Engpässen in der Supply Chain vorbeugen
Die Ursachen für Engpässe sind sehr vielfältig. Sie reichen von Naturkatastrophen, Ausfällen bei Lieferanten bis hin zu Nachfrageschwankungen. Den Unternehmer können sie viel Geld kosten.
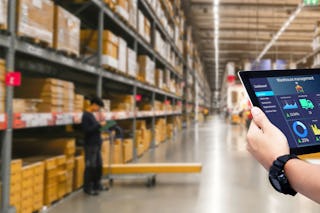
Es gibt viele Gründe, durch die es zu Verzögerungen oder gar Ausfällen in der Supply Chain kommen kann. Aus Kundensicht ist das immer ärgerlich und den Unternehmer kostet es viel Geld. Deswegen muss jedes Unternehmen Engpässen in der Supply Chain vorbeugen. Dabei können diese Engpässe in der Produktion, dem Transport sowie der Lagerung von Waren und Zulieferprodukten auftreten. Alle an der Supply Chain beteiligten Unternehmen sind ebenso involviert. Das Supply Chain Management strebt die Effizienzoptimierung der Lieferkette an. In größeren Unternehmen mit komplexen Supply Chains ist es extrem wichtig, die Wechselwirkungen zwischen optimiertem Lagerbestand, Lieferfähigkeit und Kapazitätsauslastung aufeinander abzustimmen. Dies hat zur Folge, dass die Anlieferung von Waren exakt zeitlich geplant werden kann und Sicherheitsbestände gesenkt werden können.
Was führt zu Engpässen in der Supply Chain?
Die Einflussfaktoren bzw. Ursachen sind sehr vielfältig. Sie reichen von Naturkatastrophen über unzureichende Infrastruktur bis zu Ausfällen bei Lieferanten und Nachfrageschwankungen (Produktmix und Menge der Bestellungen schwanken). Im Folgenden werden aufgrund der Vielzahl von Einflussfaktoren auf die Logistik und Lieferketten nur einige beispielhaft aufgezeigt.
Eine kleine, aber plötzliche Änderung der Verbrauchernachfrage kann zu großen Nachfrageschwankungen in vorgelagerten Bereichen der Lieferkette führen. Durch eine mangelnde Informationstransparenz und lange Vorlaufzeiten werden diese Nachfrageschwankungen noch verschärft. Dies wird als sogenannter Bullwhip-Effekt bezeichnet, bei dem sich die Nachfrage entlang der Lieferkette quasi stromabwärts vom Endverbraucher aus aufschaukelt. Eine Fehlanpassung der Bestände kann auch zu Out-of-Stock-Situationen - sprich zu einem Engpass - führen. Generell sind Push-Systeme in der Produktion hier benachteiligt, da sie auf Nachfrageabschätzungen beruhen.
Sich stark und schnell verändernde (dynamische) Märkte führen zu einer Vielzahl von Auswirkungen und Anpassungsproblemen, die zu Engpässen führen können. Gesellschaftliche und soziodemographische Entwicklungen beeinflussen nicht nur das Nachfrageverhalten, sondern auch das Käuferpotential. Beispielsweise führt ein allgemeiner Wertewandel zu Veränderungen des Kaufverhaltens und auf vielen Märkten zu einer Marktpolarisierung. Eine zunehmende Marktsättigung bzw. Stagnation oder sogar Marktschrumpfung stellen die Unternehmen auf vielen Märkten vor Wachstums- und Überlebensprobleme. Eine stärkere Internationalisierung der Märkte und des Wettbewerbs führt zu einer stärkeren Innovationsdynamik.
Immer kürzere Produktzyklen können zu einem Engpass in der Fertigung bzw. bei der Auslieferung führen - insbesondere dann, wenn das Produkt schon bei Markteinführung ein Renner ist. Die Produktion in den Unternehmen muss häufig umgestellt werden, was eine völlige Neuorganisation und Umrüsten der Maschinen voraussetzen. Überall hier können Verzögerungen auftreten, die wiederum zur Verzögerung von Prozessen und einem Engpässen führen können.
