BITO retrofitting solutions for static racking
BITO has decades of experience in the field of material storage and handling. We are also specialists in retrofitting existing static racking systems for live storage applicat
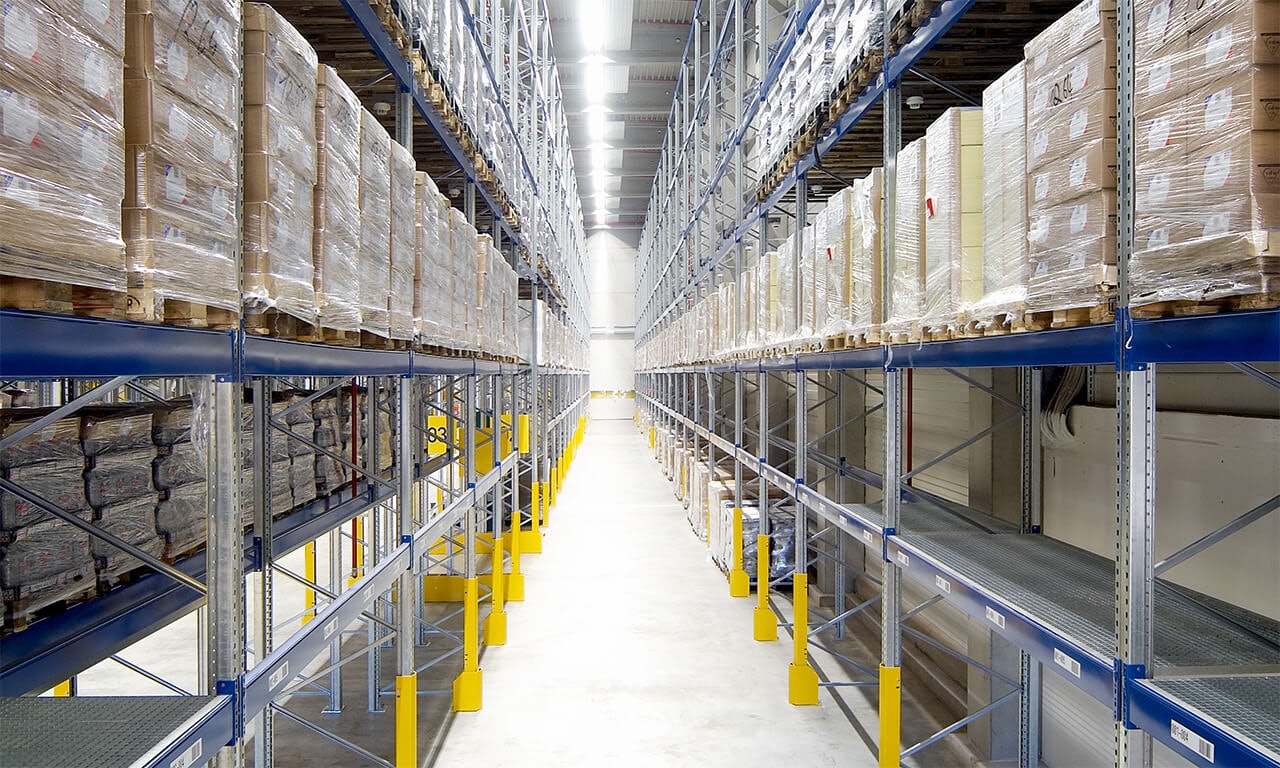
Retrofitting static pallet racking
Today's business and market conditions are subject to rapid and frequent change. Companies must be able to adapt their operational processes to these developments just as quickly. Not only processes need to be reviewed. Adapting storage and order picking equipment is also important. Retrofitting and converting existing racking installations is a way to be ahead of the game. Existing static pallet racking can be retro-fitted by adding carton live storage levels at operator reach height. Retrofitting is even possible for a limited period of time, for example for handling seasonal peaks. The racking can be re-converted afterwards. In this way, a company can quickly adapt to changing product ranges, varying product turnover rates and different pack sizes. This flexible approach helps to optimise the use of available resources and increase operational efficiency.
Upgrading storage systems and improving workflows
BITO also provides solutions for improving warehouse logistics Changing markets, products and customer demands often mean that existing systems do not meet modern requirements any more. Modernisation offers the opportunity to adapt intralogistics systems to new standards and make them more efficient and reliable. In most cases, the basic configuration of a warehouse is maintained, but with new organisational processes, operational performance and product availability can be improved. Many components may have reached the end of their service life and the availability of control systems and spare parts can be a problem. Even if mechanical and static components may not have reached the end of their service life, they often impair dynamic systems as well as control and information systems. Companies usually carry out modernisation measures in areas such as order picking, material storage and retrieval, IT and software. Modernisation can relate to an entire warehouse or only to certain areas. This process requires adjustments to meet current safety and productivity requirements. In some cases, modernisation can even make new buildings or extensions unnecessary, especially if the existing system still offers potential for optimisation. The focus is on control hardware, drive systems and sensor technology, including the software of storage and retrieval machines. BITO is at your side as an experienced partner to provide expert advice, project planning and implementation as well as a comprehensive after-sales service.
Retrofitting storage facilities is becoming increasingly popular
BITO can help convert your pallet racking into a high-performance order picking system and modernise your warehouse at the same time.
