Behälter: Schlüsselstellung im Materialfluss
Behälter spielen eine große Rolle im Materialfluss. Als Ladungsträger und Informationsübermittler sind sie ebenfalls bei der Prozessoptimierung im Unternehmen sehr bedeutsam.
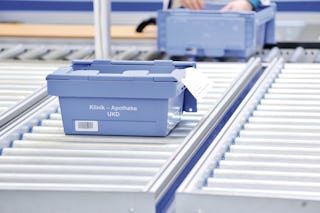
Das richtige Design bzw. die richtige Auswahl von Behältern sind für den unterbrechungsfreien Materialfluss im Unternehmen enorm wichtig. Sie fungieren nicht nur als Ladungsträger in der Logistik, sondern auch als Informationsübermittler und bilden damit die Grundlage für Kanban-Systeme. Auch in der Prozessoptimierung im Unternehmen spielen sie eine große Rolle. Das Behälterdesign hat z. B. auch enorme Auswirkungen auf die Laufeigenschaften und Geräuschentwicklung auf Förderstrecken. Damit sind sie ebenfalls ein wichtiger Bestandteil der Gestaltung von ergonomischen Arbeitsplätzen.
Nicht nur Ladungsträger
Der Materialfluss umfasst sämtliche Prozesse von der Gewinnung der Rohstoffe über die Be- und Verarbeitung bis hin zur Verteilung zum Lieferanten und den Weg zum Endverbraucher. Ebenso beinhaltet er Prozesse, die den Transport und die Logistik, die Lagerung, den Aufenthalt sowie die Prüfung des Produkts betreffen. Findet er im Unternehmen statt, spricht man vom innerbetrieblichen Materialfluss. Einher geht in der Regel auch ein Informationsfluss, der in Form von Daten erfasst, transportiert, verarbeitet und ausgegeben wird. Behälter spielen sowohl bei der Lagerung, dem Transport und der Informationsübermittlung eine wichtige Rolle. Allerdings lässt sich der Fluss des Materials erst durch die Standardisierung der Ladungsträger automatisieren. Die Ladungsträger wie Paletten, Boxen, Container, etc. müssen eindeutig definiert sprich genormt sein, damit Regalbediengeräte, Shuttle, Fahrerlose Transportsysteme (FTS), Flurförderzeuge und die Fördertechnik ihr Potenzial vollständig in die Logistik einbringen können. Beispielsweise sind Kleinladungsträger (KLT) - auch Eurokiste, Euronormbehälter oder Euronormbox genannt. Sie können daher einem gemeinsamen Recycling zugeführt werden. Die KLT wurden zur Optimierung der Logistikkette in der Automobilhersteller- und Zulieferindustrie entwickelt. Das System ist modular auf die Grundflächen 1200 × 800 mm (Europalette) und 1200 × 1000 mm (ISO) abgestimmt. Die Grundfläche verdoppelt sich jeweils und besitzt die Nennmaße 300 × 200 mm, 400 × 300 mm und 600 × 400 mm. Mittlerweile werden die Eurobehälter aufgrund ihrer Normung auch außerhalb der Autoindustrie eingesetzt. Behälter dienen ebenso aufgrund der eindeutigen Identifikations-Nummer (gespeichert auf Barcode, RFID) als Informationsträger. Im Lagerverwaltungssystem (LVS) oder im Materialflussrechner ist diese ID mit einem bestimmten Artikel oder Auftrag verknüpft. Dadurch ist eine automatische Erkennung- und Steuerung der Behälter und der Waren im Lager möglich.
Beispiele für funktionelles Behälterdesign
Die mechanischen Eigenschaften moderner Boxen erlauben vielfältige Operationen in der Logistik. Beispielsweise sollen Behälter auf der Fördertechnik möglichst reibungsarm und leise laufen. Zudem existieren extrem kleine Toleranzen für die Durchbiegung des Behälterbodens. Beispielsweise wurde der XL-Motion von BITO speziell für automatisierte Lager ausgelegt, sodass er die Anforderungen an Ebenheit, Rauheit und an den Reibwert optimal erfüllt. Dafür sorgt der neuartige Umlaufboden. Um bei hohen Belastungen im Lagerbetrieb bestehen zu können, wurde er mit einer glatten Rahmenkonstruktion versehen, die mit diagonalen Stützrippen an die Box angebunden ist. Diese Sandwichkonstruktion verhindert, dass sich der Boden bei hoher Last durchbiegt. Weil er dadurch immer eben und glatt ist, läuft der XL-Motion auf der Fördertechnik äußerst leise. Das sorgt für eine erheblich angenehmere Arbeitsatmosphäre im Lager. Die geringe Lautstärke führt nicht nur zu weniger Stress und damit geringeren Ausfallzeiten, sondern auch zu weniger Fehlern und zu einer höheren Arbeitszufriedenheit.
