BITO automated small parts storage
Direct access and high pick rates
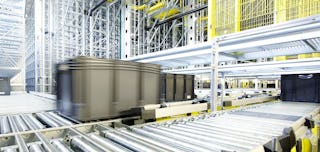
BITO Automated small parts storage
Fully automated, computer-controlled product supply of large product ranges with a lot of variety
An automated small parts warehouse or mini-load system typically comprises a racking system with one or more aisles, a storage and retrieval machine, conveyor technology, small parts containers for storing and transporting goods and control software that ensures continuous process organisation and a high level of availability of each item. Automated small parts storage systems have many advantages. Loading and unloading is fully automated following the "goods-to-person" principle based on FIFO or LIFO storage strategies. Automated storage offers fast, direct and permanent access to every item, usually from a broad range of products. The floor-to-ceiling design of an AS/RS system makes full use of the available ceiling height without expanding the footprint of the facility, thereby maximising storage capacity. At BITO, we manufacture shelving and racking as well as bins, containers and trays in our own plants with state-of-the-art machinery. Our customers can therefore buy the entire product package from a single-source. The interface to a modern inventory or warehouse management system (IMS or WMS) ensures permanent control of stock levels.
Serviced by stacker cranes or shuttle vehicles
In AS/RS systems, goods are handled with stacker cranes or shuttle carriers. Both handling systems have advantages and disadvantages. In miniload systems with stacker crane loading and retrieval, the racking construction, sensor technology and the control system are less complex than in miniload systems serviced with shuttle carriers. However, aisle-bound stacker cranes are less flexible than shuttle carriers. To increase the handling capacity of a shuttle-serviced warehouse, additional shuttle carriers can be used. This is particularly interesting in peak times. Shuttle-serviced storage systems not only enhance picking accuracy. They also guarantee the permanent functionality of the system. Shuttle vehicles can easily be exchanged if a shuttle breaks down, i.e. the storage system remains operative. Automated storage and retrieval systems achieve high throughput rates which can be further enhanced by increasing the number of shuttles, vertical conveyors and lifts. As already mentioned, rack construction and process control are much more complicated in shuttle-serviced systems as additional rails have to be laid and a complex control system with suitable, powerful algorithms has to be integrated. As flexible, high-performance storage systems for large product ranges are increasingly in demand, shuttle systems are likely to be implemented more frequently in the future.
Perpetual stocktaking has many advantages
As automated small parts warehouses are controlled by an inventory or warehouse management system (IMS or WMS), perpetual stocktaking is possible in real time. Real-time stocktaking continuously delivers information such as the location and currently available quantities of a particular product whereas manual stocktaking only provides data for a specific key date on which stocktaking was conducted. Permanent stocktaking usually minimises shortages in the company, which significantly improves the ability to deliver and increases customer satisfaction. As a result, customers are more likely to place repeat orders. In addition, permanent stocktaking also optimises logistics processes. Travel routes for product storage and retrieval can be planned more efficiently, order picking can be streamlined and the assignment of storage positions can be improved.
Advantages and benefits
Efficient storage
BITO products ensure optimum space utilisation.
Versatility
The modular design enables easy adaptation to individual requirements.
Top quality
BITO products are known for their durability and sturdiness.
Ergonomics
BITO products help to improve workplace ergonomics.
Safety
BITO products are safe and comply with all relevant safety standards.
Space-efficient solution
BITO products help to reduce the amount of storage space required.
Warehouse management system
BITO products help to improve warehouse operations and organisation.
Saving time and money
Maximising storage capacity will save you time and money.
Broad product range
BITO offers a large selection of products for a wide range of applications.
Customer support
BITO offers a comprehensive range of services from advice and planning to assembly and maintenance.
Maximum efficiency
Fully automated systems minimise the need for manual work.
Efficient order processing
Accurate order picking and effective small parts management
.Minimising error rates
The system prevents human error and maximises accuracy.