Hohe Anforderungen an regalkonforme Industrieböden
Industrieböden sind extrem hohen statischen und dynamischen Lasten ausgesetzt und müssen dementsprechend konstruiert werden. Große dynamische Lasten werden z. B. durch Flurförderzeuge und Regalbediengeräte erzeugt.
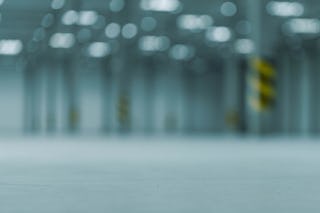
Beim Bau von Industrie- und Lagerhallen müssen sehr viele Dinge bedacht werden. Ein wichtiger Bestandteil ist der Hallenboden, der häufig sehr große statische und dynamische Lasten tragen und aushalten muss. Das Versagen eines Industriebodens (1, 2) hätte enorm große Auswirkungen auf die Betriebsabläufe. Im Ernstfall könnte der ganze Produktionsablauf bzw. der Lagerbetrieb zum Stillstand kommen, was einer Katastrophe für das betroffene Unternehmen gleichkommen würde.
Enorm große Lasten
Ein Industrieboden aus Beton muss statische Lasten z. B. der Tragstützen der Regale aushalten können. Dies sind sehr stark fokussierte Lasten auf einer geringen Standfläche (um die 100 cm²) der Regalstützen und können eine Größenordnung im Tonnenbereich (beispielsweise um die zehn Tonnen) erreichen. Große dynamische Lasten werden durch Flurförderzeuge und Bediengeräte wie Regalbediengeräte (RGB) erzeugt. RGB bewegen sich auf Führungsschienen durch die Regalgassen und erzeugen so sich verändernde (dynamische) Lasten, die den Betonboden schwer beanspruchen. Das enorme Gewicht der RGB mit einer Höhe bis zum 50 m kann mit Nutzlast locker auch mal 80 Tonnen erreichen. Das dies zu enorm hohen dynamischen Belastungen für den Industrieboden führt, kann sich jeder vorstellen. Aber auch Gabelstapler können enorm hohe Belastungen auf den Betonboden ausüben.
Wie ist ein Industrieboden aufgebaut?
Im Wesentlichen besteht ein Industrieboden aus einem gleichmäßig tragfähigen Untergrund, einer Tragschicht (ohne Bindemittel oder hydraulisch gebunden) und einer Betonplatte mit bearbeiteter Oberfläche. Das Substrat bzw. das Grundmaterial, das den Boden bildet, muss analysiert werden und eine hohe Widerstandsfähigkeit gegenüber Druck, geringe Tendenz zum Verrutschen und eine geringe Kapazität zur Wasseraufnahme aufweisen. Nur wenn das Substrat ausreichend tragfähig ist, kann die Industrie- oder Lagerhalle bzw. der Boden dort auch errichtet werden.
Ist das Substrat geeignet wird darüber eine stark verdichtete Tragschicht aus natürlichem Mischgut oder einem Füllgut aufgebaut. Bei Freiflächen kann zwischen Substrat und Tragschicht noch eine Frostschutzschicht eingefügt werden. Zudem befindet sich zwischen Substrat und Tragschicht eine Art Film bzw. Gleitschicht, damit sich der Betonboden beim Trocknen frei bewegen kann und so keine Risse und Bodenwellen entstehen. Beim Trocknen zieht sich der Betonboden zusammen, die Tragschicht aber nicht. Die Gleitschicht mindert die auftretenden Spannungen beim Trocknen des Betons. Über der eigentlichen Tragschicht wird die Bodenplatte aus Beton gegossen. Im Betonboden können leichte Metallgitter nahe der Oberfläche eingelassen sein, um Risse, Bodenwellen und Dehnfugen zu vermeiden. Mit lasergesteuerter Maschinentechnik können heutzutage Betonböden in sehr hoher Ebenheit gebaut werden.
Über dem Boden aus Beton wird ein monolithischer Bodenbelag als eigentliche Arbeitsoberfläche eingefügt. Sie besteht aus einer rund 50 mm dicken Beschichtung aus granuliertem Beton. Diese Betonschicht kann zusammen mit dem Industrieboden oder auch nachher errichtet werden. Darüber hinaus kann auch eine sehr dünne Arbeitsoberfläche (3 mm) aus z. B. Kunstharz gegossen werden, die auch spezielle (elastische) Eigenschaften aufweisen kann. Da die Anforderungen an Industrieböden und deren Oberfläche sehr hoch sind, muss beim Bau mit äußerster Vorsicht und Präzision vorgegangen werden.
Einbau des Industriebodens
Industrieböden in Produktions- und Lagerhallen benötigen durchweg eine extrem genaue Nivellierung in engen Toleranzen. Das Ausgleichen von Höhenunterschieden ist für alle weiteren Bauphasen, wie z. B. den Aufbau der Regale und den Einbau von Regalbediengeräten, enorm bedeutsam. Der Einbau eines Bodens mit geringen Höhentoleranzen benötigt eine spezielle Technik aber auch gut geschulte und geschickte Fachkräfte. Nachdem das Fundament vorbereitet wurde und die Tragschicht nivelliert ist, wird ein stabiler Metallrahmen angebracht. Darauffolgend wird Beton in den Metallrahmen gespritzt, der heutzutage bei Industrieprojekten mit lasergesteuerter Maschinentechnik nivelliert wird. Dabei kann der Beton in Streifen oder großflächig eingebracht werden. Der Beton kann mit einem speziellem Fließmittel vermischt sein, das den Beton verflüssigt und zudem stabilisiert (3). Das ermöglicht einerseits die leichte Verarbeitung und sichert zudem die Stabilität des Betons. Das Betongemisch muss sehr gleichmäßig aufbereitet sein. Zudem dürfen keinerlei Löcher im Unterbau und der Betonmasse auftreten. Industrieböden werden zudem mit einer Verschleißschutzschicht versehen, die aus sog. Hartstoffen besteht. Diese wird durch rotierendes Glätten unlösbar in die Oberfläche des Betons integriert. Der Betonboden mit Schutzschicht muss unmittelbar nach dem Einbau mit einer Folie vor einer schnellen Austrocknung geschützt werden (Vermeidung von Rissbildung). Nach langsamer Austrocknung und gründlicher Reinigung wird eine Silicatlösung für besondere Oberflächeneigenschaften (hoch belastbar, verschleißfest, antistatisch, nicht brennbar, trittsicher, etc.) aufgetragen.
Je nach Entwurf können die Betonplatten durchgehend zweilagig bewehrt, stahlfaserbewehrt oder vorgespannt geplant werden. Entscheidend ist, dass Risse in der Betonplatte vermieden werden oder mit gewollten Rissen begrenzter Breite ausgeführt werden (2, rissarme Betonbodenplatten mit Fugen, fugenlose Betonbodenplatten mit Rissen begrenzter Breite, fugenlose Betonbodenplatten mit Spannlitzen ohne Risse). Scheinfugen, Pressfugen und Bewegungsfugen sollen die Bildung wilder Risse vermeiden.
Neben der Erfüllung der genannten Anforderungen muss der Betonboden auch gegen Öle, Fette und Kohlenwasserstoffe beständig sein. Flurförderzeuge wie Gabelstapler können Öl verlieren. Daher sollte die Porosität des Bodens sehr klein sein und unter drei Prozent liegen. Der Betonboden muss mit dem stützenden Unterbau einen Monolithen bilden, um ein Verrutschen und Absenkungen zu vermeiden.