Tablare werden in automatischen Kleinteilelagern eingesetzt, um nicht förderfähige Waren, wie z. B. Kartonagen, transportieren und einlagern zu können. Sie sind speziell auf die Anforderungen der jeweiligen Fördertechnik zugeschnitten. Für das automatische Be- und Entladen existiert eine Aushebefunktion, durch die die auf dem Tablar befindlichen Güter vom Tablar getrennt werden. Danach kann z. B. das Stapeln der Güter auf Paletten vorgenommen werden.
Kanban-Systeme und Behälter
Kanban ist eine Methode der dezentralen Produktionssteuerung, bei der mithilfe von Datenkarten – japanisch Kanban genannt - einzelne Produktionsprozesse und Logistikprozesse angestoßen werden. Die Vorteile der Kanban-Methode sind die dezentrale Steuerung, eine schlanke Lagerhaltung (Lean Lager) und Just-In-Time-(JIT)Logistik von Teilen, die in der Produktion benötigt werden. Auf den Karten sind wichtige Daten, wie Artikelnummer, Menge, Lagerort, etc., vermerkt. Die Produktion sendet also an die vorgeschaltete Produktionsstufe ein Signal, dass neue Bauteile benötigt werden. Z. B. wird ein leerer Behälter mit Bestellkarte für ein bestimmtes Bauteil in das (Lean) Lager gesendet und ein voller Behälter wieder mitgenommen. Das Teilelager weiß jetzt, dass dieser Artikel in einer bestimmten Menge nachbestellt werden muss und sendet diesen Bestellauftrag an die Quelle (den Lieferanten). Der Lieferant erfüllt den Auftrag und bringt das entsprechende Bauteil in der gewünschten Menge in das Lager. Die Kanban-Karte dient also als Bestellkarte der Produktion, die einen bestimmten Produktionsauftrag bzw. eine Resonanzwelle auslöst. Beim Kanban-System muss kein Einzelner über die gesamte Prozesskette Bescheid wissen. Es wird immer nur der offene Kanban-Behälter an der jeweiligen lokalen Stelle aufgefüllt. Das System erweist sich also als selbstregulativ und selbstorganisierend und beruht auf lokalem Wissen und einfachen Regeln. Heutzutage werden statt der Kanban-Karte Speichermedien wie Barcodes oder RFID-Chips eingesetzt. Dabei werden die Daten bzw. der Produktionsauftrag via WIFI an das Lagerverwaltungssystem, ERP-System bzw. an den entsprechenden Bauteilelieferanten übertragen.
Ausgangspunkt für Prozessoptimierungen
Besonders im Zeitalter von Industrie 4.0 sollten die Abläufe und Prozesse auch in kleineren Unternehmen optimiert und verschlankt werden. Ein guter Ansatzpunkt ist hier der Transport- und Materialfluss. Dabei sollten insbesondere die Durchlaufzeiten für Materialien und Produkte überprüft werden. Durchlaufen diese unnötige Stationen und lassen sich Bearbeitungszeiten evtl. verkürzen? Jede Verringerung von Durchlaufzeiten bedeutet eine Kostenersparnis. Wird an jeder Stelle des Unternehmens das optimale Transportmittel eingesetzt? Sind evtl. Sonderkonstruktionen notwendig? Ebenso wichtig sind natürlich die Transportbehälter. Werden die passenden Transportbehälter für die Produkte, Arbeitsstationen und Prozesse eingesetzt? Hier lässt sich die Lagerhaltung, der Transport bzw. die Intralogistik entscheidend rationalisieren, wodurch die Kosten gesenkt werden können.
Bedeutung von Regalen im Materialfluss
Regale sind in der Regel die Quelle oder Senke des Materialflusses. D. h. die Ware wird aus dem Regal entnommen und in den Fluss des Materials eingeschleust oder die Güter kommen aus dem Wareneingang oder der Produktion und werden zu den Regalen befördert und eingelagert. Mitunter findet aber auch in Regalen ein Materialfluss statt, beispielsweise in Durchlaufregalen für Paletten oder Behälter und Kartons. Das kann entweder eine Nachschubaktion im Rahmen eines Kanban-Systems oder eine Nachschubsteuerung in Rahmen einer Kommissionierung sein. Dabei garantiert das Durchlaufregalsystem durch seine Fließrichtung von der Einlagerungsseite zur Auslagerungsseite hin automatisch eine Bewegung nach dem FIFO-Prinzip (First-in, First-Out). Eine weitere Funktion im Materialfluss nehmen Zwischenpuffer ein. Bei einer mehrstufigen Kommissionierung müssen beispielsweise die "ankommissionierten" Auftragsbehälter meist in einem Regal auf die weiteren Positionen warten.
Sie möchten Ihren Materialfluss effizienter gestalten? Wir helfen Ihnen dabei.