Intralogistics systems can be adapted to new requirements with professional modernisation measures
Changing markets, products and customer demands often make a system set-up less useful over the years. Modernisation offers the opportunity to adapt intralogistics systems to new requirements and make them more efficient and reliable. In most cases, the basic layout of a warehouse remains the same (storage areas, placement of conveyor and storage systems). However, by modernising individual elements and deploying new organisational processes, it is possible to increase performance and improve product availability. Retrofitting refers to the refurbishment and modernisation of older and mainly automated intralogistics and logistics systems. Many electronic and mechanical components have either reached the end of their service life, control systems are no longer manufactured or spare parts are no longer available. This harbours the risk that systems can no longer be maintained and may fail. While mechanical or static components and the steel structure have often not yet reached the end of their service life, failures frequently occur in dynamic systems as well as in control and information systems.
Modernising only a part of a system can be an option
Modernisation can either involve the entire warehouse or just certain areas. Companies most frequently carry out modernisation measures in order picking processes (such as the implementation of voice picking), goods storage and retrieval as well as in the areas of IT and software. Shipment tracking, coordination and cross-docking are also updated as a part of this process. Systems, components and processes must be modernised in line with current requirements in order to ensure adequate safety and optimum productivity. In some cases, warehouse modernisation can even avoid the need for new buildings or expanding warehouse capacity, especially if the existing facility offers sufficient potential for optimisation. Such modernisation measures often focus on the control hardware, drive systems and sensor technology, including the software of storage and retrieval machines.
What are the benefits of a BITO solution for modernising and retrofitting static pallet racking?
We set standards in the field of intralogistics
BITO has many years of expertise in the field of storage systems and warehouse equipment. We realise projects of any size and also deliver the required material storage and handling equipment. One of our particular strengths is to retrofit existing static racking systems. Using a combination of proven expertise and innovative solutions, we set standards when it comes to optimising warehousing systems. At BITO, we understand the special features of each warehouse and customise our solutions precisely to your requirements. Retrofitting static racking systems goes beyond simply increasing efficiency. It means integrating function and aesthetics into a storage environment.
We make your pallet racking more productive
BITO converts your pallet racking into a high-performance live storage system by integrating roller track flow levels. More and more customers are switching to online shipping directly from their warehouse and are looking for flexible and quick solutions for picking items directly from their pallet racking system. Rather than full pallets,, individual items are increasingly being shipped. BITO responds to this development by integrating carton live storage levels into existing pallet racking systems. The upper racking levels serve as buffer levels for replenishing the picking levels at operator reach height. Instead of one or two pallet storage levels on the floor, the racking system is now equipped with flow levels for smaller loads. Integrating and removing flow levels or adding more levels can be done very quickly, In a typical live storage system, products are fed in from the loading area at the rear of the racking and move on gravity-driven inclined roller tracks or roller beds to the picking side.
Have your warehouse modernised by a warehouse equipment specialist
We manage and implement warehouse modernisation projects of any size. If your warehouse processes or warehouse equipment are no longer fit for purpose, you should do something about it as soon as possible. Do not wait too long to modernise your warehouse because you may loose your competitive edge in a highly competitive market. BITO provides comprehensive advice and will be pleased to plan and implement the optimal solution together with you. As an allrounder in the field of material storage, we also provide general contracting services and offer our customers a holistic solution. Modernisation can include, for example, the areas of order picking, goods storage and retrieval, IT and software, or even require a comprehensive warehouse automation system.
Manufactured in our own facilities
At BITO, we manufacture premium shelving and racking systems as well as plastic bins, trays and containers in our own state-of-the-art production facilities. Our steel products are manufactured at our company headquarters in Meisenheim, BITO bins and containers are produced in Lauterecken. Both production sites work in compliance with the latest technological standards and use modern, energy-efficient machines. This not only guarantees the outstanding quality of our products, but also ensures that production is resource-efficient and meets the highest standards of technology and environmental compatibility.
Decades of expertise in warehouse logistics
Thanks to decades of experience in the development and implementation of solutions for almost any industry, BITO can draw on a wealth of expertise. As a specialist in storage technology, we go beyond simply manufacturing our own shelving and racking, plastic bins and containers and operating an extensive online shop for components and accessories. Our expertise also extends to designing and realising large warehouse projects and supplying the entire range of necessary equipment in the field of warehouse modernisation.
Easy and affordable first step into the world of automation with LEO
The LEO automated guided vehicle system from BITO enables the fully automated and flexible distribution of parts and semi-finished products to various assembly or picking stations. The LEO AGV safely transports totes, containers, trays or cartons and also automatically returns empty load carriers to their point of origin. The optically controlled transport system requires neither a master computer nor a WLAN connection. LEO navigates by means of colour-coded track tapes and receives precise driving commands through optical markers (QR codes) on the floor. LEO AGVs can be customised to your order picking application and are a simple and cost-effective way to introduce your company to the world of automation.
BITO Storage solutions grow with your business
BITO provides storage solutions that can be easily scaled and flexibly adapted to any industry. Many BITO shelving and racking series can be easily assembled without nuts and bolts and extended with add-on bays.
Using synergies to boost performance
Together with you, we will find the best solution for your warehouse automation project or for retrofitting your pallet racking into a live storage installation. At BITO, we value effective communication and comprehensive advice. Right from the start, we are on hand to advise you and realise the optimal solution for your needs. We are thoroughly convinced that outstanding solutions are created through intensive dialogue with our customers.