The Kanban Method in Production Logistics
Kanban is an ingenious method of decentralized production control, but it is not suitable for every application. Find out here whether it also suits your company.
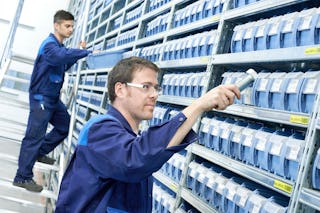
If you are interested in logistics, warehouse technology, the automotive industry or management, you have probably heard of Kanban before. But what exactly is Kanban? When is it used? Where are the advantages? If you are unsure whether Kanban is also suitable for your company, then this article should give you answers.
Decentralized production control with the Kanban system
Kanban is a method of decentralized production control in which data cards - called Kanban in Japanese - are used to trigger individual production processes and logistics processes. The Kanban method was introduced by Toyota manager Taiichi Ohno in the 1950s at Toyota plants. The actual idea came from the food industry or logistics, or more precisely from the supermarket sector. The advantages of the Kanban method are decentralized control, lean warehousing and just-in-time (JIT) logistics of parts needed in production. Important data such as article number, quantity, storage location, etc. are noted on the cards. The production sends a signal to the upstream production stage that new components are needed. For example, an empty container with an order card for a specific component is sent to the lean warehouse and a full container is taken back with it. The parts warehouse now knows that this item must be reordered in a certain quantity and sends this purchase order to the source (the supplier). The supplier completes the order and delivers the required quantity of the corresponding component to the lean warehouse. The kanban card therefore serves as an order card for production, which triggers a specific production order or resonance wave that runs from production to the vendor. In the second variant, the kanban card serves as an identification card for the new component to be produced or ordered. Two adjacent production stages are connected to form a control loop, which ensures problem-free coordination of the successive stages. For example, production stage A retrieves a component from the lean warehouse (buffer warehouse) and production stage B replenishes the parts warehouse with the corresponding component.
Push and pull principle
Decisive advantages of the method are the decentralized control and the self-control in combination with the pull-principle (hold-principle). Stock levels can be considerably reduced compared to the classic push principle (bringing principle). The Kanban system is significantly more robust and flexible than the classical method. With classic central production control, production is based on demand estimates. For this purpose, market and sales data shall be and based on this, forecasts are prepared. The parts warehouse holds many components in stock and triggers orders based on existing stock. Orders are placed on the basis of forecasts and at the same time a safety stock is maintained. The danger with push systems is a miscalculation. This can either lead to too much being calculated or to customer wishes not being fulfilled due to shortages.
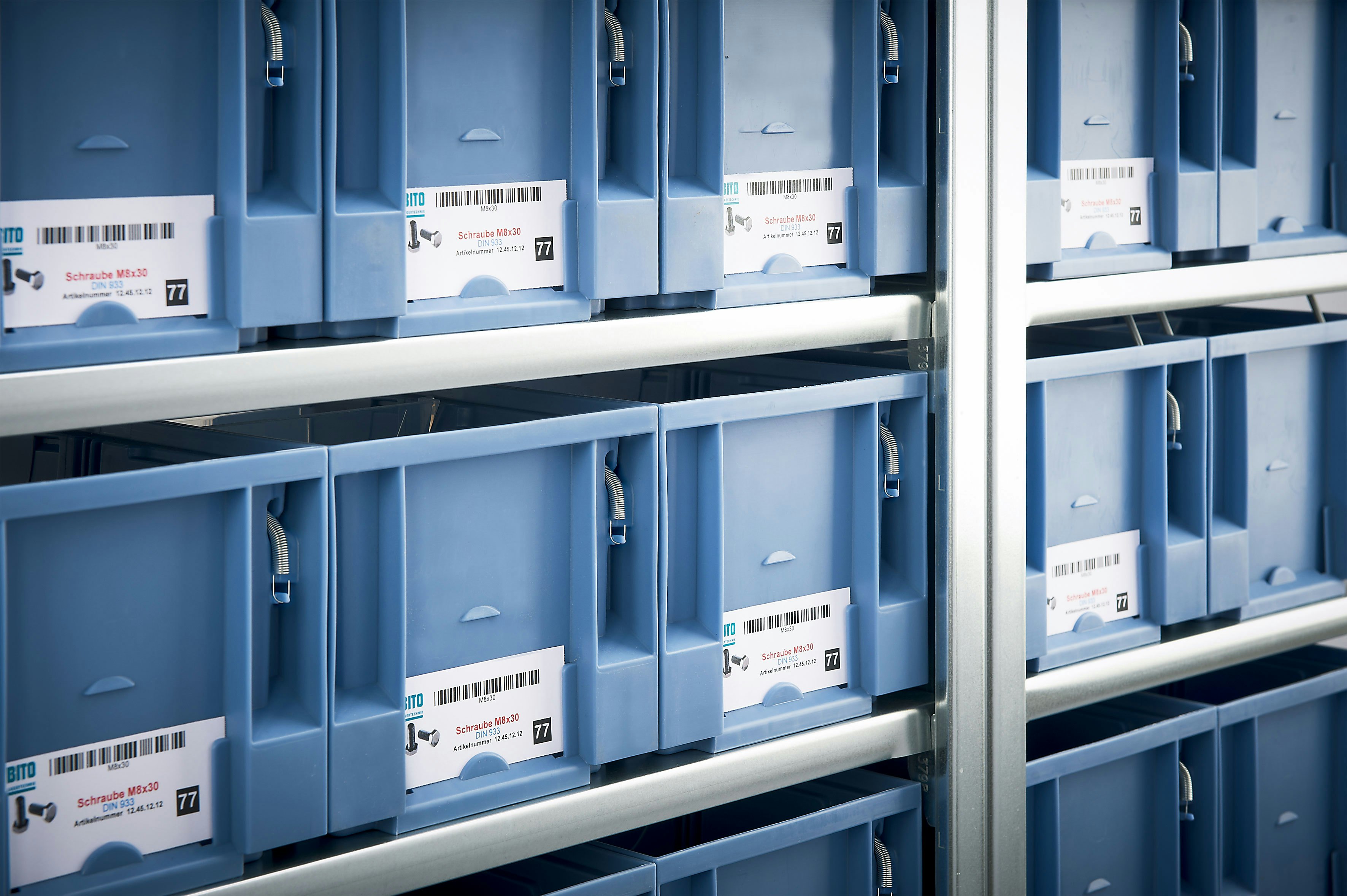
Management in the Kanban System
