10 tips for efficient hall construction
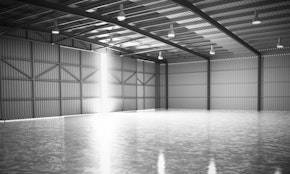
Topics overview:
- Individuality as a benchmark for successful construction projects
- Precise coordination promotes the efficiency of hall construction
- Making the right use of financial resources
- Well planned from head to toe
- Designing logistics halls correctly
- Keeping sustainability in mind at all times
- IT in hall construction
Individuality as a benchmark for successful construction projects
In order to design the construction of a hall quickly, cost-effectively and as efficiently as possible, it is important to know that a hall makes different demands on the construction depending on the intended use. So it depends on a wide variety of things that influence the efficiency of a hall construction. Therefore, you must first clearly define which type of use your hall should have. Whether warehouse, hazardous materials hall or production hall, sales hall, logistics hall or exhibition hall - they should all fulfil a specific purpose and do so as efficiently as possible.
Depending on the type of hall you have chosen, various regulations must be observed for hall construction, which in turn are directly related to the type of use. For example, a logistics hall must have enough space to manoeuvre the means of transport, while a market hall must meet special fire protection regulations due to its later public traffic. While the logistics hall is about getting the logistics department and floor conveyor technology on board the planning boat right at the start of construction, the market hall is more about function, design and prestige going hand in hand. Or is your hall a deep-freeze warehouse? Then you should already make sure before the start of construction that you can guarantee an uninterrupted cold chain, a high storage density as well as energy efficiency and short throughput times later on.
Precise coordination promotes the efficiency of hall construction
The use of the hall is therefore decisive for hall construction from the very first planning second. In a second step, this is accompanied by the expected size of the building. This depends to a large extent on the purpose of the hall. In order not to have a financial disadvantage later due to too much or too little space, it is important that you consider in advance how much space you will need. This is also connected with another tip that you should take into account, especially for the construction of a warehouse or logistics hall: What is stored? Depending on the stowed goods, the area of a hall can be determined even more precisely, which in turn leads to the best possible use of costs.
Also important: the traffic routes that should exist in your hall. Will there be many means of transport and a large floor conveyor system? Do you store pallets with large goods or do you erect shelves with many small cartons? Questions such as these should absolutely be included in the planning for an efficient hall construction in advance in order to be able to create the best possible concept for the traffic routes within the hall. The decision as to how much space you need for the logistical processes within your hall should therefore be made at the very beginning of hall construction.
Making the right use of financial resources
Hall equals cost trap? It may be, but it doesn't have to be. Because if the financial planning is detailed and realistic right from the start, there is no unpleasant surprise in the end. Be sure to include a reserve of around 30 percent of the construction sum. You should also always consider which construction method best suits the requirements of your hall and what financial resources you will have to spend on it. If the cost factor is very important to you, it is a good idea to choose a system or lightweight hall. In terms of hall construction, these are considerably cheaper than, for example, a concrete or steel hall. But here, too, you should always keep an eye on the end product so that there are no conflicts between the building fabric and the use of the hall.
The same applies to the coordination between the individual departments of a company. For efficient hall construction, it is crucial to involve all departments that will later operate within the hall in the planning from the outset. This is the only way to achieve a result in which everyone can work together optimally.
Well planned from head to toe
As different as halls are and how they are used, so are the options for designing their roofs. Another tip is therefore to think about the roof design at an early stage. This should not only be dense and weather-resistant, but at the same time also meet some design criteria. Especially market halls, exhibition halls or production halls can provide a lot of comfort by choosing the right roof. And this benefits the (working) atmosphere in the entire hall at the end of the day. For this reason, roof planning should play a decisive role in hall construction.
Another important factor when planning the hall construction is the consideration of the floor. Especially when a hall is later to serve as a warehouse or logistics hall, it must be clear in advance which shelves will be used. Some shelving units, such as heavy-duty shelving units, require special anchoring in the floor. It is therefore advisable in any case to adjust the screed thicknesses and concrete thicknesses at an early stage to the anchoring regulations of the respective shelves. Also check whether the building site is located in an earthquake or subsidence region and what preventive measures you can take to protect your hall.
Designing logistics halls correctly
Special requirements apply to each hall. Be it fire protection, occupational safety or regulations for hazardous substances, they all have to be taken into account in hall construction. Therefore, you should consider the relevant regulations for your hall at an early stage. What can happen if planning is inadequate and what massive financial losses can result have already been impressively demonstrated by many major projects in the past: the Hamburg Elbphilharmonie, Berlin's BER Airport or the expansion of the A8 motorway near Munich. Such a thing does not have to be and can be avoided by a good planning.
Apropos good planning - this also includes the early involvement of specialist consultants from intralogistics and warehouse technology in hall construction. They are experts for all internal material and goods flows and know exactly how a hall must be constructed in order to enable efficient, fast and profitable work. Regardless of whether goods are received, produced, stored or dispatched, they have all the knowledge you need to help you with efficient hall construction.
Keeping sustainability in mind at all times
Particularly in times of renewable energies, it is advisable to pay special attention to the building materials used in hall construction. Is a modern energy system based on photovoltaics a viable option? Or galvanized steel against corrosion? The possibilities of hall construction are manifold. Take advantage of this opportunity and invest in a building whose sustainability can pay off in the long term.
In this context you should also pay attention to the conditions of the property on which you want to build. The condition of the ground, location and surroundings can have a significant impact on hall construction and should therefore be taken into account in all planning. If you have all these factors in mind, avoid complications later on, such as the space required by the construction vehicles or the materials used.
IT in hall construction
The larger the area of your hall is, the more you should attach importance to continuous monitoring of storage areas and entrances and exits. Your cost planning for hall construction should therefore always include the installation of a professional IT system. In this way you protect your company against unauthorised entry, theft or the like - an investment that is worthwhile in any case. And even for automatic small parts warehouses, it is important to consider a sophisticated technology concept, since warehouses of this type are always fully automated. Only comprehensive planning in advance can ensure that you can keep up with Logistics 4.0 and guarantee smooth work.
What all 10 tips have in common is that they concentrate on the planning prior to hall construction. Lay the foundation stone for an efficient construction project from the use of which you can benefit in the long term. Therefore, invest enough time in the preparations and, if necessary, seek advice from a competent partner. He/She will visit you on site, support you in planning and accompany the entire construction project. This saves you unpleasant surprises during the construction phase.