Entlang der Supply Chain sind natürlich auch die Kapazitäten keine fixen Größen. Die zählbaren Ressourcen wie Menschen und Maschinen können begrenzt sen. Zudem kann die Schwankungen von Prozessen kapazitätsmindernd oder erhöhend wirken. Die Qualifikation von Mitarbeiter und die Eignung von Maschinen, Anlagen, Transportmitteln, etc. beeinflusst ebenso die Kapazitäten. Je nach Auftragsmix wird eine unterschiedliche Kombination dieser Ressourcen und Qualitäten gefordert. Die hohe Anzahl der fest terminierten Fertigungsaufträge konkurriert um die oft knappen Ressourcen und Kapazitäten. Wünscht nun ein Kunde einen früheren Liefertermin müssen die Kapazitäten und Ressourcen umdisponiert werden und das gesamte System kommt abermals zum Schwingen.
Die Logistik und Intralogistik eines Unternehmens können ebenfalls zu einem Engpass werden. Gerade bei extrem schwankender Nachfrage und einem breitem Produktportfolio können schnell Platzprobleme entstehen. Die Nachfrageschwankungen müssen eventuell durch Pufferlager (z. B. Fachbodenregale, Blocklager) für Halbzeuge und Fertigartikel ausgeglichen werden. Das ganze System aus Logistik und Intralogistik muss leistungsfähig genug sein, um die Kundennachfrage bzw. die Schwankungen bewältigen zu können. Die Durchlaufzeiten für Aufträge müssen dementsprechend kurz sein. Das ganze Lager muss effizient gestaltet und optimiert sein. Dazu gehören eine passende Lagerorganisation, ein optimales Regalsystem, kurze Transportwege, geeignete flurfreie und flurgebundene Transportmittel, u. U. ein Lagerverwaltungssystem, geeignete und leistungsstarke Mitarbeiter, u. v. a. m.. Natürlich können auch in der nachfolgenden Logistik bzw. Transport Engpässe auftreten.
Wie kann man Engpässe frühzeitig erkennen?
Die Theory of Constraints (TOC) geht davon aus, dass der Durchsatz (Leistungsfähigkeit) eines Systems nur von einem einzigen Faktor bestimmt wird, welcher als Engpass bezeichnet wird. Von diesem Engpass aus werden alle vorgeschalteten und nachkommenden Prozesse optimiert. Eine Prozessoptimierung kann also nur erfolgreich sein, wenn sie übergreifend das Gesamtsystem betrifft und den Engpass immer als Ausgangspunkt nimmt. Bevor der Engpass beseitigt werden kann, wird dafür gesorgt, dass nur so viel Arbeit im Gesamtsystem vorhanden ist, wie auch tatsächlich durch den Engpass verarbeitet werden kann.
Aber wie kann man einen auftretenden Engpass vorhersehen? Durch die Vielfalt der Einflussfaktoren auf das System Versorgungskette sind Ort, Zeitpunkt und die Ursachen des Auftretens von Engpässen teilweise schwierig vorauszusagen.
Im Lean Management existiert das Werkzeug der Wertstromanalyse (1). Dabei werden u. a. folgende Fragen gestellt: Wie entstehen Dienstleistungen und Produkte, für die der Kunde bezahlt? Wo und wie kommen Aufträge ins System? Welche Arbeitsprozesse werden durchlaufen - im Push- oder Pull-Modus? Was lässt sich an den Arbeitsstationen beobachten (Kapazitäten, Aufträge, Durchsatz, Bestände)? Auf diese Weise können Störungen oder Engpässe identifiziert werden. Schwierigkeiten machen aber sich ständig veränderten Parameter und natürlich die komplexen Einflussfaktoren. Das System ist nicht mehr einfach zu determinieren. Die Engpässe können fallweise oder dynamisch auftreten und ein klares Muster ist nicht zu erkennen. Sie sollten sich fragen: Sind die vermeintlichen Engpässe wirklich die kritischen Schwachstellen des Systems? Was hindert das Gesamtsystem daran, besser zu werden? Auch Annahmen und „ungeschriebene Gesetze“ (mentale Barrieren), die dem heutigen Handeln im Unternehmen zugrunde liegen, sollten hinterfragt werden. Erstellen Sie hier am besten eine Sammlung von Ursachen für statische, dynamische bzw. mentale Barrieren. Und werten Sie sie danach, ob die Ursache bekannt oder unbekannt ist. Danach können Sie sich auf die Suche nach den wirklich kritischen Schwachstellen und Ursachen machen.
