Flexible Fertigung in der Smart Factory
Industrie 4.0 ermöglicht die umfassende Digitalisierung der Fertigung. Kennzeichnend für die Smart Factory sind die Vernetzung und Selbststeuerung von Systemen sowie die dezentrale Produktionssteuerung.
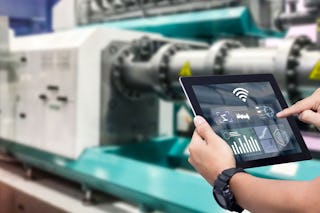
Der Industriestandard 4.0 ermöglicht die Intelligente Fertigung und damit die Smart Factory. Experten sprechen auch von der sog. vierten industriellen Revolution. Nach Wasser- und Dampfkraft, Massenfertigung mithilfe von Fließbändern und der Automatisierung der Produktion wird nun die umfassende Digitalisierung der industriellen Produktion eingeleitet.
Um aber den Begriff und die Organisationsprinzipien der Smart Factory bzw. intelligenten Fabrik besser verstehen zu können, soll hier zunächst tiefer auf Industrie 4.0 eingegangen werden. Im Rahmen von Industrie 4.0 sind zwei Entwicklungen - nämlich die Vernetzung und Selbststeuerung von Systemen - entscheidend. Vernetzte Systeme können Daten miteinander austauschen und somit intelligent aufeinander zu reagieren. In der herkömmlichen (klassischen) Fabrik wird die Fertigung zentral gesteuert - in der Intelligenten Fabrik dezentral.
Zentrale und dezentrale Produktionssteuerung
Für die Fertigungssteuerung wird ein sog. Production Planning System (PPS)-System eingesetzt. Die spezialisierte Software verbindet die Produktionsplanung mit der Fertigungssteuerung. Die Produktionsplanung berücksichtigt die Nachfrage nach den zu produzierenden Gütern und den Bedarf an Rohstoffen, Einzelteilen und Baugruppen. Darüber hinaus beschäftigt sie sich mit dem Produktionsablauf bzw. der Produktionsdurchführung. Zu den Hauptaufgaben der Fertigungssteuerung gehören die Minderung der Maschinen-Leerzeiten, die Verkürzung der Durchlaufzeiten von Aufträgen und die Lenkung der Fertigung entsprechend der Ablaufplanung. Weiterhin werden alle Daten der Produktionslogistik und der Supply Chain verarbeitet. Bei der zentralen Produktionssteuerung laufen alle Informationen über ein zentrales Steuerungszentrum. Hier werden Produktionsaufträge in die Fertigung geschoben, ohne dass Kundenaufträge für die zu produzierenden Artikel vorliegen müssen (Push-Prinzip). Man produziert mit allen Risiken auf Halde. Zudem muss jeder einzelne Fertigungsschritt an das zentrale System zurückgemeldet werden. Man kann hier bereits leicht erkennen, dass die zentrale Steuerung ineffizienter ist als die dezentrale Steuerung. Die Produktionsmenge basiert auf vorherigen Abschätzungen der Nachfrage und ist daher mehr oder weniger genau. Eine Über- oder Unterauslastung der Maschinen, etc. muss möglichst vermieden werden. Das Push-Prinzip wird überwiegend bei großen Losgrößen und einer geringen Anzahl von Varianten eingesetzt.
