Ergonomie und Arbeitssicherheit im Lager
Ergonomie und Arbeitssicherheit am Arbeitsplatz werden unter hohem Arbeitsdruck immer wichtiger. Neben dem Vermeiden von unnötigen Belastungen spielen Lichtverhältnisse, Lärm- und Vibrationen, u.v.m. eine große Rolle.
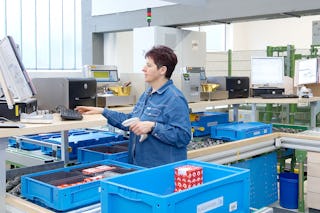
Viele Arbeitnehmer leiden heutzutage unter Rückenschmerzen (46 Prozent) sowie Schulter- und Nackenbeschwerden (40 Prozent) und sind dadurch bei der Arbeit beeinträchtigt. Häufig ist daran ein ergonomisch falsch gestalteter Arbeitsplatz Schuld. Die Höhe und Abstände von Tischen, Stühlen, Arbeitspulten, Kommissionier- und Werkstatttischen und -wagen, etc. sind falsch bemessen und damit nicht ergonomisch. Die Ausleuchtung und Belüftung von Räumen ist schlecht, Lasten werden falsch gehoben, Arbeitsmittel sind ungünstig gestaltet, die Arbeitsumgebung ist zu laut und vieles mehr. In der Neuzeit (von 1919 an) beschäftigte sich zunächst das Bauhaus mit dem Thema Ergonomie. Konsequent und umfassend wurde sie jedoch erst von dem US-amerikanischen Produktdesigner Henry Dreyfuss und seinem Designbüro entwickelt und angewandt. Die ergonomische Lehre verfolgt das Ziel, Arbeitsplatz und -umgebung optimal an den Einzelnen anzupassen. Der Begriff stammt aus dem Griechischen und setzt sich aus den Worten „ergon“ („Arbeit“) und „nomos“ („Gesetz“) zusammen.
In Deutschland beschäftigen sich neben Universitäten und Fachhochschulen vor allem die Bundesanstalt für Arbeitsschutz und Arbeitsmedizin (BAUA) "Fachgruppe 2.3 Human Factors, Ergonomie", der VDI und der DIN-Normenausschuss Ergonomie (NAErg) mit dem Thema. Gemeinsame Ausschüsse des DIN und des VDI stimmen ihre Arbeitspläne ab. Die BAUA definiert Ergonomie als "Theorie, die Prinzipien, Daten und Methoden auf die Gestaltung von Arbeitssystemen anwendet mit dem Ziel, das Wohlbefinden der Menschen und die Leistung des Gesamtsystems zu optimieren.“ Ergonomie kann man generell als eine Teildisziplin des Arbeitschutzes ansehen.
Sie haben keine Lust den Artikel zu lesen? Kein Problem! Hier einfach als Podcast anhören!
Normen, Richtlinien und Gesetze
Laut der Kommission Arbeitsschutz und Normung ist "aus Sicht des Arbeitsschutzes die Überschneidung von DIN-Normen und VDI-Richtlinien mit Skepsis zu betrachten. Zwar werden beide nach festen Regeln erarbeitet, allerdings stellt die mehrteilige Normenreihe DIN 8201 wesentlich detailliertere Anforderungen an das Normungsverfahren, als es die 16-seitige VDI 10002 für das Richtlinienverfahren vermag. Das Arbeitsschutzgesetz (ArbSchG) verpflichtet den Arbeitgeber zur Vermeidung von Arbeitsunfällen und Sicherheit, arbeitsbedingten Erkrankungen sowie zur menschengerechten Gestaltung der Arbeit (§§ 2, 3 ArbSchG). Hierzu gehören sowohl die Gestaltung der Arbeitsstätte, des Arbeitsplatzes und der Arbeitsumgebungsbedingungen als auch die Gestaltung von Arbeitsverfahren, -ablauf und -organisation (Ergonomie). Welche Maßnahmen des Arbeitsschutzes und Sicherheit erforderlich sind, hat der Arbeitgeber durch die Gefährdungsbeurteilung nach § 5 ArbSchG zu ermitteln. In der 2016 umfassend geänderten Arbeitsstättenverordnung (ArbStättV) indes wird der Begriff der Ergonomie nun auch wörtlich berücksichtigt. Zudem sind seit 2016 in der ArbStättV auch die Inhalte der Bildschirmarbeitsverordnung (BildScharbV) zu finden, die dafür zeitgleich aufgehoben wurde. Laut der ArbStättV hat "beim Einrichten und Betreiben der Arbeitsstätten der Arbeitgeber die Maßnahmen nach ArbStättV § 3 Absatz 1 durchzuführen und dabei den Stand der Technik, Arbeitsmedizin und Hygiene, die ergonomischen Anforderungen sowie insbesondere die vom Bundesministerium für Arbeit und Soziales nach ArbStättV § 7 Absatz 4 bekannt gemachten Regeln und Erkenntnisse zu berücksichtigen."