With the Kanban system, no single person needs to know about the entire process chain. Only the open Kanban container is filled at the respective local location. The system thus proves to be self-regulating and self-organizing and is based on local knowledge and simple rules. It resembles self-organized systems from nature, which are based on swarm intelligence. Think, for example, of the actions of army irons in an army state. This results in a new function for managers in the kanban system. They must first set the framework conditions so that the process chain can function at all. However also conception of resonance-wave (see above) often demands usage of wisdom of many people, i.e. of swarmintelligence. The manager is given the role of the team manager, whose task it is to organise the self-organisation of the team. In addition, he acts as moderator, motivator, coach, coordinator and conflict manager or trouble shooter in order to harmonize the processes.
When Does the Kanban Method Make Sense?
However, the kanban system does not make sense everywhere. If you manufacture only a few or a few products, the method is not suitable. It fits best with a high proportion of identical parts with a small number of variants. Production control and material flow, logistics and replenishment are based exclusively on actual material consumption at the point of supply or consumption. As already mentioned, this method provides a high degree of flexibility and lean stocks. However, the entire supply chain or supply chain logistics can be disrupted if a point in the process is not available. If you want to implement KANBAN, your company should fulfill some prerequisites:
- Continuous production
- high degree of product standardisation with strictly synchronised production
- Unique designations for the exact allocation of cards and containers Consistent container management
- Large fluctuations in production must be avoided
- Transport cycles must be shortened and designed uniformly
Kanban containers and racks
Special racking systems and containers for Kanban systems and logistics are now standard in intralogistics. These include C-parts containers, which combine the advantages of shelf and open fronted storage bins, or Euromodule containers. The space in the Kanban shelves is optimally utilised by the C-parts containers. They allow top and front picking, i.e. access to the C parts from the front (the window is pushed down) and from above (the box is pulled out and the restraint device holds it in the shelf). The dosing disc of the box allows the filling volume to be used up to the top. Through the window, the employee can see exactly how many parts are still in the box at any time. With the single container kanban, the principle is implemented within a box. If the last part is removed at the front, the supply quantity can be used by pulling up the dosing disc. The ordering process for new C parts is triggered by removing the card or RFID tags from the back of the box. With the two-container kanban, the first crate is pulled out of the shelf after the last part has been removed. The card is removed and the ordering process is triggered. Then the second box is pulled into the front position. The ordered box with the supply parts is then pushed in from behind (FIFO principle). A Euromodule container is also very suitable for the Kanban method, as it can be stored well in inclined floor or piece goods flow racks. It is 600 millimetres long and available in various heights and widths. The series is designed in such a way that the different container sizes can be stacked modularly, but still in a firm bond fitting on a Euro pallet. It is extremely stable and therefore safely stackable and also has a large internal volume. The smooth inner surfaces allow easy cleaning. With the integrated ergonomically shaped handles, the Euromodule container can be easily pulled and carried.
