Kaizen: zavázán k neustálému zlepšování
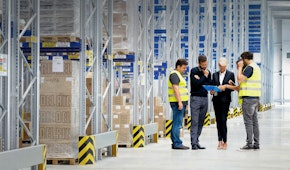
Za japonským termínem „Kaizen“ stojí filozofie, která může být použita v mnoha oblastech života, ale také v průmyslových procesech. Kaizen znamená „změna k lepšímu“ a zahrnuje myšlenku nebo životní filozofii, která je zaměřena na nepřetržitou a nekonečnou optimalizaci nebo změnu. Změny a vylepšení procesů ve výrobní logistice se provádějí postupně a selektivně. Počátky Kaizenu lze vysledovat až do 50. let, kdy poválečné Japonsko leželo v troskách. V té době musela Toyota najít řešení odborového sporu, který vyústil v zapojení všech zaměstnanců do procesu nepřetržité optimalizace. Záruka celoživotního zaměstnání znamenala, že lidský kapitál musel být nesmírně ziskový. Dávalo smysl neustále zlepšovat dovednosti pracovníků a účinně využívat jejich znalosti, zkušenosti a pracovní výkon. Toyota představila Kaizen mezi mnoha dalšími principy, jako je Kanban, dodávka komponentů Just-In-Time (JIT), Kenbutsu (zapojení dodavatelů) atd. do výrobního systému Toyota (TPS) v automobilovém průmyslu. Podle známého inženýra a manažera výroby společnosti Toyota Taiichi Ohno je výchozím bodem konceptu TPS odstranění veškerého odpadu. Definoval také sedm druhů odpadu. Ačkoli kniha Taiichiho Ohna „Toyota Production System: Beyond Large-Scale Production“ byla přeložena do angličtiny v 80. letech, Kaizen se poprvé stal na Západě známým prostřednictvím japonského konzultanta pro management Masaaki Imai a jeho knihy „Kaizen: Japonský duch zlepšování“. Lean Production a Lean Management byly v zásadě již použity. Následně byl tento koncept přijat do západní ekonomiky a dále se vyvinul do systému řízení známého v praxi jako proces kontinuálního zlepšování (CIP).
Základy Kaizenovy metody
Kaizen je způsob myšlení, který je realizován všemi zaměstnanci a ve všech procesech společnosti. Pět centrálních základů Kaizenu je: Procesní orientace, orientace na zákazníka, orientace na kvalitu, orientace na kritiku a standardizace.
Přesunem od čisté orientace na výsledek k orientaci na proces a optimalizaci zisku prostřednictvím neustálé optimalizace procesů je nevyhnutelná orientace na zákazníka. Protože optimalizace zisku je možná pouze s vysokou spokojeností zákazníků, protože získávání zákazníků je dražší než navázání vztahu s novými zákazníky. Existují však externí i interní zákazníci (pobočky, organizační a výrobní jednotky). Problémy se často objevují na rozhraní mezi těmito organizačními jednotkami, a proto je hlavní důraz kladen na implementaci optimalizací a cílů Kaizen - zajištění a zvyšování kvality, spokojenost zákazníků a snižování nákladů zaměstnanci. V rámci Total Quality Managementu je prováděna stálá Total Quality Control, ve které je kvalita průběžně sledována během výroby komplikovaným měřicím postupem. Pro mnoho lidí to není snadné přijmout, ale v Kaizenu je kritika vnímána jako příležitost k neustálému zlepšování. Řízení by však nemělo obsahovat pouze kritiku, ale také návrhy na zlepšení. Návrhy budou přezkoumány a vyhodnoceny z hlediska použitelnosti a pokud možno budou provedeny. Výsledkem je nepřetržitý cyklus plánování, provozu, řízení a zlepšování, cyklus PDCA (Plánovat → Dělat → Kontrolovat → Jednat). Standardně se stanoví vhodné vylepšení. Tento standard však stále podléhá vylepšení.
Nástroje a metody
V Kaizenu existuje mnoho nástrojů a metod, které mohou zviditelnit příčiny všech druhů chyb a původ odpadů ve společnosti. Ukazují, kde a jak mohou být změny provedeny. Jejich aplikace je relativně jednoduchá, ale jen nasazením u všech zaměstnanců je možné dosáhnout významných změn. Některé příklady jsou: 5S / 5A, Kaizen workshopy k projednání návrhů na zlepšení, 3-Mu kontrolní seznam, 6-W kontrolní seznam, Ishikawa diagram pro analýzu kořenových příčin, 5 Proč otázek, Gemba-Walks, Kanban, Poka Yoke a mnoho dalších.
5 proč otázek
Toto je technika dotazování, která má prozkoumat původ výzvy. Podle filosofie Kaizen by metoda měla být užita k určení výzvy. První se například ptá: „Proč se to stalo?“, přičemž příslušná odpověď tvoří základ pro další otázku. Ne všechny výzvy mají jednu základní příčinu. Proto může být nutné položit pro každou příčinu jinou sekvenci 5 proč otázek. Výsledek vždy závisí na znalostech a vytrvalosti zúčastněných osob.
