Safety regulations in the warehouse - from occupational safety and health protection to access control
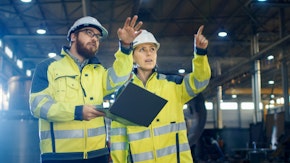
80,153 - this is how many reportable accidents at work occurred during manual transport in 2016. According to the German statutory accident insurance (DGUV), there are also around 155,000 accidents involving the manual handling of objects. Apart from the damage suffered by a person, the affected companies also have to make considerable organisational efforts after an accident at work: compensate for the employee's absence from work, investigate the cause of the accident and rectify defects, pay any compensation for pain and suffering, as the safety regulations in the warehouse were not sufficiently met. A situation that can be easily avoided. This article will tell you how.
Safety begins with people
Despite the latest technical developments and high safety standards, internal storage and transportation are still among the most accident-prone activities in companies in a wide range of industries. The Berufsgenossenschaft für Gesundheitssysteme und Wohlfahrtspflege (BGW), for example, has discovered that storage in stacks and shelves, despite the use of the latest technology, repeatedly leads to risks for people working in the warehouse. For this reason, it is advisable for every company to observe and regularly check a number of important things with regard to the safety regulations in the warehouse.
First of all, warehouse and logistics managers should instruct their employees at least once a year about the safety regulations in the warehouse and document this instruction carefully in order to be able to prove it in case of doubt. When it comes to annual safety updates, all areas within a warehouse must be addressed equally - regardless of whether they are concerned with order picking, means of transport or storage. In this context, it is also advisable to check the protective equipment of each employee and to renew it if necessary. Warehouse and logistics managers should in any case ensure that their employees always wear protective clothing. For example, the risk of injury from falling objects can be minimised by wearing helmets or safety shoes.
The optimum design of a warehouse creates safe working conditions
A major safety risk within a warehouse is in many cases a lack of space. Narrow and nested traffic routes can cause industrial trucks to hit the storage shelves when manoeuvring and objects to fall out or over shelves. Wide aisles and sufficient space between the shelves are therefore particularly important components of the safety regulations in the warehouse. The more space between individual shelves or stacks, the lower the risk of collisions.
Although transporters and industrial trucks can make some of the work easier or even completely relieve people today, manual equipment handling is still very important in all warehouses. This is also an important point which the safety regulations in the warehouse should absolutely take into account. It is precisely the lifting and carrying of loads that in many cases leads to overloading or strain of the spine as well as to trapping, crushing and cutting of hands or feet. To prevent this, warehouse and logistics managers should, where possible, provide their employees with suitable aids to facilitate hand transport and minimize the risk of injury. There should also be no danger of slipping in a warehouse.
If the goods are transported in containers, high-quality containers with ergonomic handles and rounded edges help to avoid injuries. The risk also exists with sharp edges of steel products, such as storage shelves. For the protection of the employees, therefore, value should be placed on the highest quality measures.
Control the risk factor shelf
A large proportion of all accidents in the warehouse are caused by inadequately secured shelves. A risk that can be significantly reduced by detailed planning of shelf loading. For example, the safety regulations in the warehouse also aim to prevent accidents caused by shelving. The main reasons for the risk factor shelf are incorrect storage and inadequate fastening. Overloaded shelves can quickly break and falling objects can trigger a chain reaction. It is also possible for poorly fastened shelves to fall over - a dangerous situation for all employees. In particular, if the articles stored are liquids with dangerous contents, technical and organisational measures in favour of the safety regulations in the warehouse are a must.
What may seem at first glance to be a massive amount of work, however, is basically done quickly. And this with only a few but effective measures. Storage areas should be sufficiently large, resilient and leveled. Shelves that stand back to back for space reasons should have a wire mesh back wall - this prevents a mutual shifting of the goods. It is also possible to use profiled trusses here. These provide a secure hold for the stored goods. Metal shelves are the best choice for all types of goods. Sturdy and correctly positioned, they guarantee safe storage. Anyone who stores liquids should install large drip trays made of suitable material and arrange the liquids in such a way that there are no unfavourable or dangerous mixtures in the event of an accident. In addition, stacks of cartons or crates should not be higher than permitted.
Clear safety regulations for handling means of transport
In addition to regular maintenance of racks and stacks, the means of transport used in a warehouse should also undergo periodic inspection. That way, defects can be quickly identified and accidents prevented. For the safety regulations in the warehouse, this is an essential factor for maintaining them permanently. In addition, warehouse and logistics managers should always ensure that employees only use the means of transport for the goods they are suitable for (a sack truck for crates and sacks, a hand pallet truck for pallets, etc.). In addition, each employee should only use means of transport for which he or she is qualified.
A sufficiently trained staff is therefore indispensable for the constant observance of the safety regulations in the warehouse. Appropriate certificates, such as for driving an industrial truck, are crucial. In addition, it is the duty of warehouse and logistics managers to thoroughly check their personnel and their qualifications before deploying them in certain areas. The better trained the employees are, the safer the work in the warehouse will be, as the specialists know what they have to pay particular attention to when it comes to safety. Access control for certain areas can also prevent accidents, as unauthorised persons have no access and cannot endanger themselves or others.
Using the power of the collective
The safety regulations in the warehouse also include comprehensive structural, technical and organisational fire protection. This includes not only the installation of fire detectors, but above all the provision of emergency and escape plans. Corresponding regular simulations of a fire give the employees security and the peace of mind they need in an emergency. In addition, there should always be a qualified first-aider on site in every warehouse. It is advisable to make first aid courses compulsory.
In addition to all safety precautions, it is advisable to install appropriate warning and instruction signs in the necessary places to point out possible dangers. Nevertheless, the best security regulations in the warehouse are of no use if not all those involved in a company adhere to them. For this reason, warehouse and logistics managers should attach great importance to communication. If all employees are involved in the topic of safety, each of them feels responsible. The power of the collective can thus prevent some accidents.
Fotoquelle Titelbild: © shutterstock.com / Gorodenkoff