Ergonomics and occupational safety in the warehouse
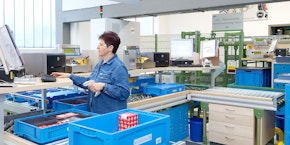
Topics overview:
Many workers today suffer from back pain (46 per cent) and shoulder and neck pain (40 per cent), which affects them at work. This is often due to an ergonomically incorrectly designed workplace. The height and distances of tables, chairs, work desks, picking and workshop tables and trolleys, etc. are incorrectly dimensioned and therefore not ergonomic. The illumination and ventilation of rooms is poor, loads are lifted incorrectly, work equipment is poorly designed, the working environment is too loud and much more. In modern times (from 1919 onwards), the Bauhaus initially dealt with the subject of ergonomics. However, it was only consistently and comprehensively developed and applied by US product designer Henry Dreyfuss and his design office. The ergonomic teaching pursues the goal of optimally adapting the workplace and environment to the individual. The term comes from Greek and is composed of the words "ergon" ("work") and "nomos" ("law").
In Germany, in addition to universities and universities of applied sciences, the Federal Institute for Occupational Safety and Health (BAUA) "Fachgruppe 2.3 Human Factors, Ergonomie", the VDI and the DIN Standards Committee for Ergonomics (NAErg) are particularly concerned with this topic. Joint committees of DIN and VDI coordinate their work plans. The BAUA defines ergonomics as "theory that applies principles, data and methods to the design of work systems with the aim of optimising the well-being of people and the performance of the overall system". Ergonomics can generally be regarded as a sub-discipline of occupational safety.
Standards, guidelines and laws
According to the Commission for Occupational Health and Safety and Standardization, "from the point of view of occupational health and safety, the overlap between DIN standards and VDI guidelines must be viewed with scepticism. Although both are developed according to fixed rules, the multi-part series of standards DIN 8201 places considerably more detailed requirements on the standardization procedure than the 16-page VDI 10002 for the guideline procedure is able to. The Occupational Health and Safety Act (ArbSchG) obliges employers to avoid occupational accidents and safety, work-related illnesses and to design work in a way that is humane (§§ 2, 3 ArbSchG). This includes both the design of the workplace, the workplace and the working environment as well as the design of work processes, procedures and organisation (ergonomics). The employer must determine which occupational health and safety measures are required by means of the risk assessment in accordance with § 5 ArbSchG. In the workplace ordinance (ArbStättV), which was comprehensively amended in 2016, the concept of ergonomics is now also taken into account literally. In addition, since 2016 the ArbStättV has also included the contents of the German Display Screen Work Ordinance (BildScharbV), which was repealed at the same time. According to the ArbStättV, "when setting up and operating the workplaces of employers, the measures in accordance with ArbStättV § 3 paragraph 1 must be carried out and the state of the art, occupational medicine and hygiene, ergonomic requirements and in particular the rules and findings published by the Federal Ministry of Labour and Social Affairs in accordance with ArbStättV § 7 paragraph 4 must be taken into account".
Design of an ergonomic warehouse or production workstation
In addition to correct workplace design and compliance with limit values for the load caused by lifting and carrying loads, noise, vibrations and shocks, room climate, lighting conditions, software operation, etc. also play a major role in workplace ergonomics.
Adjustment of the respective workplace in the enterprise
Workstations in industry, e.g. in warehouses, are extremely diverse, because the work to be done in the companies is often very different. Each workplace and the respective employee working there must be viewed individually. The work equipment should be able to be ergonomically optimally adjusted to the employee's body measurements. Especially when working in a seated position, the worker should be able to adjust chairs, tables, monitors and other equipment to his or her measurements and at the same time design the workplace himself or herself. Work equipment must generally be easily accessible. Long periods of working in a standing position place a great strain on employees and their health, i.e. circulation, back and legs. Ergonomic standing aids, floor mats, flat shoes with a footbed and frequent breaks when sitting or lying down can help here.
Lifting of loads
Loads are often lifted and carried in warehouses and production areas. Therefore, the employees concerned should be instructed in how to lift and carry them correctly. Above all, it is important that the back is straight when transporting loads. This reduces the load on the intervertebral discs by about 20 percent. Lifting and carrying aids must be available for heavier loads. In general, the Load Handling Ordinance (LasthandhabV) applies. Similar to the Hazardous Substances Ordinance or the Workplace Ordinance, the employer is obliged by the LasthandhabV to assess the operation for risks to health associated with the movement of heavy freight. The work processes must be checked for four key characteristics: the duration (or frequency) of a load, the actual load weight, the posture adopted and the conditions under which the load is handled. This can be used to determine a kind of hazard value. In accordance with the Load Handling Ordinance, technical or organisational changes must take place if a certain limit value is exceeded. In principle, load weights should be kept as low as possible only if the sequence of work permits. Basically, BITO containers are particularly light and have various ergonomic handle variants (e.g. ergonomic open grips (soft-touch grips) for the Euro stacking container XL). The LEO Locative Automatic guided vehicle system (AGV) is also suitable for the automatic overhead transport of heavier loads on pre-determined routes. It can be used to connect various workplaces in the company - saving power and energy for the employees - and thus ergonomically.
Required minimum lighting (hall lighting)
DIN EN 12464-1 provides guidelines for the required hall lighting. In warehouses, for example, 100 lux should be reached to ensure good orientation and storage and retrieval. In the shipping area it should already be 300 Lux. This information refers to direct workplace lighting. In areas where work is seldom done, the lighting can be varied in an energy-efficient way. Other lighting requirements covered by the DIN standard include glare, uniformity and colour rendering. For glare, the standard specifies the "Unified Glare Rating" (UGR) procedure, which serves as the rating and defines maximum values. Based on DIN, the workplace directive for lighting takes the values into account. From illuminance to glare, you will find all the values required for an optimum working environment.
Noise and vibration occupational health and safety ordinance (LärmVibrationsArbSchV)
The Noise and Vibration Occupational Health and Safety Ordinance (LärmVibrationsArbSchV) protects employees from actual or potential health and safety hazards caused by noise or vibrations at the workplace. The Technical Rules for Noise and Vibration Protection at Work (TRLV Lärm) reflect the state of the art, occupational medicine and industrial hygiene as well as other assured occupational science findings for the protection of employees from the hazards of noise. The following order of priority shall be taken into account when defining and implementing protective measures:
- Noise emissions shall be prevented or reduced as far as possible from their source.
- Technical protective measures shall take precedence over organisational protective measures.
- Technical or organisational protective measures shall take precedence over individual protective measures (personal hearing protection).
The selection and use of new work equipment should take place under the priority aspect of noise reduction. Workplaces, workspaces and workplaces are to be designed and furnished to reduce noise. The duration and extent of employee exposure should be reduced and hearing protection should be worn (Download TRLV Lärm).
A typical noise source in storage and comissioning areas is the noise emission from conveyor technology, forklifts, etc.
The correct selection of the storage tank alone enables the storage operator to make a major contribution to noise reduction. Due to different possibilities of the bottom design of the containers, volume reductions of up to 10 dB are possible, which corresponds to a halving of the volume perception.
As ergonomics, safety and health at work are very wide-ranging issues, they cannot be fully addressed in this article. You will find further information below.