Příklad:
Výzva: Vysokozdvižný vozík se nespustí.
- Proč? Baterie je vybitá.
- Proč? Alternátor nefunguje.
- Proč? Roztrhaný řemen ventilátoru.
- Proč? Řemen ventilátoru byl již starý a nezměnil se.
- Proč? Vysokozdvižný vozík nebyl řádně opraven. (Příčina)
5S/5A
V metodě 5S/5A zaměstnanec analyzuje své pracovní prostředí z hlediska odpadu a zbytečných činností a zahajuje vhodná opatření k jejich odstranění. To vše začíná písmenem „S“ v japonštině.
- Seiri: Odstraňte nepotřebné položky ze svého pracovního prostoru.
- Seiton: Objednejte věci, které zůstaly po Seiri.
- Udržujte své pracoviště čisté.
- Seiketsu: Ukliďte a uspořádejte si osobní věci.
- Shitsuke: Udělejte z 5S zvyk stanovením standardů.
Workshopy Kaizen
Všichni zaměstnanci se pravidelně setkávají se svými nadřízenými, aby prodiskutovali, jaké problémy se vyskytly a jaká opatření by měla být přijata pro jejich zlepšení. Jsou zkoumána pracoviště, pracovní oblasti a situace „na místě“, věci jsou sledovány a analyzovány naživo. Pokud je to možné, vylepšení jsou implementována a vyzkoušena přímo. Témata schůzky mohou být například:
- operační procesy, zdvojování práce, zbytečné činnosti
- problémy s kvalitou a nedostatky v produktech, nástrojích nebo strojích
- chybná organizace pracovního místa
- zpoždění v jednotlivých činnostech a procesech
- racionalizace, které zjednodušují nebo zrychlují procesy
- a mnohé další
Aby bylo možné přímo implementovat a testovat vylepšení z workshopů Kaizen, je užitečné pracovat s technologiemi a nástroji, které mohou sami zaměstnanci optimalizovat podle svých potřeb. Příklad z BITO: S dopravním systémem „LEO Locative“ bez řidiče mohou zaměstnanci nastavit nebo „programovat“ své vlastní trasy nebo příkazy, dokud nejsou optimálně přizpůsobeny jejich požadavkům. Zaměstnanci nepotřebují externí IT podporu, nepotřebují žádat o dodatečný rozpočet na realizaci, což jim umožňuje pružně se přizpůsobit všem okolnostem.
Kontrolní seznam 3-Mu
Pomocí kontrolního seznamu lze odhalit zdroje odpadu a příčiny problémů.
- Muda: Odpad
- Muri: Přetížení
- Mura: Odchylka od standardů nebo pravidel
V těchto třech oblastech jsou kontrolovány například tyto okruhy: Zaměstnanci, technologie, metody, čas, kreativní rozsah, zařízení a nástroje, materiál, objem výroby, přeprava, oběh, prostor, pohybové sekvence (ergonomie), způsob myšlení (myšlení).
Sedm druhů odpadu (mudas)
- nadprodukce
- čekací doba
- zbytečná přeprava
- výroba vadných dílů
- nadměrné skladování
- zbytečný pohyb
- nepříznivý výrobní proces
Cíle a výhody pro logistiku uvnitř a ve výrobě
V zásadě lze Kaizen aplikovat na jakoukoli oblast a proces. V průmyslových procesech je hlavním cílem optimalizovat zisky zamezením plýtvání (viz sedm druhů odpadu), čehož je dosaženo prostřednictvím procesů, zákazníků, kvality, kritiky a standardizace - a zároveň neustále optimalizovat tyto oblasti. Jak ukázal příklad workshopu Kaizen v LEO Locative, zaměstnanci mají větší volnost při optimalizaci procesů v malých krocích i podle svých požadavků ve smyslu Kaizen. To vytváří větší pocit odpovědnosti a spokojenosti zaměstnanců, a proto zvyšuje motivaci a efektivitu. Návrhy řešení od pracovníků mohou a měly by být také odměňovány, aby se zvýšila motivace. Neustálé uplatňování jednoduchých pravidel ke zlepšení procesů ve všech sektorech vytváří hmatatelné změny. To také znamená, že člověk nečeká na dokonalé řešení, ale dává přednost jednoduchým, ale účinným řešením. Všichni zaměstnanci a oddělení jsou vždy zapojeni do Kaizenu. Problémy jsou zde příležitosti nebo výzvy a jsou považovány za hnací sílu procesu zlepšování. Konkrétním příkladem Kaizenu v intralogistice je neustálá optimalizace dopravních tras ve skladu. Odpověď na mnoho otázek lze nalézt přímo v pracovním prostředí. Kreativita a inteligence všech zaměstnanců v procesu Kaizen jsou vyžadovány a k implementaci často není zapotřebí ani velké množství kapitálu. Filozofie také ukazuje, že žádný proces není nikdy plně optimalizován. Další malý optimalizační krok se objeví hned po právě dokončeném.