Gestalten eines ergonomischen Lager- bzw. Produktionsarbeitsplatzes
Neben der richtigen Arbeitsplatzgestaltung und der Einhaltung von Grenzwerten für die Belastung durch das Heben und Tragen von Lasten spielen für die Ergonomie von Arbeitsplätzen auch Lärm, Vibrationen und Erschütterungen, Raumklima, Lichtverhältnisse, Softwarebedienung, etc. eine große Rolle.
Anpassen des jeweiligen Arbeitsplatzes im Unternehmen
Arbeitsplätze in der Industrie z. B. im Lager sind äußerst vielfältig, denn die zu erledigenden Arbeiten in den Unternehmen sind oft sehr unterschiedlich. Jeder Arbeitsplatz und der jeweilige dort tätige Arbeitnehmer müssen individuell betrachtet werden. Dabei sollten die Arbeitsmittel ergonomisch optimal auf die Körpermaße des Mitarbeiters eingestellt werden können. Gerade wenn die Arbeit sitzend ausgeführt wird, sollte der Arbeitnehmer die Möglichkeit haben, Stühle, Tische, Monitore und andere Geräte auf seine Maße einzustellen und gleichzeitig den Arbeitsplatz selbst gestalten zu können. Arbeitsmittel müssen generell gut erreichbar sein. Langes Arbeiten im Stehen beansprucht die Mitarbeiter und deren Gesundheit, sprich Kreislauf bzw. Rücken und Beine, sehr stark. Ergonomische Stehhilfen, Bodenmatten, flache Schuhe mit Fußbett und häufige Pausen im Sitzen oder Liegen können hier Abhilfe schaffen.
Heben von Lasten
Im Lager sowie in Produktionsbereichen werden häufig Lasten gehoben und getragen. Daher sollten die betroffenen Mitarbeiter im richtigen Heben und Tragen unterwiesen werden. Wichtig ist vor allem, dass der Rücken beim Lastentransport gerade ist. Dadurch werden die Bandscheiben etwa um 20 Prozent weniger belastet. Für schwerere Lasten müssen Hebe- und Tragehilfen zur Verfügung stehen. Generell gilt die Lastenhandhabungsverordnung (LasthandhabV). Ähnlich wie in der Gefahrstoffverordnung oder der Arbeitstättenverordnung ist der Arbeitgeber durch die LasthandhabV dazu verpflichtet, den Betrieb auf Gefahren für die Gesundheit, die mit der Bewegung schwerer Fracht zusammenhängen, hin zu beurteilen. Die Arbeitsprozesse müssen auf vier Leitmerkmale hin überprüft werden: die Zeitdauer (oder auch: Häufigkeit) einer Belastung, das eigentliche Lastgewicht, die eingenommene Körperhaltung und die Bedingungen, unter denen die Lastenhandhabung stattfindet. Daraus kann eine Art Gefahrenwert ermittelt werden. Im Sinne der LasthandhabV müssen technische bzw. organisatorische Umgestaltungen stattfinden, wenn dabei ein gewisser Grenzwert überschritten wird. Lastgewichte sollten grundsätzlich so gering wie nur möglich gehalten werden, wenn es der Ablauf der Arbeit zulässt. Grundsätzlich sind BITO-Behälter besonders leicht und besitzen verschiedene ergonomische Griffvarianten (z. B. ergonomische Durchfassgriffe (Soft-Touch-Griffe) beim Eurostapelbehälter XL). Für den automatischen flurgebundenen Transport von schwereren Lasten auf vorgezeichneten Wegen eignet sich zudem das Fahrerlose Transportsystem (FTS) LEO Locative. Mit ihm lassen sich verschiedene Arbeitsplätze im Unternehmen - kraft- und energiesparend für die Mitarbeiter - und somit ergonomisch verbinden.
