The importance of energy efficiency in warehouse logistics
Rising energy prices, increasingly scarce resources and stricter legal requirements present companies with the challenge of finding potential savings. This means that saving energy is also becoming increasingly important in warehousing and logistics. But how is it possible to increase energy efficiency and initiate sustainability in warehouse logistics?
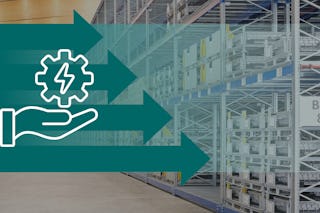
Energy consumption challenges in the logistics sector
Energy consumption in warehouses can be inherently very high. This results in high operating costs and CO₂ emissions. In order to achieve energy savings in warehousing, first identify the main consumers. These can include
- Continuous lighting
- Heating, ventilation and air conditioning systems
- Cooling systems in refrigerated and deep-freeze warehouses
- Electric vehicles for internal transport
- IT and communication systems (e.g. servers, computers)
As you cannot simply switch off the systems, it is important to reduce warehouse energy consumption and therefore costs by optimising energy efficiency. An important starting point is automation, which, in addition to improved energy efficiency, brings further benefits such as faster warehouse processes, higher productivity, better stock control and greater security.
Measures and technologies to increase energy efficiency and sustainability
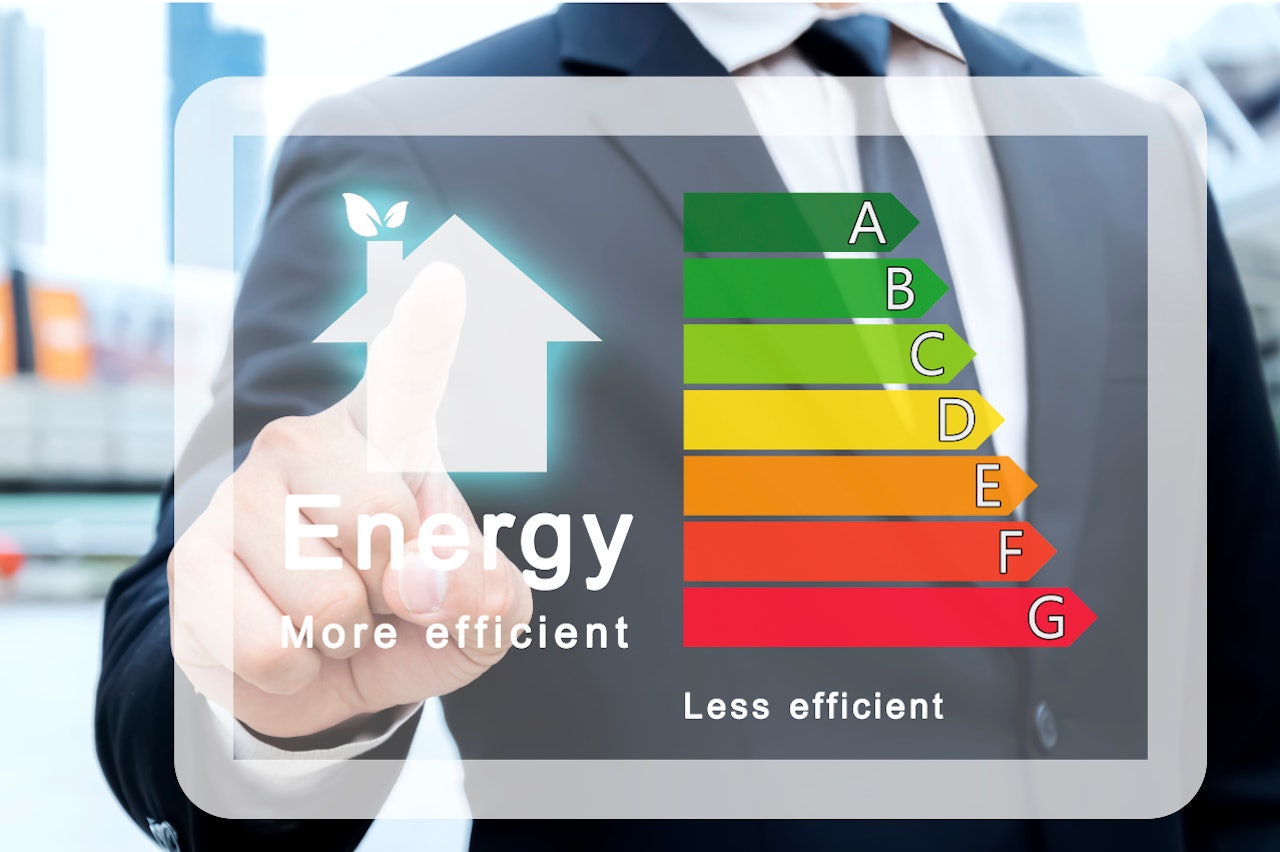
There are a wide variety of energy-efficient technologies for warehouses, so that suitable solutions can be found for every need. Energy consumption for lighting, for example, can be reduced by using LED light sources and motion sensors. Maintaining optimum climatic conditions can be made more sustainable and environmentally friendly by switching to more energy-efficient heating, ventilation and air conditioning systems and utilising heat recovery systems. When storing temperature-controlled products, modern cooling systems with better insulation reduce energy requirements.
If you charge your electric vehicles with mains power, then your own solar powered system could be a good solution. There are also energy-saving storage solutions for the IT sector, such as energy-efficient hardware and the integration of energy management software.
Optimising the energy efficiency of warehouse processes through automation
Fully automated warehouses only need to be heated or cooled when the goods require it. There is no need for lighting, as robots and similar devices can easily find their way around without light thanks to intelligent control systems. Of course, automation initially requires a high level of investment. However, the systems pay for themselves relatively quickly through the savings in energy costs.