statisch: bsp. Arbeitszeitmodelle, Qualifikationsdefizite (Kapazitäten)
dynamisch: z. B. Schwankungen der Nachfrage, Zulieferprobleme, Planungs-/ Steuerungsdefizite, Prozessschwankungen
mentale Barrieren: z. B. Kundenanforderungen, Prozesse für Mitarbeiter zu belastend
Vorbeugen und Beseitigung von Engpässen
Hier können Sie schon im Vorfeld die Logistik und Intralogistik bzw. die Prozesse optimieren. Die Prozessoptimierung (2) hat die Aufgabe, Arbeitsabläufe zu analysieren, diese zu dokumentieren, Schwachstellen aufzudecken und einen verbesserten Arbeitsablauf zu entwickeln. Ziele der Prozessoptimierung können neben dem reibungsloseren Ablauf und der Verbesserung der Qualität auch Kosteneinsparungen sein. Zu den Methoden der Prozessoptimierung gehören beispielsweise das Business-Process-Reengineering, Total Quality Management, Lean Production, Kaizen, Six Sigma und 5S/ 5A. Voraussetzung für das Erkennen von Verschwendung und Engpässen ist das Kennen der Prozesse und Abläufe. BITO bietet eine Reihe von technischen Lösungen wie Kanban-Regale, das Fahrerlose Transportsystem LEO Locative, Behälter, Visuelles Management, u. v. a. für Prozessverbesserungen an.
Um Schwankungen in der Nachfrage zu bewältigen, sind Pufferlager unerlässlich. Sie sollten natürlich auch ein gutes Lagerbestandsmanagment (3) betreiben. Die Lagerbestands-Optimierung ist eine Methode, um die Beschränkungen oder Ziele des Kapitalinvestments mit den Zielen des Servicelevels über ein breites Sortiment von Artikelpositionen unter Berücksichtigung von Nachfrage und Angebotsschwankungen auszubalancieren.
Denken Sie auch an die Auswirkungen des demographischen Wandels. Der Fachkräftemangel muss schon jetzt berücksichtigt werden. Dazu gehört die Aus- und Weiterbildung von Mitarbeitern wie auch der evtl. Einsatz von Robotern, Cobots bzw. FTS.
Suchen Sie sich leistungsstarke Zulieferer. Bei der Lieferantenoptimierung (4) geht es darum, unzuverlässige Lieferanten zu identifizieren und durch zuverlässige zu ersetzen. Der Ausfall von kompletten Lieferungen oder Teillieferungen von Rohstoffen, Halbzeugen und Produkten sowie eine nicht verwertbare schlechte Qualität kann einen Betrieb sehr schnell in den Abgrund stürzen. Bei der Auswahl vertrauenswürdiger Lieferanten sollten Sie sich folgende Fragen stellen: Liefert der Lieferant pünktlich und qualitativ zuverlässig? Wie flexibel reagiert er, wenn Sie überraschend eine größere Menge eines Produkts bestellen müssen? Wie werden Reklamationen geregelt? Wichtig ist ein einheitliches Bewertungssystem für die Lieferanten und das -management zu etablieren und nicht nur monetäre Gründe für die Entscheidung für einen Lieferanten zu wählen. Grundsätzlich ist es wichtig, eine bedarfsorientierte Lieferkette zu implementieren. Die tatsächliche Nachfrage nach Produkten sollte die Lieferkette antreiben. Dadurch kann die Nachfragevariabilität besser gemanagt werden. Bei saisonalen und akut auftretenden Auftragsspitzen kann auch im Versand, bei der Qualitätskontrolle und der Logistik auf Zeitarbeitskräfte zurückgegriffen werden. Entsprechendes Verpackungsmaterial sollte rechtzeitig eingekauft werden. Der Transport zusätzlicher Lieferkontingente kann beispielsweise an einen Logistikdienstleister mit flexiblen Kapazitäten ausgelagert werden. Die beschrieben Maßnahmen können nur Denkanreize geben. Die Liste der Maßnahmen zur Beseitigung eines Engpasses und dessen Auswirkungen kann im Einzelfall recht lang werden.
Literatur:
1 Wolff Reinald, Wo ist der Engpass? Oder, das Ende der Auslastungsorientierung., SCM Blog, mehr hier
2 Prozessoptimierung in der Produktionslogistik, BITO Fachwissen, mehr hier
3 Warum sollten Sie Lagerbestände minimieren?, BITO Fachwissen, mehr hier
4 Schwankungen der Nachfrage und des Angebots bewältigen, BITO Fachwissen, mehr hier