Reduce walking distances in the warehouse - 5 ideas for quickly implementable measures
Speed and innovation are two decisive factors for companies when it comes to competing. This applies without exception to all sectors, but especially to those companies that have a logistics department. This is where the greatest potential lies to increase the efficiency and speed of work processes and thus bring an entire company forward.
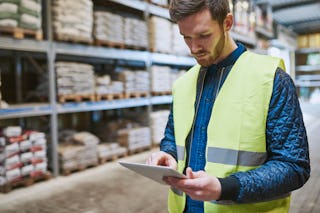