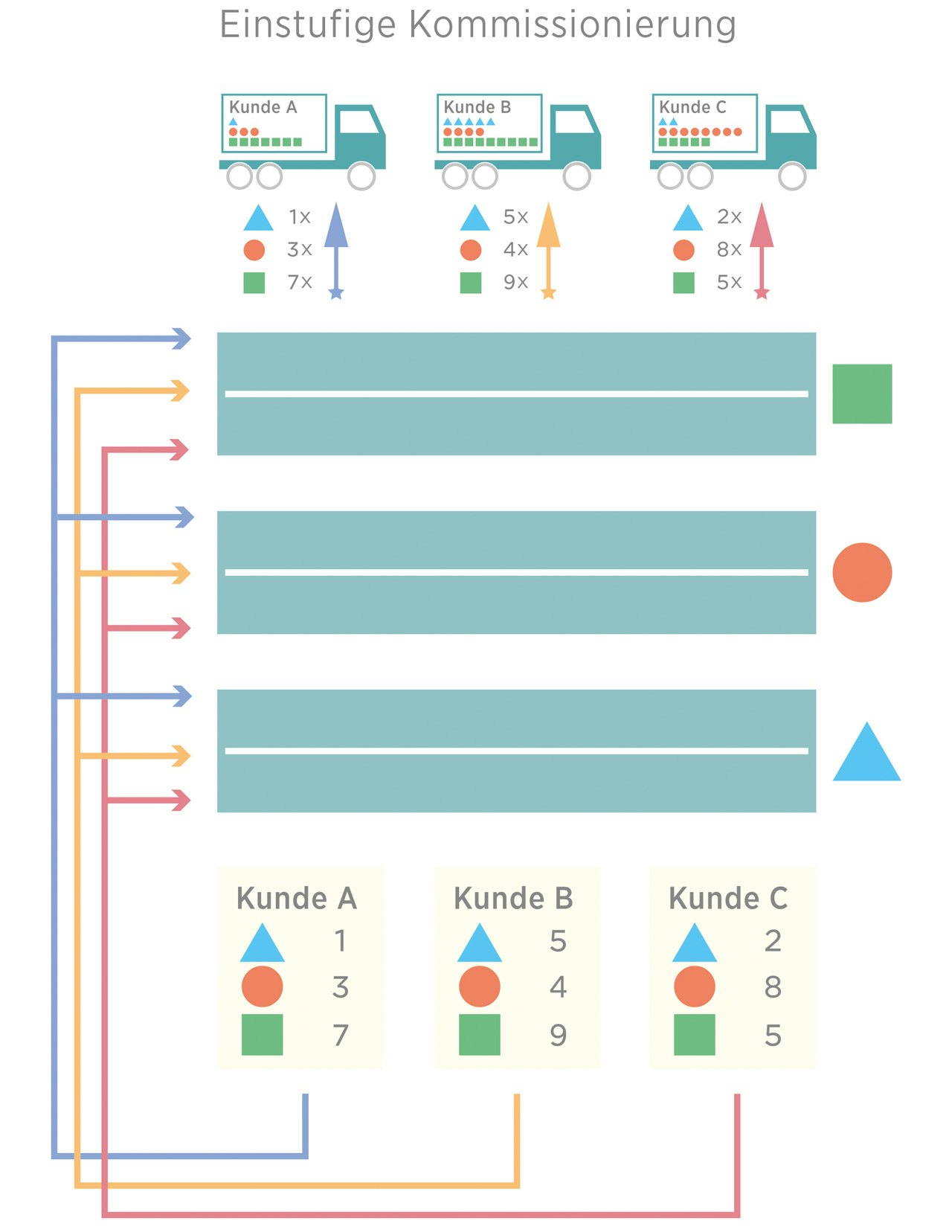
Single stage picking
With single stage picking, each customer order is compiled individually. Order-oriented parallel and order-oriented serial picking are used as picking methods. With parallel picking, an order is divided into different picking zones and processed simultaneously. Larger orders are divided and processed in different storage zones at the same time. As soon as all partial orders have been completed, they are consolidated again at a collection point to form the respective complete order. This leads to a saving of distances and a shorter processing time of the orders. However, a consolidation unit is required to combine the part orders. The entire process must be coordinated and controlled by a warehouse management system.
In serial picking, the items in the order are processed successively. Either an order picker passes through all warehouse zones or an order is transferred from one order picker of a certain zone to the next order picker and his zone – in a relay run – until all order positions are completed. The distances travelled are relatively small, as a picker moves in small picking zones. Since the order is not split but passed on, no consolidation is necessary. The disadvantage is that the orders have to be temporarily stored at the transfer points. This can also result in an unequal supply of order pickers with orders.