Bei der dezentralen Fertigungssteuerung wird immer erst nach dem Vorliegen eines konkreten Kundenauftrags produziert (Pull-Prinzip). Es ist eng mit den Begriffen Kanban und Just-In-Time-Produktion verwoben. Kanban ist eine Methode der dezentralen Produktionssteuerung, bei der mithilfe von Datenkarten – japanisch Kanban genannt - einzelne Produktionsprozesse und Logistikprozesse angestoßen werden. Die Vorteile der Kanban-Methode sind die dezentrale Steuerung, eine schlanke Lagerhaltung (Lean Lager) und Just-In-Time-(JIT)Logistik von Teilen, die in der Fertigung benötigt werden. Auf den Karten sind wichtige Daten, wie Artikelnummer, Menge, Lagerort, etc., vermerkt. Die Fertigung sendet also an die vorgeschaltete Produktionsstufe ein Signal, dass neue Bauteile benötigt werden. Z. B. wird ein leerer Behälter mit Bestellkarte für ein bestimmtes Bauteil in das Lean Lager gesendet und ein voller Behälter wieder mitgenommen. Das Teilelager weiß jetzt, dass dieser Artikel in einer bestimmten Menge nachbestellt werden muss und sendet diesen Bestellauftrag an die Quelle (den Lieferanten). Der Lieferant erfüllt den Auftrag und bringt das entsprechende Bauteil in der gewünschten Menge in das Lean Lager. Die Kanban-Karte dient also als Bestellkarte der Produktion, die einen bestimmten Produktionsauftrag bzw. eine Resonanzwelle auslöst, die von der Fertigung bis zum Lieferanten verläuft. Bei der zweiten Variante dient die Kanban-Karte als Identifikationskarte für das neu zu produzierende bzw. zu bestellende Bauteil. Zwei benachbarte Produktionsstufen sind zu einem Regelkreis verbunden, wodurch eine problemlose Koordination der aufeinanderfolgenden Stufen entsteht. Z. B. holt sich Produktionsstufe A ein Bauteil aus dem Lean Lager (Pufferlager) und Produktionsstufe B füllt das Teilelager wieder mit dem entsprechenden Bauteil auf.
Selbstgesteuerte Maschinen mit CPS
In der Smart Factory werden sog. selbstgesteuerte Maschinen eingesetzt. Diese Maschinen und auch die Produkte sind mit Sensoren ausgestattet. Sie kommunizieren ständig untereinander, optimieren ihre Abläufe fortlaufend bzw. passen situationsgerecht ihre Prozesse an. Darüber hinaus tauschen sie auch Daten via Internet der Dinge mit anderen Systemen im Unternehmen z. B. in der Produktion, dem Vertrieb und der Entwicklung aus. Sogar Kunden und Lieferanten werden in die vernetzte Welt eingebunden. Die selbstgesteuerten Maschinen aber auch Produkte und andere Systeme werden mit „cyberphysischen Systemen“ (CPS) ausgestattet sein. CPS sind Netzwerke kleiner mit Sensoren und Aktoren ausgestatteter Computer, die als sog. „Eingebettete Systeme „integriert werden und via Internet kommunizieren. Sie ermöglichen die Steuerung in Echtzeit auch über große Entfernungen. Mit ihrer Hilfe werden künftig betriebliche Prozesse geplant, gesteuert und kontrolliert. CPS werden auch die Flexibilität der Maschinen und damit der Fertigung ermöglichen. Die selbstgesteuerten (anwendungsoffenen) Maschinen können je nach Bedarf unterschiedliche Werkzeuge einsetzen und Bearbeitungsschritte ausführen. Im Unternehmen werden alle Prozesse - von der Bearbeitung der Auftragseingänge, über das Ressourcenmanagement und die Fertigung bis hin zur Auslieferung - vertikal integriert und können situativ immer wieder aufeinander abgestimmt werden. Selbst weltweit verteilte Firmenniederlassungen und Lieferanten können via Internet miteinander smart koordiniert werden. All das erlaubt die kontinuierliche Optimierung aller Prozesse auf Basis aktueller Daten aus den Märkten und aus der Produktion. Die CPS führen auch zu einer vollständigen Transparenz über den Zustand aller Maschinen. Eine vorausschauende Wartung wird möglich. Die selbstgesteuerten Maschinen überprüfen ständig den eigenen Zustand und bestellen entsprechende Ersatzteile sobald Verschleißerscheinungen zu groß werden. Die Flexibilität der Maschinen und das Predictive Maintainance führen zu einer besseren Auslastung der Produktionskapazitäten und einem flexiblen Ressourcenmanagement. Zudem werden Fehler häufiger vermieden oder können schneller behoben werden.