Notwendige Mindestbeleuchtung (Hallenbeleuchtung)
Die DIN EN 12464-1 gibt Richtlinien für die erforderliche Hallenbeleuchtung wieder. In Lagerhallen sollten z. B. 100 Lux erreicht werden, um die gute Orientierung und das Ein- und Auslagern zu gewährleisten. Im Versandbereich sollen es schon 300 Lux sein. Diese Angaben beziehen sich auf die direkte Arbeitsplatzbeleuchtung. In Bereichen in denen selten gearbeitet wird kann die Beleuchtung energieeffizient variiert werden. Weitere Anforderungen an die Beleuchtung, auf die die DIN Norm eingeht, sind unter anderem Blendung, Gleichmäßigkeit und Farbwiedergabe. Für die Blendung setzt die Norm das„Unified Glare Rating” (UGR)-Verfahren fest, welches der Bewertung dient und Höchstwerte definiert. Angelehnt an die DIN nimmt die Arbeitsstättenrichtlinie für Beleuchtung die Werte auf. In ihr finden Sie von der Beleuchtungsstärke bis zur Blendung alle Werte, die für ein optimales Arbeitsumfeld eingehalten werden müssen.
Lärm- und Vibrations-Arbeitsschutzverordnung(LärmVibrationsArbSchV)
Die Lärm- und Vibrations-Arbeitsschutzverordnung (LärmVibrationsArbSchV) gilt zum Schutz der Beschäftigten vor tatsächlichen oder möglichen Gefährdungen ihrer Gesundheit und Sicherheit durch Lärm oder Vibrationen am Arbeitsplatzt. Die Technischen Regeln zur Lärm- und Vibrations-Arbeitsschutzverordnung (TRLV Lärm) geben den Stand der Technik, Arbeitsmedizin und Arbeitshygiene sowie sonstige gesicherte arbeitswissenschaftliche Erkenntnisse zum Schutz der Beschäftigten vor Gefährdungen durch Lärm wieder. Bei der Festlegung und Durchführung der Schutzmaßnahmen ist die folgende Rangfolge zu berücksichtigen:
1. Die Lärmemission muss am Entstehungsort verhindert oder so weit wie möglich verringert werden.
2. Technische Schutzmaßnahmen haben Vorrang vor organisatorischen Schutzmaßnahmen.
3. Technische oder organisatorische Schutzmaßnahmen haben Vorrang vor individuellen Schutzmaßnahmen (persönlicher Gehörschutz).
Dabei sollen die Auswahl und der Einsatz neuer Arbeitsmittel unter dem vorrangigen Gesichtspunkt der Lärmminderung erfolgen. Arbeitsstätten, Arbeitsräume sowie Arbeitsplätze sollen lärmmindert gestaltet und eingerichtet werden. Die Dauer und das Ausmaß der Exposition von Mitarbeitern soll gesenkt werden und Gehörschutz getragen werden.(Download TRLV Lärm)
Eine typische Lärmquelle in Lager- und Kommssionierbereichen sind die Geräuschemissionen von Fördertechnik, Staplern etc.
Alleine durch die richtige Auswahl des Lagerbehälters kann der Lagerbetreiber einen großen Beitrag zur Lärmminderung erreichen. Durch unterschiedlichen Möglichkeiten der Bodenausführung bei den Behälten sind Laustärkeminderungen von bis zu 10dB möglich, was einer Halbierung der Lautstärke-Wahrnehmung entspricht.
Da die Themen Ergonomie und Arbeitssicherheit sowie Gesundheit am Arbeitsplatz sehr weitreichende Themen sind, können sie in diesem Artikel nicht vollständig behandelt werden. Im Folgenden erhalten Sie weitere Informationen.