Kanban system with barcode or RFID
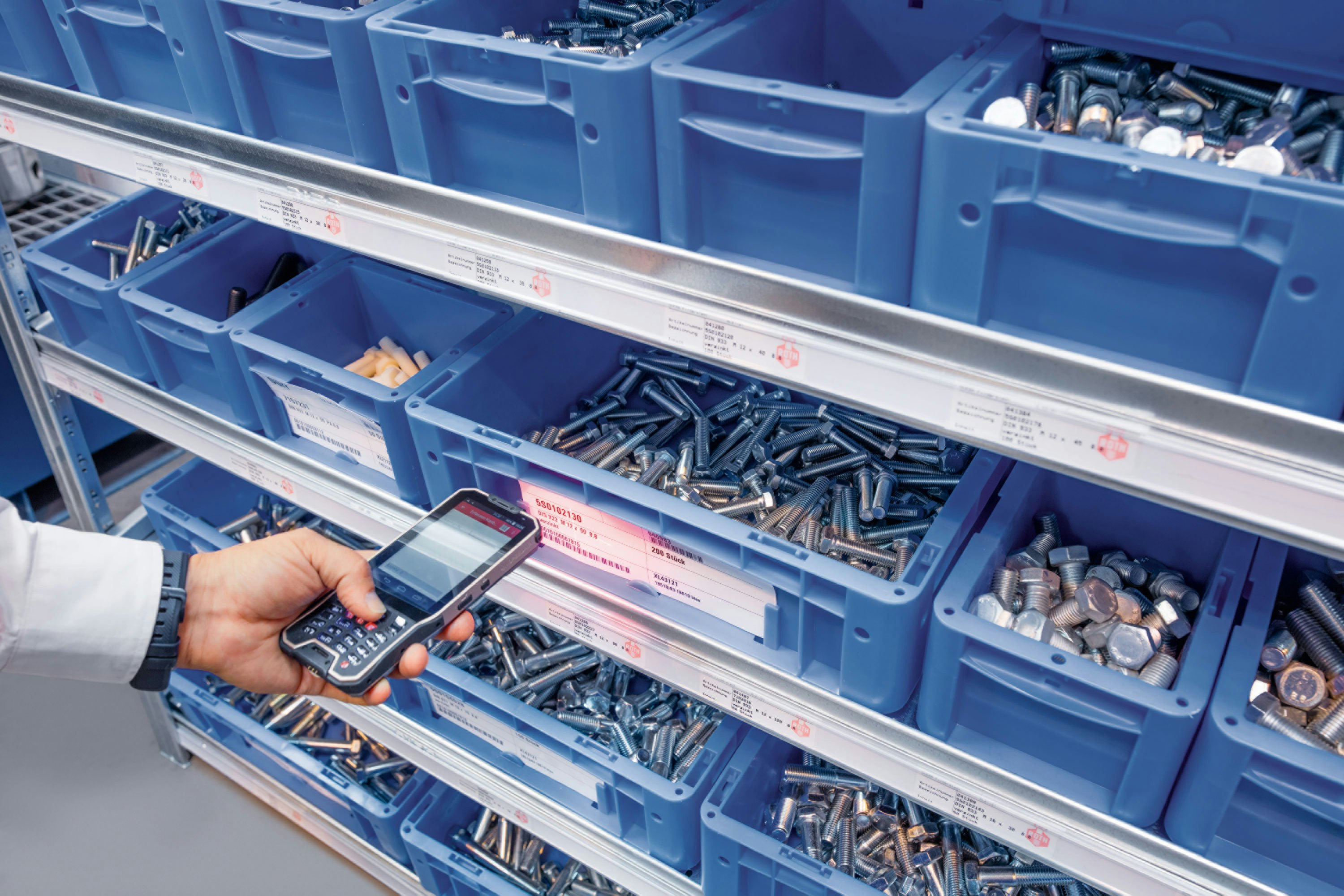
Nowadays storage media such as barcodes or RFID chips are used instead of the Kanban card. The data or the production order is transferred via WIFI to the warehouse folding system, ERP system or to the corresponding component supplier. In the barcode system, the barcodes of the empty containers of the corresponding components are manually scanned by an employee and transmitted to the respective component supplier, who then delivers these parts. In an RFID system, this process is automated. The article and container data are automatically transmitted from the customer's production facility to the central warehouse via radio frequency identification (RFID). This means that automated repeat orders are placed here without scanning and without manual recording. The RFID tag or RFID transponder has an antenna and is attached to the respective object or Kanban container. Each day can be identified by a unique data security number. In addition, an RFID system consists of a reader for reading the transponder and a transmitter unit for data transmission or automated reordering of components for production.
Would you like detailed advice on storage equipment, Kanban systems, containers and racking? Then please contact one of our experienced warehouse technology experts via email, telephone or contact form.