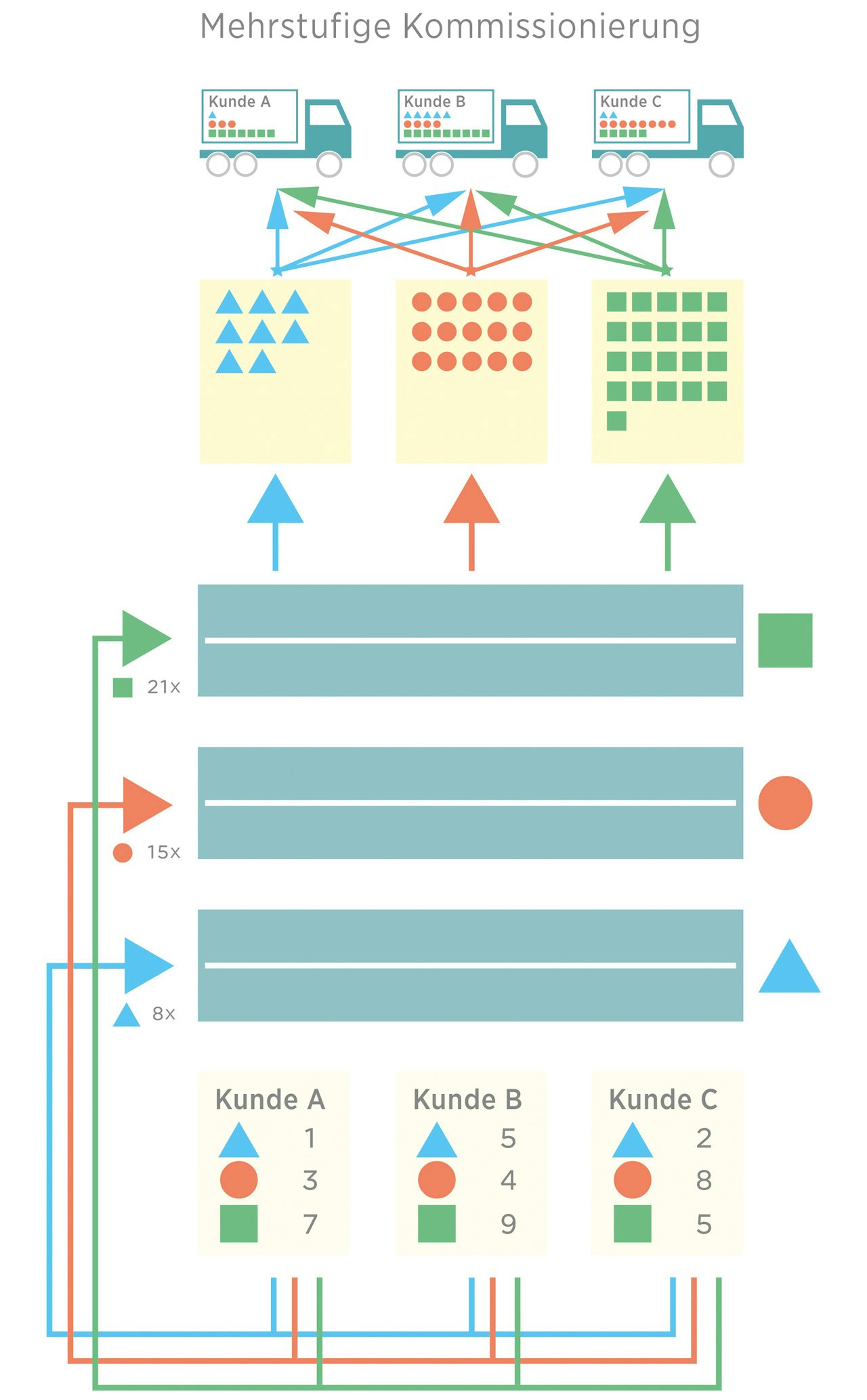
Two- stage or multi stage picking
With two-step picking, the entire quantity of an article can be picked simultaneously or in parallel for a large number of orders. The number of times a picking route and an article are accessed is drastically reduced (in the best case to just once). Several orders are bundled to a total order, then picked based on articles and packed later based on orders. The use of downstream sorting – using either a fully automatic or manual sorter – allows a far-reaching decoupling from the order reference during order picking. Two-stage picking is also called series-oriented, parallel picking. A major advantage is that the container frequencies in the individual storage areas are greatly reduced and the performance limits of the conveyor technology are less exploited. Two-step picking is suitable for operations such as mail order or pharmaceutical wholesalers.
Picking procedures
Pick-by-Light
Pick-by-light is an optical, paperless picking procedure. Easy-to-read lights, located directly at the storage location, indicate where the next unit is to be picked. A display additionally indicates the number of units that has to be picked. After picking, the order picker confirms the process by pressing a button, and the signal disappears. Pick-by-Light is used for high picking speeds with low error rates.
Pick-by-Voice
Pick-by-voice is a voice-supported, paperless picking procedure. The order picker can keep his hands free and concentrate undisturbed on picking. The Warehouse Management System (WMS) transmits the orders via a voice client and reports them directly back to the WMS after acknowledgement. No time-consuming searching is required, error rates are reduced and picking performance increases.
Pick-by-Terminal
Pick-by-terminal sees data transmitted by radio to a terminal permanently installed on the industrial truck. Companies that predominantly trade large and bulky goods use this picking procedure. Since the terminal is operated intuitively, there is no need for time-consuming teaching-in of order pickers. The error rate is very low, but language barriers of employees can become sources of error.
Pick-by-MDE / Pick-by-Scan
Pick-by-mde / Pick-by-scan involves employees moving through the warehouse with mobile or forklift terminals for mobile data collection. The picking list is displayed directly to the employees on the respective PDC (Portable Data Capture) unit. The removed articles are confirmed on the device and also missing quantities or zero quantities can be entered. The current status of the picking process can be tracked in the WMS. Advantages include shorter search times and fewer picking errors. Disadvantages are a relatively high initial investment and it does not allow for hands-free picking.
To learn more about warehouse planning, picking, picking methods and systems, please contact us at bito.com. We offer comprehensive advice and a wide range of storage options and services.