Container: Key position in material flow
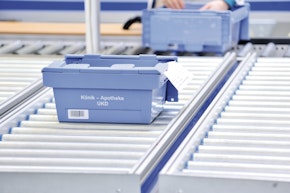
The right design or selection of containers is extremely important for the uninterrupted flow of materials in a company. They not only act as load carriers in logistics, but also as information transmitters and thus form the basis for Kanban systems. They also play a major role in process optimization in the company. For example, container design also has an enormous impact on the running characteristics and noise development on conveyor lines. They are therefore also an important part of the design of ergonomic workplaces.
Not only product carriers
The material flow includes all processes from the extraction of raw materials, through processing and treatment, to distribution to the supplier and the route to the end consumer. It also includes processes relating to transport and logistics, storage, quality and testing of the product. If it takes place within the company, it is called internal material flow. It is usually accompanied by a flow of information, which is recorded, transported, processed and output in the form of data. Containers play an important role in storage, transport and information transfer. However, the flow of material can only be automated by standardising the load carriers. The load carriers such as pallets, boxes, containers, etc. must be clearly defined, i.e. standardised, so that storage and retrieval machines, shuttles, automated guided vehicles (AGVs), industrial trucks and conveyor technology can bring their full potential to bear in logistics. For example, small load carriers (KLT) - also known as Euro crates, Euronorm containers or Euronorm boxes. They can therefore be sent to centralised ‚pooling‘ hubs for re -use. KLTs were developed to optimise the logistics chain in the automobile manufacturing and supply industry. The system is modularly adapted to the base areas 1200 × 800 mm (Euro pallet) and 1200 × 1000 mm (ISO). The floor space doubles in each case and has the nominal dimensions 300 × 200 mm, 400 × 300 mm and 600 × 400 mm. In the meantime, the Euro containers are also used outside the automotive industry due to their standardisation. Containers also serve as information carriers due to their unique identification number (stored on barcode, RFID). In the warehouse management system (WMS) or in the material flow computer, this ID is linked to a specific article or order. This enables automatic recognition and control of the containers and goods in the warehouse.
Examples of functional container design
The physical properties and charecteristics of modern boxes allow a wide range of operations in logistics. For example, containers on conveyor systems should run as quietly and with as little friction as possible. There are also extremely small tolerances for the deflection of the container base. For example, the XL-Motion from BITO has been specially designed for automated warehouses, so that it optimally meets the requirements for flatness, roughness and friction coefficient. This is ensured by the new rotating floor. In order to be able to withstand high loads during storage operation, it has been equipped with a smooth frame construction which is connected to the box with diagonal support ribs. This sandwich construction prevents the floor from deflecting under high loads. Because it is always flat and smooth, the XL-Motion runs extremely quietly on the conveyor system. This makes for a much more pleasant working atmosphere in the warehouse. The low noise level not only leads to less stress and thus less downtime, but also to fewer errors and greater job satisfaction.
Trays are used in automatic small parts warehouses to transport and store non-conveyable goods such as cardboard boxes or loose articles. They are specially tailored to the requirements of the respective conveyor technology. For automatic loading and unloading, there is a lift-out function which separates the goods on the tray from the tray. The goods can then be stacked on pallets, for example.
Kanban systems and containers
Kanban is a method of decentralized production control, in which individual production and logistics processes are triggered with the help of data cards - known as Kanban in Japanese. The advantages of the Kanban method are decentralized control, lean warehousing and Just-In-Time (JIT) logistics of parts needed in production. Important data, such as article number, quantity, storage location, etc., are noted on the cards. Production therefore sends a signal to the upstream production stage that new parts are needed. For example, an empty container with an order card for a specific component is sent to the (Lean) warehouse and a full container is taken away again. The parts warehouse now knows that this item must be reordered in a certain quantity and sends this order to the source (the supplier). The supplier fulfills the order and brings the corresponding component into the warehouse in the desired quantity. The kanban card therefore serves as an order card for production, which triggers a certain production order or a resonance wave. In the KANBAN system, no individual person needs to know about the entire process chain. Only the open Kanban container is ever refilled at the respective local point. The system therefore proves to be self-regulating and self-organizing and is based on local knowledge and simple rules. Today, storage media such as barcodes or RFID chips are used instead of the Kanban card. Here, the data or the production order is transferred via WIFI to the warehouse management system, ERP system or to the corresponding component supplier.
Starting point for process optimization
Particularly in the age of Industry 4.0, workflows and processes should be optimized and streamlined even in smaller companies. A good starting point here is the transport and material flow. In particular, the throughput times for materials and products should be reviewed. These pass through unnecessary stations and processing times can possibly be shortened. Every reduction in throughput times means a cost saving. Is the optimum means of transport used at every point in the company? Are special bespoke solutions necessary? The transport containers are of course just as important. Are the appropriate transport containers used for the products, work stations and processes? This is where warehousing, transport or intralogistics can be decisively rationalised, which can reduce costs.
Importance of shelves in the material flow
Shelves are usually one of the locations in the material flow. That is, the goods are removed from the shelf and placed in the flow of material, or the goods come from the goods receipt or production area and are transported to the shelves and placed in storage. Sometimes, however, a material flow also takes place in shelves, for example in flow racks for pallets or containers and cartons. This can be either a replenishment action in a KANBAN system or a replenishment control action in a picking process. Here, the flow direction of the flow rack system from the putaway side to the retrieval side automatically guarantees a movement according to the FIFO principle (first-in, first-out). Intermediate buffers take on a further function in the material flow. In the case of multilevel picking, for example, the "picked" order totes usually have to wait in a rack for the other items.
Would you like to make your material flow more efficient? We can help you with this.