Sacchi Giuseppe S.p.A.
Service efficiency also depends on the decision to reorganise logistics, a process which began in 2009 and is constantly evolving.
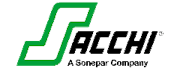
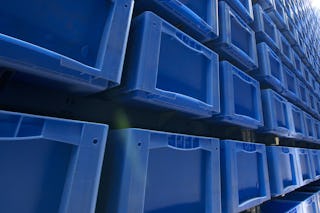
Our customer
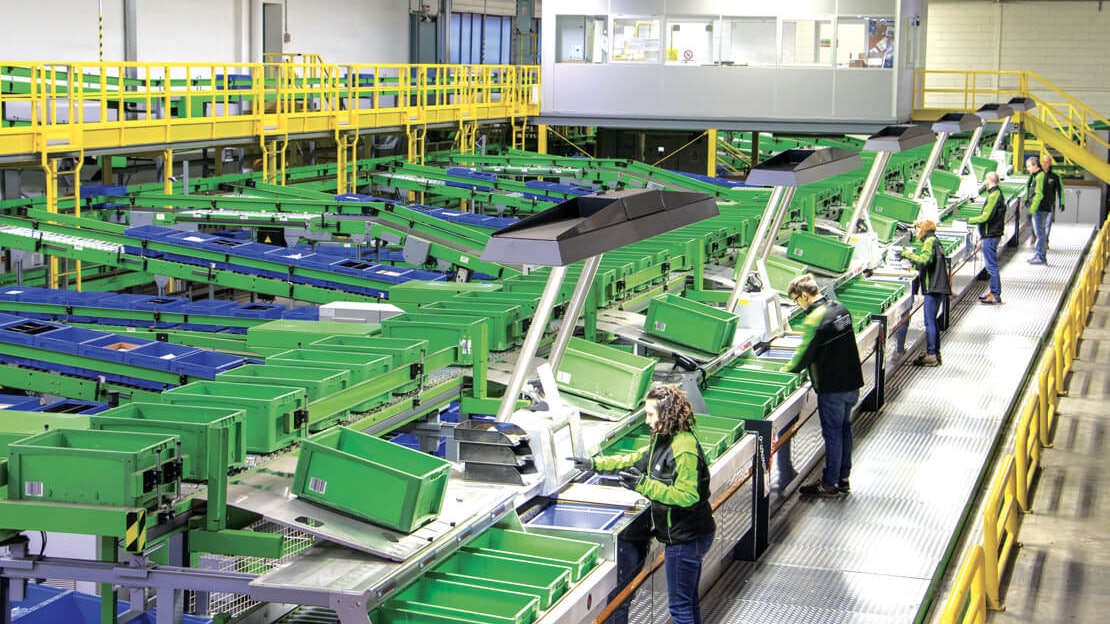
Sacchi Giuseppe S.p.A., founded in 1957, with the subsidiaries Comel, D.m.e. and DEMO, is one of the main Italian companies in the distribution of electrical equipment, lighting and industrial automation. For 60 years Sacchi has been working to offer a high quality service, providing the best products and solutions. 95 points of sale in Northern Italy, 2 consumer electronics megastores, a logistics centre and 1,350 people who work in synergy, with competence and professionalism, to respond efficiently and quickly to the needs of over 40,000 customers. In 2017 Sacchi became part of the international Sonepar Group.
Some impressions of our customer solution
Project brief
The BITO Solution
Überbegriff fehlt
» Logistics management begins with the acceptance of incoming goods and material storage in the automated warehouse. The goods are stored in barcoded, single-reference BITO containers with dividers. The customer uses blue containers for material storage.
Überbegriff fehlt
» Green BITO bins are used for order picking (different colors for different purposes). The operator receives the blue container at his workstation, from which he takes one or more references from the load carrier and places them in the green container for distribution.
Überbegriff fehlt
» At the end of the picking process, the container is either moved to the packing area for shipment to customers and to the sorting area for replenishment at the point of sale. In the packing area, the BITO containers are then sealed with BITO single-use seals and labeled for shipping.
On-site application and key features of our storage solution
- 3,000 square meters of logistics space for storage, product receiving, order picking and outgoing goods/sorting
- Automated warehouse of 55,000 units, to manage 25,000 references
- 50,000 items available within 24h
Customer benefits
In what way has the BITO solution helped our customer to realise their full potential?
- 20,000 reference lines can now be handled per day.
- Picking errors were reduced by two-thirds.