Creating an orderly warehouse
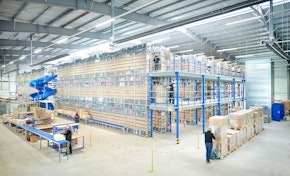
Every logistics manager wants efficient operations with perfect processes but what is required to plan and build an orderly and efficient storage system? Disorder shreds nerves, time and ultimately money. Logistics and production depend on orderly and economic warehousing – it is the only way to ensure the efficiency of operating procedures.
Storage solutions for efficient intralogistics
When planning and building a warehouse, there are numerous important aspects to consider. Because the design and equipment within the warehouse depend on the intended use and space constraints, the first point to establish is the installation’s function.
The aim is always to provide the best possible support for operational processes. An orderly and traceable storage system will guarantee the most efficient intralogistics possible. Warehouse planning includes, among other things, material flow planning, ensuring good use of space as well as efficient workplace design.
Sufficient capacity for peak loads
When beginning to plan storage a detailed list of operational requirements will be needed along with an understanding of the types and quantities of goods and materials to be stored in the warehouse. If necessary, the assortment should also be subdivided into groups of goods according to their turnover frequency – the so-called ABC analysis. These aspects are crucial to get the dimensions and installation set up correct. High quality data is therefore indispensable and it is generally advisable to plan for sufficient stock reserves to ensure capacity even during peak trading periods.
In practice, a maximum storage capacity of between 80 and 90% has proven to be optimal. Stock holding of above 90% capacity is often found to be counterproductive in everyday operations.
From pallet racking to hand loaded shelving
The correct choice of shelving or racking is fundamental to optimising the storage system. A thorough analysis of the different options is therefore essential.
Pallet racking offers the advantage of standardisation and simple handling during order picking as well as storage and retrieval. It requires a lot of space to accommodate pallets, regardless of the actual storage quantity on the pallet. In addition there must be sufficient free space for storage and retrieval using forklifts, warehouse trucks and hand pallet trucks.
For the storage of small parts, hand loaded metal shelving is the better choice. Automated storage systems allow multiple small parts storage locations to be created using minimal floor space. The result typically provides a better use of the available space.
Vertical storage systems or carousels also provide space-saving storage thanks to a system of rolling trays occupying a minimal footprint.
Use space as profitably as possible
A warehouse can generate a lot of cost, so minimising those costs is the goal of every warehouse development. To this end it is essential to identify the optimum stock level to ensure delivery capability and reduce the risk of production bottlenecks. It determines the required storage system dimensions and the number of locations required. The quantity and frequency of the goods handled are also determining criteria for creating a warehouse layout that makes the best possible use of space.
The use of warehouse management software should also not be underestimated for the efficient and economic operation of a warehouse – even for small businesses with small stock levels.
Goods receipt, picking warehouse and shipping
Delivery times that are excessively lengthy risk far more than damage to a company’s image. Speed of delivery is an essential component towards gaining competitive edge. In addition, non-compliance with delivery deadlines sometimes can lead to legal issues. This makes it all the more important to set up an orderly and fully thought through storage system.
The degree of organisation of a warehouse will depend primarily on the quantity of items stored. Companies quickly reach their limits when there is an increase in product range and the number of consignments. When planning a warehouse, technical capacities and business considerations must be taken into account. Basic factors include the number of shipments, the returns rate, the number of items and the size of the items in stock. For many ecommerce companies, a simple three-way division of their warehouse into goods receipt, picking and shipping is perfectly sufficient.
Planning and implementation of complex warehouse concepts
In a warehouse, each individual article has a storage bin. The storage bin is allocated either randomly or numerically. With the numerical location assignment, items are stored in the order of their article numbers. This process is suitable for a large number of small to medium-sized companies with a manageable range of products.
In the case of random space allocation, warehouse management software ensures the allocation of new articles to the next free storage space. In this case, the automated assignment of item and storage bin numbers is essential.