One-Piece-Flow und schlanke Produktion
Der Begriff One-Piece-Flow wird meist im Zusammenhang mit dem Toyota-Produktionssystem oder Lean Production benutzt. Der mitarbeitergebundene Arbeitsfluss führt zu neuartigen Möglichkeiten der Individualisierung von Produktionsprozessen.
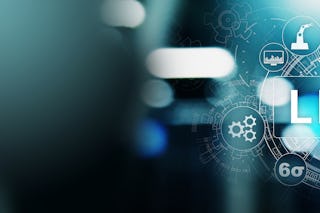
Unter One-Piece-Flow versteht man logistisch eine Fließfertigung, bei denen die Mitarbeiter das Werkstück durch die verschiedenen Bearbeitungsgänge und unter Umständen bis zu seiner Fertigstellung begleiten (mitarbeitergebundener Arbeitsfluss). Dazu werden sie in Gruppen organisiert und können rotierend eingesetzt werden. Die Mitarbeiter müssen dabei alle anfallenden Arbeitsgänge beherrschen. Der Begriff wird meist im Zusammenhang mit dem Toyota-Produktionssystem (TPS) oder „Lean Production“ (Schlanke Produktion)“ benutzt. Im Rahmen von Industrie 4.0 und "Smart Factory" bietet die One-Piece-Flow-Fertigung neuartige Möglichkeiten zur Individualisierung von Produktionsprozessen. Sie ermöglicht eine reibungslose wie auch in sich geschlossene Zusammenarbeit zwischen Mitarbeitern, Ressourcen und Maschinen. Je störungsfreier die Kommunikation, desto effizienter, ressourcenschonender und flexibler lässt sich die Schlanke Produktion gestalten. Zudem wird die Motivation beim One-Piece-Flow durch eine abwechslungsreichere Beschäftigung gesteigert. Damit wird in aller Regel auch die Fehlerrate gemindert.
Lean Production und Lean Management
Die Automobil- und Maschinenbau-Industrie setzt schon seit langem Kanban-Systeme, Just-in-Time (JIT) und One-Piece-Flow im Rahmen des TPS ein. Das TPS wird durch drei Hauptbestandteile geprägt: die JIT-Anlieferung, das Kanban-Prinzip und Kaizen (Permanenter Verbesserungsprozess). Unter dem Begriff Lean Production oder auch Schlanke Fertigung versteht man den Einsatz von Produktionsfaktoren wie Personal (Arbeit), Werkstoffe, Organisation und Betriebsmittel, bei dem auf die Vermeidung von Verschwendung und Zeiteffizienz geachtet wird. Ein Schwerpunkt liegt dabei auf der Prozessoptimierung, durch die neben der Qualität auch die Flexibilität eines Unternehmens gesteigert bzw. optimiert werden soll. Dementsprechend wird Lean Management als übergeordneter Begriff als Methode verstanden, durch die die Unternehmen ihre Geschäfts-Prozesse optimieren, Verschwendung in diesen reduzieren und somit ihre Wertschöpfungskette effizienter gestalten können. Im Zentrum von Lean Management steht die Kundenorientierung. Es bedient sich verschiedener Tools und Hilfsmittel wie beispielsweise dem PDCA-Zyklus, der 5s-Methode oder Kanban. Zu den besonderen Merkmalen von Lean Production und Lean Management gehören: Fokus auf die Wertschöpfung des Produktes, größere Übertragung der Verantwortung an die Mitarbeiter, Vermeidung von Verschwendung, Verbesserung der internen und externen Kommunikation, Konzentration auf das Wesentliche und die Kundenorientierung. Zu den Werkzeugen und Methoden von Kaizen und damit natürlich auch von Lean Management und Lean Production gehört u. a. auch die 3-Mu-Checkliste. Mit der Checkliste können Quellen von Verschwendungen und Ursachen von Problemen aufgedeckt werden.
Muda: Verschwendung
Muri: Überlastung
Mura: Abweichung von Standards oder Regeln
In den drei Bereichen werden beispielsweise folgende Dinge überprüft: Mitarbeiter, Technik, Methode, Zeit, Gestaltungsspielraum, Vorrichtungen und Werkzeuge, Material, Produktionsvolumen, Transporte, Umlauf, Platz, Bewegungsabläufe (Ergonomie), Denkart (Geisteshaltung).
Die sieben Verschwendungsarten (Mudas) werden wie folgt benannt:
Überproduktion
Wartezeit
überflüssiger Transport
Herstellung fehlerhafter Teile
überhöhte Lagerhaltung
unnötige Bewegung
ungünstiger Herstellungsprozess
Weitere Prinzipien und Ziele sind die Zerlegung und Analyse des Wertestroms (alle notwendigen Schritte bis zur Fertigstellung eines Produkts bzw. der Anlieferung des Produktes beim Kunden), das Fluss-Prinzip (Wertstrom möglichst in einem stetigen Fluss), das Pull-Prinzip ( Produktion wird an den Bestellungen der Kunden ausgerichtet) und Kanban (Materialnachschub in der Produktion wird verbrauchsorientiert mithilfe sogenannter Kanban-Karten gesteuert). Zentrale Bestandteile des Konzepts sind zum einen, dass nur benötigtes Material angefordert wird und zum anderen, dass auch keine Produktion auf Vorrat stattfindet. Geht das Material zuneige, wird der entstehende Bedarf rechtzeitig durch entsprechende Kanban-Karten signalisiert.