Organisationsprinzipien von Industrie 4.0 und Smart Factory
Industrie 4.0 ist ein Organisationsgestaltungskonzept, das aus vier grundlegenden Organisationsgestaltungsprinzipien (OGP) besteht. Die Prinzipien unterstützen Unternehmen bei der Identifikation und Implementierung von Industrie-4.0-Szenarien. 1. OGP: Vernetzung: Maschinen, Geräte, Sensoren und Menschen werden vernetzt und können miteinander via Internet der Dinge (IdD) kommunizieren. 2. OGP: Informationstransparenz: Sensordaten erweitern Informationssysteme digitaler Fabrikmodelle, um so ein virtuelles Abbild der realen Welt zu erstellen. 3. OGP: Technische Assistenz: Assistenzsysteme unterstützen den Menschen mit Hilfe von aggregierten, visualisierten und verständlichen Informationen. 4 OGP: Dezentrale Entscheidungen: Cyberphysische Systeme sind in der Lage, eigenständige Entscheidungen zu treffen und Aufgaben weitgehend autonom zu erledigen.
Ziele der Intelligenten Fertigung
Das Ziel der Intelligenten Fertigung ist die Verbesserung der Herstellungsleistung durch Datenanalyse und die Identifizierung von Möglichkeiten für die Automatisierung einzelner Operationen. Durch die Analyse der riesigen Datenströme der vernetzten Maschinen kann z. B. auch ein drohender Ausfall von einzelnen Maschinen oder -gruppen erkannt werden und eine vorsorgliche Wartung bzw. der Austausch von Teilen eingeleitet werden. Auf diese Weise lassen sich Stillstandszeiten vermeiden. Zudem können Datentrends analysiert werden, um eine verlangsamte oder ineffiziente Fertigung aufzuspüren. Darüber hinaus können die Daten für Simulationen von verschiedenen Prozessen z. B. mithilfe des sog. „Digitalen Zwillings“ verwendet werden, um die effizientesten Fertigungsprozesse zu ermitteln.
Smarte Systeme in der Intelligenten Fabrik
Neben den smarten Maschinen und Anlagen, Cyberphysischen Systemen, smarten Produkten und dem IdD kommen auch Technologien wie Digitale Zwillinge (die gesamte Produktion und Fabrik wird digital simuliert), Big Data-Verarbeitung und -Analyse, Advanced Robotics-Systeme, Augmented Reality sowie 3D-Printing und Rapid Prototyping zum Einsatz.
Der 3D-Druck (Additive Fertigung) kann für die schnelle Herstellung von Prototypen genutzt werden. Material wird Schicht für Schicht aufgetragen und so ein dreidimensionaler Gegenstand (Werkstück) erzeugt. Dabei erfolgt der schichtweise Aufbau computergesteuert aus einem oder mehreren flüssigen oder festen Werkstoffen nach vorgegebenen Maßen und Formen. Beim Aufbau finden physikalische oder chemische Härtungs- oder Schmelzprozesse statt. Typische Werkstoffe für das 3D-Drucken sind Kunststoffe, Kunstharze, Keramiken und Metalle. Die eigentlichen Daten für das 3D-Modell stammen aus einem Computer Aided Design (CAD)-System. Durch Rapid Prototyping kann ein Unternehmen schon in der Planungsphase relativ einfach ein Probe-Modell bauen. Somit können schon frühzeitig Fehler oder Schwächen erkannt und behoben werden, bevor innerhalb des eigentlichen Produktionsprozesses durch nicht entdeckte Fehler hohe Kosten anfallen würden.
Literatur:
Zillmann Mario, Lünendonk GmbH, Smart Factory – Wie die Digitalisierung Fabriken verändert, Transformation von der Werkshalle bis zur Unternehmensleitung, Mindelheim 2016, Download
Burke Rick, Mussomeli Adam et al., The Smart Factory, Responsive, adaptive, connected manufacturing, Deloitte University Press, 2017 Deloitte Development LLC, Download
Dr. Huber Walter, Hofmann Benedikt, Smart Factory 2025, So sieht die Fabrik der Zukunft aus, April 2019, MM Maschinenmarkt, Link