Optimisation of warehouse processes for greater efficiency
Efficient warehouse processes reduce the consumption of energy and resources and make a significant contribution to cost control, sustainability, productivity and customer satisfaction. There are several ways to speed up warehouse processes and increase efficiency through targeted optimisation. The most important of these include
- Layout optimisation to reduce transport distances
- Automation of processes using the Internet of Things (IoT) and warehouse management systems
- Monitoring key performance indicators such as stock accuracy and order throughput figures to identify processes in the warehouse with optimisation potential
- Implementation of just-in-time principles to minimise stock levels, use storage space more efficiently and optimise warehouse processes
Automated warehouse processes are suitable for various areas. Incoming goods are recorded more quickly and accurately. This saves both time and space. In inventory management, automated systems help to optimise stock turnover and avoid excess stock. Autonomously operating conveyor belts and driverless transport systems contribute to a smooth material flow. Robots and pick-by-light systems speed up order picking while reducing the error rate.
Automating processes in the warehouse is not only important for energy efficiency. This form of warehouse optimisation also increases the agility and adaptability of warehouse operations allowing you to react more flexibly to market dynamics.
Sustainable logistics strategies to reduce costs
In addition to energy savings and increased flexibility, the development of sustainable strategies can also contribute to long-term cost reductions in the company. As every warehouse has different requirements, there are no universal solutions that work equally well everywhere. Ideas presented here can therefore only provide a rough guide to suggested savings.
In order to optimise your warehouse processes and reduce costs, it is necessary to analyse your existing processes and use this as a basis for planning how to reduce energy consumption. As a start, sustainable logistics can be achieved through the following measures.
Create storage space
Use compact storage and shelving systems to maximise storage space in the smallest possible area.
Optimise warehouse processes
By integrating warehouse processes with well thought through optimisation, you save time and reduce error rates.
Reduce energy consumption
Investing in the modernisation of the warehouse noticeably reduces operating costs and is guaranteed to pay off in the long term. The positive effects for staff well being are felt immediately.
Practical examples and best practices
Optimising warehouse processes to reduce energy consumption is worthwhile and various case studies show that energy-saving measures in warehouse logistics bring the desired success. Photovoltaic systems on warehouse roofs are the first steps towards sustainable warehouse management. However, there are also examples of concrete solutions in which BITO has played a decisive role.
With the support of BITO, the Pilsner Urquell brewery in Germany was able to triple its storage capacity from 700 to more than 2,000 pallets and reduce transport routes and costs by centralising its export warehouse. Instead of multiple external warehouses, there is now only one,which has reduced their overall energy requirement. The Schwälbchen dairy was another client who contacted BITO because they needed additional storage space for fresh products. With the help of mobile pallet racking, the storage capacity could be increased by 75 per cent while at the same time reducing energy costs.
Our customer projects provide many more examples of companies that have been able to make warehouse processes more efficient, energy-saving and cost-effective through clever optimisation. Best practices in this area include
- Maximising storage capacity with multi-tier racking systems and unit load flow systems
- Shorter picking routes and times thanks to conveyor technology and integrated buffer storage
- Optimisation of internal logistics with the help of AutoStore systems
- Reduction of storage areas to be cooled through optimised space utilisation
Outlook for the future: Trends in energy-efficient warehousing
It is already possible to achieve a great deal through adopting strategies for energy reduction in logistics. The development of new technologies will further improve energy efficiency in warehouses and logistics centres in the future. These are the most important trends:
More energy-efficient buildings
Modern insulation and energy-saving lighting and air conditioning systems will reduce the energy requirements and operating costs of storage rooms and warehouses.
Renewable energies
The increased integration of renewable energy from solar, wind and geothermal power plants will help to reduce CO₂ emissions and make warehouse operations more environmentally friendly and economical.
Artificial intelligence (AI) and automation
AI and automation make it possible to optimise processes such as sorting, picking and packing. Artificial intelligence can also help with predictive maintenance and the planning of transport routes. This reduces the risk of breakdowns and unexpected downtime, while optimised transport routes save time and transport costs.
Intelligent warehouse management systems (WMS)
AI-supported WMS can collect and analyse huge amounts of data from sensors, supply chains and other sources and provide you with valuable insights into the flow of goods. This simplifies the management of goods and commodities and gives you the ability to proactively respond to delays and bottlenecks. Some WMS can monitor energy consumption in real time, allowing you to identify inefficient processes and take targeted measures to save energy.
Networking of warehouses
Warehouse devices and sensors can be effectively networked via the Internet of Things to collect real-time data. You can use this data to make warehouse processes more energy-efficient through planned optimisation.
Other key strategies are
- Efficient space utilisation through multi-tier storage solutions or automated storage and conveyor systems
- Minimisation of movement through path optimisation
- Improve flexibility with an easily customisable warehouse layout that enables quick reactions to seasonal fluctuations or changes in stock levels
- Use of modern warehouse software that provides valuable insights into inventory data and supports you in optimising warehouse processes
Conclusion and recommendations for action
By optimising warehouse processes, companies can increase the energy efficiency of their warehouse logistics and achieve a sustainable reduction in costs without having to compromise on productivity, quality or customer satisfaction.
Even simple measures such as replacing conventional light bulbs with LED bulbs or installing motion sensors to automatically control the lighting help to reduce energy consumption. Intelligent heating or cooling, short distances, energy-efficient drives in conveyor technology and the increased use of renewable energies increase sustainability even further.
Making warehouse processes more energy and cost efficient through holistic optimisation is a complex task that requires careful planning. We are happy to support you with our technical expertise, so why not get in touch to see how we could help?