Kaizen: committed to continuous improvement
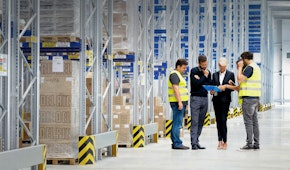
Behind the Japanese term "Kaizen" stands a philosophy that can be applied in many areas of life but also to industrial processes. Kaizen means "continuos improvement" and encompasses a mindset or philosophy of life that is geared towards continuous and infinite optimisation or change. The changes and improvements to the processes and products in the production logistics are carried out step by step and selectively. The origins of Kaizen can be traced back to the 50s, when the post-war Japan was lying on the ground. At that time, Toyota had to find a solution to a trade union dispute which resulted in the involvement of all remaining employees in a continuous optimisation process. The guarantee of lifelong employment meant that human capital had to be extremely profitable. It made sense to continuously improve the skills of the workers and to make effective use of their knowledge, experience and work performance. Toyota introduced Kaizen among many other principles like Kanban, Just-In-Time (JIT) delivery of components, Kenbutsu (supplier involvement), etc. to the Toyota Production System (TPS) in automotive manufacturing. According to the well-known Toyota engineer and production manager Taiichi Ohno, the starting point of the TPS concept is the elimination of any waste. He also defined the seven types of waste. Although Taiichi Ohno's book "Toyota Production System: Beyond Large-Scale Production" was translated into English in the 1980s, Kaizen first became widely known in the West through the Japanese management consultant Masaaki Imai and his book "Kaizen: Japanese spirit of improvement". In principle, Lean Production and Lean Management were already applied at this time. Subsequently, the concept was adopted in the Western economy and further developed into a management system known in practice as the Continuous Improvement Process (CIP).
Basics of the Kaizen method
Kaizen is a way of thinking that is internalized by all employees and realized in all processes of a company. The five central foundations of Kaizen are: Process orientation, customer orientation, quality orientation, criticism orientation and standardization.
By moving away from pure result orientation towards process orientation and profit optimisation through the constant optimisation of processes, customer orientation is inevitable. Because profit optimization is only possible with high customer satisfaction, since customer acquisition is more expensive than customer connection. However, there are external and internal customers (branch offices, organizational and production units). Problems often arise at the interface between these organizational units, which is why the main focus here is on implementing the optimizations and goals of Kaizen - quality assurance and increase, customer satisfaction and cost reduction by the employees. Within the framework of Total Quality Management, a permanent Total Quality Control is carried out, in which the quality is permanently monitored during production in an elaborate measuring procedure. This is not easy for many people to accept, but criticism is seen in Kaizen as an opportunity for continuous improvement. However, not only criticism, but also suggestions for improvement should be made to the management. Proposals will be reviewed and evaluated for usability and, if possible, implemented. It results in a continuous cycle of planning, operation, control and improvement, the PDCA cycle (Plan → Do → Check → Act). A suitable improvement shall be set as a standard. However, this standard is still being reviewed for improvements.
Tools and Methods
There are many tools and methods in Kaizen that can make the causes of all kinds of mistakes and wastes in the company visible. They show where and how improvements can be made. Their application is relatively simple, but nevertheless, through the continuous use of all employees, major changes can be achieved. Some examples are: 5S/ 5A, Kaizen workshops to discuss suggestions for improvement, 3-Mu checklist, 6-W checklist, Ishikawa diagram for root cause analysis, 5-Why questions, Gemba-Walks, Kanban, Poka Yoke, and many more.
5-Why-Why Questions
This is a questioning technique to explore the root of the challenge. According to Kaizen philosophy, it should be applied first to determine the challenge. One asks, for example, "Why did this happen?", whereby the respective answer forms the basis for the next question. Not all challenges have a single underlying cause. Therefore, a different sequence of 5-W questions may have to be asked for each cause. The result always depends on the knowledge and perseverance of the questioning persons involved.
Example:
Challenge: The forklift truck does not start.
- Why? The battery's dead.
- Why? The alternator doesn't work.
- Why? The fan belt's torn.
- Why? The fan belt was already old and was not changed.
- Why? The forklift wasn't properly serviced. (root cause)
5S/ 5A
In the 5S/5A method, the employee analyses his working environment for waste and unnecessary activities and initiates appropriate actions to eliminate them. These all start with an "S" in Japanese.
- Seiri: Remove unnecessary items from your workspace.
- Seiton: Order the things that remained after Seiri.
- Keep your workplace clean.
- Seiketsu: Make cleanliness and order your personal concern.
- Shitsuke: Make 5S a habit by setting standards.
Kaizen Workshops
All employees in a work area meet regularly with their superiors to discuss what problems have arisen and what measures should be taken to improve them. Workplaces, work areas and the situation "on site" are examined, things are viewed and analysed live. If possible, improvements are implemented and tried out directly. Topics for the meeting can be, for example:
- operational processes, duplication of work, unnecessary activities
- Quality problems and faults in products, tools or machines
- faulty work center organization
- Delay in individual activities and processes
- Rationalizations that make processes simpler or faster
- and much more
In order to be able to directly implement and test improvements from Kaizen workshops, it is helpful to work with technologies and tools that the employees themselves can optimize for their needs. A BITO example: With the driverless transport system "LEO Locative", employees can set or "program" their own lanes or commands until they are optimally adapted to their requirements. Employees do not need external IT support, do not need to obtain quotes or request a budget, which allows them to adapt flexibly to all circumstances.
3-Mu Checklist
With the checklist sources of waste and causes of problems can be uncovered.
- Muda: Waste
- Muri: Overload
- Mura: Deviation from standards or rules
In the three areas, for example, the following things are checked: Employees, technology, methods, time, creative scope, devices and tools, material, production volume, transports, circulation, space, movement sequences (ergonomics), way of thinking (mindset).
Seven types of waste (mudas)
- overproduction
- waiting time
- unnecessary transport
- Manufacture of defective parts
- excessive storage
- unnecessary movement
- unfavorable manufacturing process
Goals and advantages for intra- and production logistics
In principle, Kaizen can be applied to any area and process. In industrial processes, the main objective is to optimise profits by avoiding waste (see seven types of waste), which is achieved through process, customer, quality, criticism and standardisation - while at the same time constantly optimising these areas. As the example of the Kaizen workshop at LEO Locative showed, employees are given more leeway to optimize processes in small steps even according to their requirements in the sense of Kaizen. This creates a greater sense of responsibility and satisfaction among the employees and therefore increased motivation and efficiency. Solution proposals from the workforce can and should also be rewarded in order to further increase motivation. The continuous application of simple rules to improve processes in all sectors creates tangible changes. This also means that one does not wait for the perfect solution, but prefers simple but effective solutions. All employees and departments are always involved in Kaizen. Problems here are opportunities or challenges and are seen as the driving force of the improvement process. A concrete example of Kaizen in intralogistics is the continuous optimization of transport routes in the warehouse. The answer to many questions can be found in the direct working environment. The creativity and intelligence of all Kaizen employees is explicitly used and often not even a large amount of capital is required for implementation. The philosophy also shows that no process is ever fully optimized. The next small optimization step appears directly after the just completed one.