Avoid interruptions in the warehouse
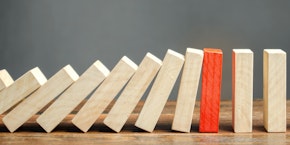
When processes in the warehouse are interrupted, it not only costs time but also has a knock on effect leading to delays in subsequent procedures, such as dispatch of articles and delivery to customers. If, for example, a company is a just-in-time supplier to the automotive industry, it faces a risk of high contractual penalties if production dependent on deliveries comes to a standstill. If customers are supplied too late, trust and customer loyalty suffer. Avoiding interruptions in warehouse operations and downtimes is therefor a crucial factor when it comes to warehouse process optimisation.
A distinction can generally be made between planned and unplanned interruptions. Planned interruptions in the warehouse include, for example, stoppages due to inventory or due to maintenance of machines, systems and racks. Causes of unplanned stoppages include machine damage, Warehouse Management System (WMS) failure, downtime in upstream production or even accidents and employee sick leave.
Planned interruptions
Planned and delay-free warehouse inventory
Stocktaking on the Balance Sheet Date should always be well planned, prepared and carried out in a time-saving or efficient manner. It may be necessary for the entire company to work in advance to create a time buffer and resilience against process interruptions. Rework may be necessary. It generally tends to be small things that cause unnecessary delays and interruptions to processes on Inventory Day. Of course, sufficient personnel – employees as well as possibly temporary workers – to handle the physical inventory must be planned for first. Before stocktaking takes place, it must be clarified whether it can be carried out during ongoing or reduced operations, or whether the business will need to be shut down. How much time is the inventory expected to take and when exactly should it take place? The inventory areas should be prepared – this means tidying up the warehouse and sales area, stocks must be compiled and ordered, damaged goods must be placed separately, correct labelling must be checked, etc. In addition, necessary information, such as stock and item lists, must be prepared and made available. The use of inventory checklists is also a good idea. Recording and checking must be preformed at least four hours before the start of the main inventory. As soon as the task is completed, the receiving areas must be locked or goods secured against removal.
Maintaining a permanent inventory using a WMS is also recommended. It is the best way to keep meticulous stock accounts and corresponding records.
Carry out maintenance work
Maintenance for racking systems, forklifts, automatic conveyor technology, automatic small parts storage, etc. should be carried out at least once a year.
Dates for different aspects of maintenance work in the warehouse should be planned and distributed over the year so that processes and workflows are interrupted as little as possible. For example, one truck from the company's own fleet can be serviced each month or the maintenance of all trucks can be concentrated together on a weekend, during a holiday period. In this case, the loss of performance can be compensated for by additional scheduled equipment. Additionally required equipment, such as forklifts, can be rented from a service provider. Of course, the personnel planning in the warehouse must also be adjusted accordingly.
Unplanned disruptions to warehouse operations
Failure of machinery, plant and equipment
The failure of machinery and equipment can cost a lot of time and money. Anticipating failures allows an operation to react to them efficiently through appropriately pre-planned emergency procedures.
It is also advisable to design in redundancy for continuity of operations. Take the example of a failing stacker crane in an aisle of an automated warehouse. To ensure that goods can still be accessed in an emergency, it is advisable to distribute important articles to several different storage aisles. This will avert a standstill in order picking and customer delivery. In another example, equipping narrow-aisle warehouses with an inductive guide, rather than a rail guide, means that in the event of a forklift failure, floor pallets can still be accessed with a hand pallet truck.
It is certainly advantageous to prevent breakdowns and downtimes through maintenance measures, machine service (fluid management, maintenance work, etc.) and industrial cleaning.
Redundancy for critical hardware and software components of a WMS is a crucial requirement due to the complexity of the system and the serious consequences of a failure. The redundancy concept also applies to conveyor components.
Prevention of production interruptions
Having appropriate safety stocks of vital items in a warehouse will avoid disruption of service levels. This is the only way to ensure that order picking and customer deliveries can continue without interruption. In addition, preventing standstills in production processes requires stocking the appropriate semi-finished products, components, auxiliary materials and lubricants required for maintenance.
Averting delivery delays
Delivery delays by suppliers can be catastrophic for companies. This is why continuous supplier control and the identification of alternative suppliers is a good idea.
It is possible for entire supply chains can collapse, as was demonstrated during the Corona crisis. The heavy dependence on suppliers from China led to supply bottlenecks and standstills in many production and trading operations. In the future, work on supply chain resilience will therefore be intensified and steps will include finding alternative suppliers in other countries. Delivery delays have been particularly catastrophic for just-in-time production in the automotive industry, which in many cases saw production come to an immediate standstill. A rethink of the entire production principle or system may even be required.
Prevent employee absenteeism
In the event of employees being absent due to illness or accidents, it may be possible to resort to temporary employment agencies to avoid interruptions in warehouse processes.
It is of course important that companies take accident prevention seriously. In every company there are areas that must be secured against access by unauthorised persons. Furthermore, there are many danger spots that must be completely separated by barriers. Accident prevention and the elimination of hazardous areas are the responsibility of the company owner. When it comes to occupational health and safety, the employer is primarily responsible for preventing harm to life and limb of his employees. Basic obligations are therefore imposed on employers by law.
Avoiding interruptions during order picking
Constantly maintaining a sufficient safety stock of items will prevent interruptions during order picking. However, excessively large storage areas and stocks are costly disadvantages that should be avoided. Safety stocks must therefore be determined precisely. It is also advantageous to organise picking efficiently so that the process runs smoothly. Supplier control and the identification of alternative suppliers are also important. Furthermore, the loss of employees must be prevented.
Optimisation of warehousing
For efficient warehousing and to avoid interruptions and errors, standardised processes are required. These might include uniform labelling of storage locations and transport units as well as the use of a WMS. The following ten approaches are particularly suitable:
Eliminate information breaks in warehousing processes.
Lean warehouse processes – from goods receipt, to order picking, to goods issue.
Reduce the search effort through standardised labelling and shorten path/grabbing times.
Introduce efficient control mechanisms in the outgoing goods department.
Minimise inventory discrepancies and prevent misloads.
Increase stock accuracy.
Prevent out-of-stock situations and increase the quality of goods provision.
Uncover energy-saving potential.
Optimise the use of floor vehicles.
Reduce communication effort by switching to Electronic Data Interchange (EDI), and possibly introduce WMS.
Literatur:
1 Inventur: So gelingt Ihnen die Bestandsaufnahme mit minimalem Aufwand, Haufe-Lexware GmbH & Co. KG, Link
2 Bito Fachwissen, Vorschriften zur Lagereinrichtung, Link
3 Sicher und gesund durch Absperrungen von Gefahrenbereichen, Bito, Link
4 Bito Fachwissen, 10 Fehler, die Sie beim Kommissionieren vermeiden sollten, Link
5 Herausforderung effizientes Lagermanagement, Mittelstand 4.0-Kompetenzzentrum eStandards, Link