Zwingend notwendig für die Lean Production sind ein Höchstmaß an Disziplin, Genauigkeit und Pünktlichkeit, um damit eine größtmögliche Effizienz in den Abläufen zu schaffen.
Beispiel: Vermeidung von Überproduktion und Überbeständen
Eine der wesentlichen Verschwendungsarten bei der Produktion ist wie oben genannt die Überproduktion und damit die Erhöhung der Bestände. Dadurch wird Kapital des Unternehmens unnötig gebunden und steht für einen anderen Zweck, z. B. die Investition in Innovation nicht mehr zur Verfügung. Zu hohe Bestände binden aber nicht nur Kapital, sondern blockieren auch Flächen und Räume, die dann für eine andere Nutzung - beispielsweise den Einsatz weiterer Produktionsmittel - nicht mehr zur Verfügung stehen. Überbestände behindern in der Logistik oftmals auch die etablierten Prozesse. Durch den Such- und Umräumaufwand entstehen zusätzliche Kosten für das Unternehmen. Durch eine flexible Fertigung mit kleinen Losgrößen bis hin zur Einzelfertigung (Losgröße 1) können Überbestände minimiert und die Lagerbestände klein gehalten werden. Um kleine Losgrößen wirtschaftlich fertigen zu können, müssen vor allem die Rüstzeiten für das Wechseln von einem auf ein anderes Werkstück reduziert werden. Nicht zu vernachlässigen sind hier auch Ver- und Entsorgungszeiten. Die Produktionszeit, Rüstzeit, Ver- und Entsorgungszeiten von Material sowie Todzeiten (Wartezeiten auf Material, Bediener etc.) sind wesentliche Zeitbestandteile einer Fertigung. Durch Rüstzeitworkshops werden Rüstzeiten durch die Methoden des Lean Management und der Lean Production drastisch reduziert. Eine weitere Methode sind sogenannte Rüstzyklen. Hier wird eine Maschine mehrfach mit kleinen Schritten auf die Herstellung eines anderen Bauteils umgerüstet, bevor ein größerer Wechsel der Produktion verbunden mit wesentlichen Umbauten der Maschine(n) durchgeführt wird.
Die Ver- und Entsorgung der Maschine kann oftmals mit Robotern und automatisierten Handhabungs- und Transporttechniken erfolgen. In den letzten Jahren sind verstärkt kollaborative Automatisierungslösungen (z. B. kollaborative Roboter bzw. Cobots) auf den Markt gekommenen. Die Arbeiter können hier direkt mit einer Maschine, ohne aufwändige Sicherungseinrichtungen wie Zäune und Lichtschranken, zusammenarbeiten.
Auswirkungen auf die Mitarbeiter
Für die Mitarbeiter bedeutet dies einen dramatischen Wandel ihrer bislang gewohnten Abläufe und der eingeübten Verhaltensweisen. Bei der Lean Production und dem Lean Management müssen die Maschinen und damit die Arbeitnehmer immer genau das produzieren, was für den Kundenauftrag gerade im Moment benötigt wird. Der Mitarbeiter wird nun nicht mehr daran gemessen, dass die Maschine möglichst lange läuft und eine hohe Auslastung und Ausbringung (Produktionsleistung) aufweist. Gleichzeitig müssen sie mit Kollege Cobot bzw. Automatisierungstechnik zusammenarbeiten, was für die meisten Menschen zunächst sicher sehr befremdlich ist. Durch den extremen Wandel der Arbeitskultur wird ein Change-Management im Unternehmen zwingend notwendig.
Vor- und Nachteile von Lean Production
Die Hauptvorteile der Schlanken Produktion und von Lean Management sind verkürzte Durchlaufzeiten von Produkten, eine höhere Produktionsgeschwindigkeit sowie Flexibilität und größere Produktivität. Zudem lässt sich die Qualität durch entsprechende Qualitätsmaßnahmen steigern. All das führt zu deutlichen Kostensenkungen.
Die großen Nachteile dieser Produktionsweise sind die kleinen Lagerbestände, wodurch kurzfristige Störungen oder Probleme in der Produktion kaum abfangen werden können. Wegen der JIT-Fertigung sind viele einzelne kleine Lieferungen mit Material notwendig, was zu einer höheren Umweltbelastung (Emissionen) und Auslastung von Verkehrswegen führen kann. Lean Management und Schlanke Produktion eignen sich vor allem bei einer hohen Variantenvielfalt der Produkte.
Die neue Ausrichtung hin zu Industrie 4.0, die eine immer größere Digitalisierung, Automatisierung und Vernetzung im Unternehmen und in der Produktion bringt, wird eine ständigen Verbesserung der Prozesse und damit den Gedanken von Lean Management und Lean Production befördern. Der internationale Wettbewerb erfordert die kontinuierliche Optimierung von Kosten und Prozessen.